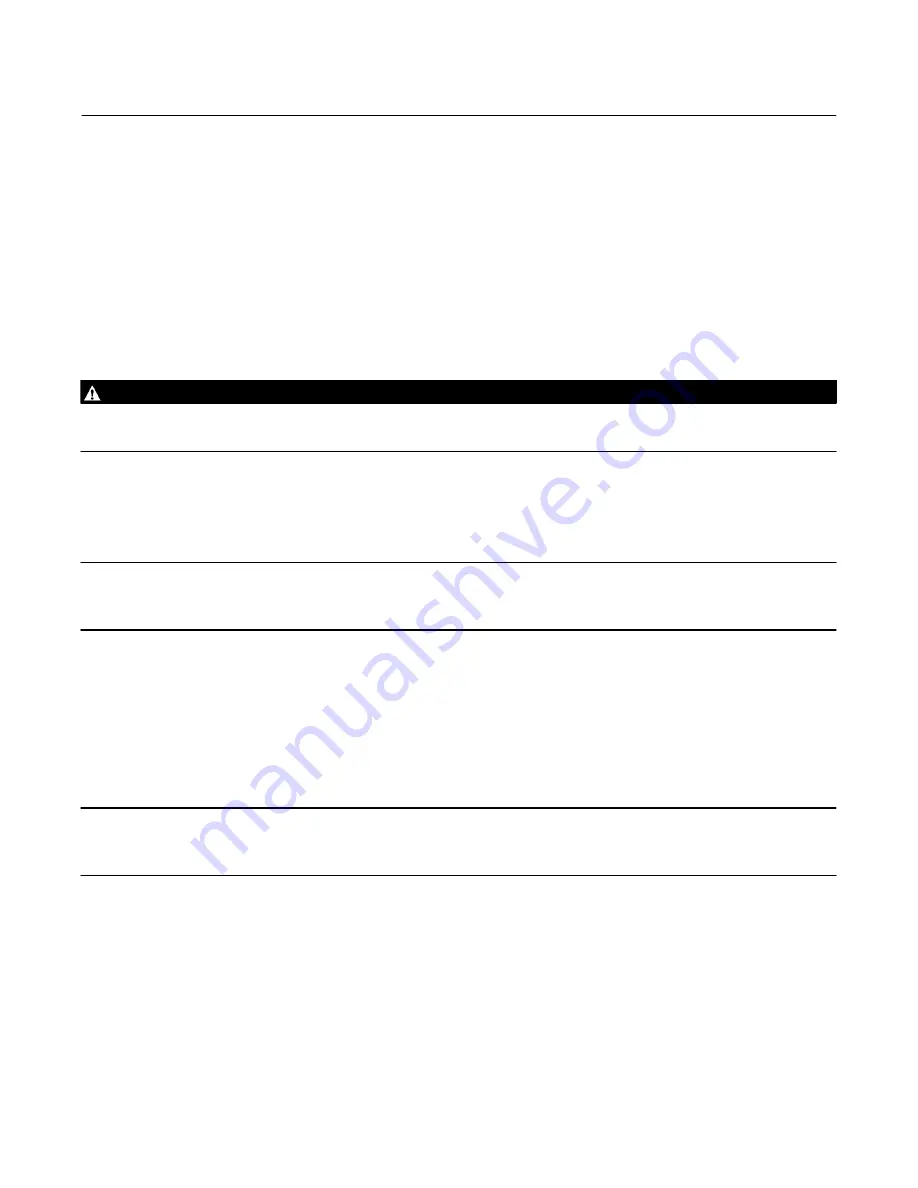
Instruction Manual
D200156X012
4194HA, HB, HC Controllers
July 2018
63
Refer to figure 6‐1 (4194HB or 4194HC controllers, suffix letter F) for key number locations.
1. Perform the procedures required in the Note above.
2. Loosen the nuts at both ends of the relief valve tubing (key 44) and remove the tubing.
3. Install the replacement relief valve tubing and tighten the tubing nuts at both ends.
4. Apply the proper supply pressure to the controller. Check for leaks.
5. Install the controller assembly in the case and cover.
6. Perform the process zero‐and‐span adjustment procedure and the flapper alignment procedure.
Calibration After Controller Maintenance
WARNING
To avoid personal injury or property damage resulting from the sudden release of pressure, do not exceed the operating
limits given in this manual.
Process Indicator Zero‐and‐Span Calibration
Note
For routine zero‐and‐span calibration, refer to the appropriate procedures in Section 3 or 4. Use the following maintenance
zero‐and‐span procedure only if difficulty is encountered with the routine procedure or if nonlinearity occurs.
Refer to figure 3‐1 for location of adjustments and figure 6‐1 for key number locations.
Provide a regulated process differential pressure to the differential pressure unit. Provide a regulated supply pressure
to the controller. Do not exceed normal operating pressure (table 1‐4). For a 4194HA controller, connect the
controller output to an accurate gauge. For 4194HB and HC controllers, a gauge is not necessary and the controller
output connection may be plugged.
Note
Any adjustment of the process indicator span adjustment screw requires readjustment of the process indicator zero adjustment
screw.
1. Remove the two machine screws (key 6) and lift off the proportional band indicator cover (key 36).
2. Set the proportional band adjustment between DIRECT and REVERSE.
3. Adjust the reset valve (4194HB and HC controllers only) to 0.01 minutes per repeat.
4. Adjust the rate valve (4194HC controllers only) to OFF.
5. Adjust the process differential pressure to 50 percent of the process scale range.
6. The process indicator should be aligned with the indicator subassembly as shown in figure 5‐6. If not, loosen the
zero adjustment locking screw and adjust the zero adjustment screw to align the process indicator with the
indicator subassembly. Tighten the zero adjustment locking screw.