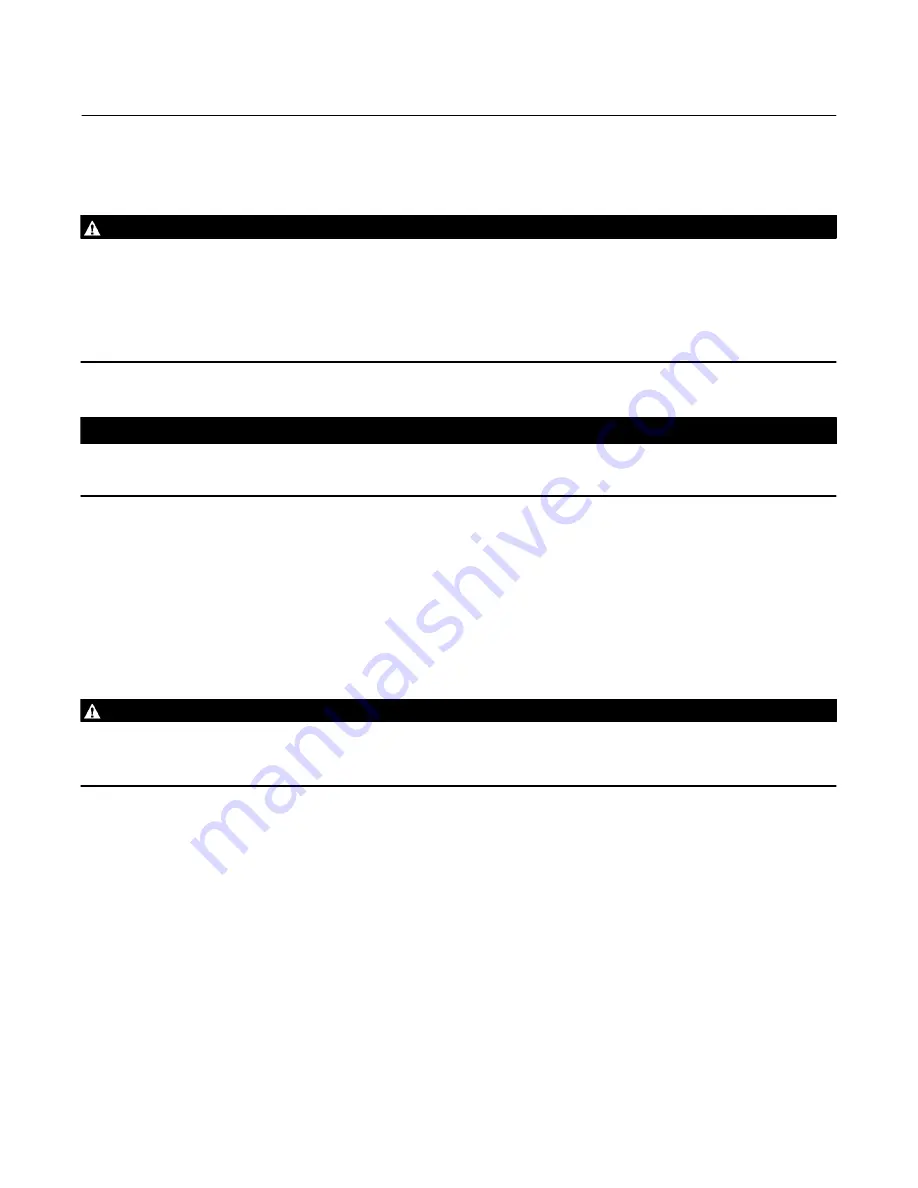
Instruction Manual
D200126X012
2502 Controllers
June 2017
12
Vent Assembly
WARNING
Personal injury or property damage could result from fire or explosion of accumulated gas, or from contact with hazardous
gas, if a flammable or hazardous gas is used as the supply pressure medium. Because the instrument case and cover
assembly do not form a gas‐tight seal when the assembly is enclosed, a remote vent line, adequate ventilation, and
necessary safety measures should be used to prevent the accumulation of flammable or hazardous gas. However, a remote
vent pipe alone cannot be relied upon to remove all flammable and hazardous gas. Vent line piping should comply with
local and regional codes, and should be be as short as possible with adequate inside diameter and few bends to reduce case
pressure buildup.
CAUTION
When installing a remote vent pipe, take care not to overtighten the pipe in the vent connection. Excessive torque will
damage the threads in the connection.
The vent assembly (see figure 3) or the end of a remote vent pipe must be protected against the entrance of all foreign
matter that could plug the vent. Use 13 mm (1/2-inch) pipe for the remote vent pipe, if one is required. Check the vent
periodically to be certain it has not become plugged.
Prestartup Checks
WARNING
The following procedure requires taking the controller out of service. To avoid personal injury and property damage caused
by an uncontrolled process, provide some temporary means of control for the process before taking the controller out of
service.
Adjustment locations are shown in figure 9 unless otherwise indicated. When performing the checks open loop
conditions must exist. To obtain open‐loop conditions:
D
make sure there is no process flow through the final control element, or
D
disconnect the controller output signal line and plug the output connection.
During startup, it is necessary to change process levels to position the displacer from its maximum to its minimum
range of operations. Provide a means to change the process level or interface. If the process variable cannot be varied
sufficiently, follow the instructions in the Calibration section to simulate the process variable changes required for
these checks.
Make sure that the RAISE LEVEL dial on the controller is mounted with the correct side facing out. The dial is printed on
both sides with the arrow on one side pointing to the left and the arrow on the other side pointing to the right. Figure 9
shows the dial arrow positioned for a sensor that is mounted to the left of the controller; the arrow points to the left. If