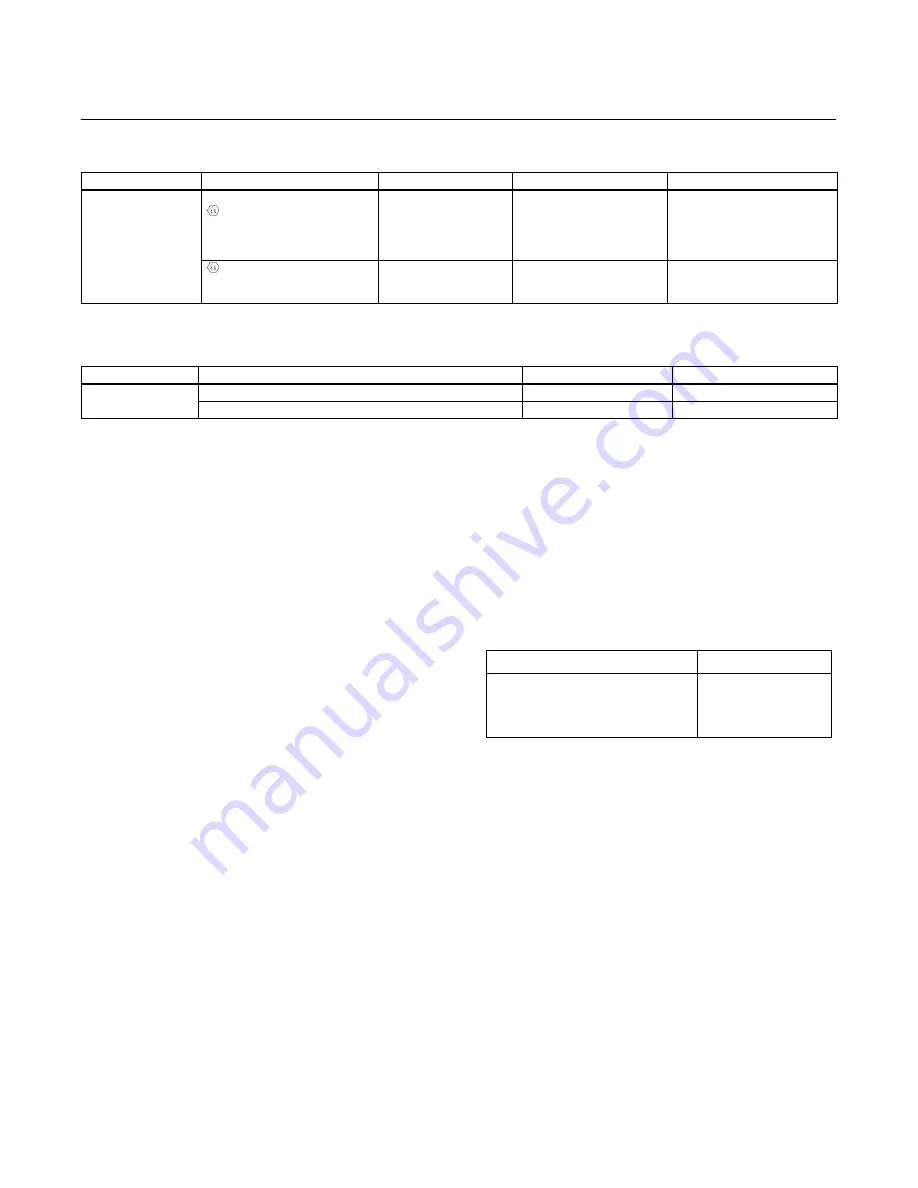
3660 and 3661 Positioners
Instruction Manual
Form 5265
March 2006
6
Table 4. Hazardous Area Classifications for Type 3661—ATEX
CERTIFICATE
CERTIFICATION OBTAINED
ENTITY RATING
TEMPERATURE CODE
ENCLOSURE RATING
ATEX
II 1 G —Intrinsic Safety
Gas
EEx ia IIC T4/T5/T6
U
i
= 30 Vdc
I
i
= 150 mA
P
i
= 1.25 W
C
i
= 0 nF
L
i
= 0 mH
T4 (T
amb
v
82
°
C)
T5 (T
amb
v
62
°
C)
T6 (T
amb
v
47
°
C)
IP44
II 3 G
Gas
EEx nA IIC T6 —Type n
−
−
−
T6 (T
amb
v
82
°
C)
IP44
Table 5. Hazardous Area Classifications for Type 3661—Australia (SAA)
CERTIFICATION
CERTIFICATION OBTAINED
TEMPERATURE CODE
ENCLOSURE RATING
SAA
Ex ia IIC —Intrinsic Safety
T4 (T
amb
v
40
°
C)
IP54
Ex n IIC —Type n
T4 (T
amb
v
40
°
C)
IP54
ATEX Intrinsic Safety
Type 3661
Special Conditions for Safe Use
This
equipment is intrinsically safe and can be used
in potentially explosive atmospheres.
The electrical parameters of certified equipment
which can be connected to the device must not
exceed the following value:
U
0
30 Vdc; I
0
150 mA; P
0
1.25 W.
Ambient Temperature:
T6, at T
amb
= 47
_
C
T5, at T
amb
= 62
_
C
T4, at T
amb
= 71
_
C
Refer to table 4 for additional approval information
and figure 30 for the ATEX approvals nameplate.
ATEX Type n
Type 3661
Special Conditions for Safe Use
The Type 3661 has an IP44 ingress protection: it is
only intended to be installed in an area where a
convenient protection is ensured against the entry of
solid foreign bodies and liquids which may decrease
the safety.
Refer to table 4 for additional approval information
and figure 30 for the ATEX approvals nameplate.
SAA Intrinsic Safety, Type n
Type 3661
Conditions of Certification
1. It is a condition of certification that the following
parameters are taken into consideration during
installation when the equipment is used as an Ex ia
apparatus:
Input Parameters
2-Way terminal block
Maximum Input Voltage U
i
Maximum Input Current I
i
Maximum Internal Capacitance C
i
Maximum Internal Inductance L
i
32 V
150 mA
0
µ
F
0 mH
2. It is a condition of safe use that the input voltage
does not exceed 32 Volts when the equipment is
used as an Ex n apparatus.
3. It is a condition of safe use that the equipment
shall be mounted such that the exhaust vents will be
self-draining.
4. It is a condition of safe use that the cable gland or
conduit adaptor with an ingress protection rating of
IP54 must be used in the conduit entry in order to
maintain the IP rating of the enclosure.
5. It is a condition of safe use that the irrelevant
explosion protection marking codes on the
certification label are permanently scribed off upon
completion of commissioning.
Refer to table 5 for additional approval information,
and figure 31 for the SAA approvals nameplate.