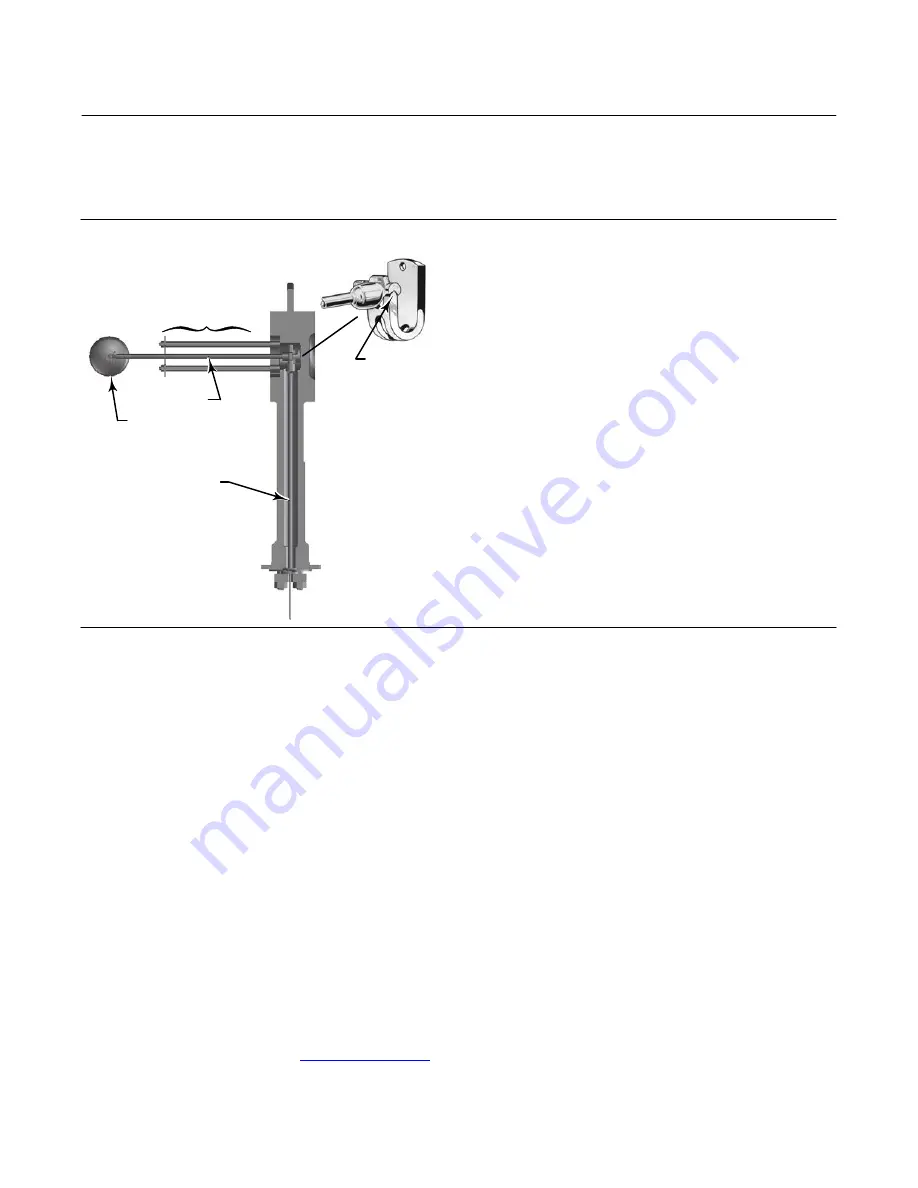
Instruction Manual
D103288X012
249VS Sensor
July 2018
2
A torque tube assembly (figure 2) and displacer provide an indication of liquid level, interface level, or density/specific
gravity. The torque tube assembly consists of a hollow torque tube with a shaft welded inside it at one end and
protruding from it at the other end.
Figure 2. Side‐Mounted Cageless Wafer‐Style Sensor Assembly
KNIFE EDGE BEARING
TRAVEL STOP
ASSEMBLY
DISPLACER ROD
DISPLACER
TORQUE TUBE
W1800‐1
W9353
The unconnected end of the tube is sealed by a gasket and clamped rigidly to the torque tube arm, permitting the
protruding end of the shaft to twist and therefore transmit rotary motion. This allows the interior of the torque tube to
remain at atmospheric pressure, thus eliminating packing and the disadvantages of packing friction.
The displacer always exerts a downward force on one end of the displacer rod. The other end of the displacer rod rests
on the knife‐edge of the driver bearing. A keyed shaft on the bearing end of the displacer rod fits into a socket on the
outside of the welded end of the torque tube assembly.
A change in liquid level, interface level, or density/specific gravity buoys up the displacer by a force equal to the weight
of the liquid displaced. Corresponding vertical movement of the displacer results in angular movement of the displacer
rod around the knife edge. Since the torque tube assembly is a torsional spring which supports the displacer and
determines the amount of movement of the displacer rod for a given displacement change, it will twist a specific
amount for each increment of buoyancy change. This rotation is brought through the torque tube arm by the
protruding rotary shaft. A controller or transmitter attached to the end of the rotary shaft converts the rotary motion
into varying pneumatic or electric signals. Figure 3 shows how the controller or transmitter mounts on the torque tube
arm.
The 249VS wafer‐style sensor mates with cast iron CL125 flat face and CL250 raised face flanges, and CL150, 300, 600,
900, and 1500 raised face steel flanges. The 249VS is also available with CL600, 900, 1500, and 2500 butt weld end
process connections.
Unless otherwise noted, all NACE references are to NACE MR0175‐2002.
The Parts List section shows some standard 249VS displacer lengths. Table 1 contains displacer and torque tube
materials. However, 249VS parts are available in a wide variety of materials of construction, part dimensions, and
other specifications. Contact your
Emerson sales office
or Local Business Partner for assistance in selection of specific
materials, dimensions, and specifications.