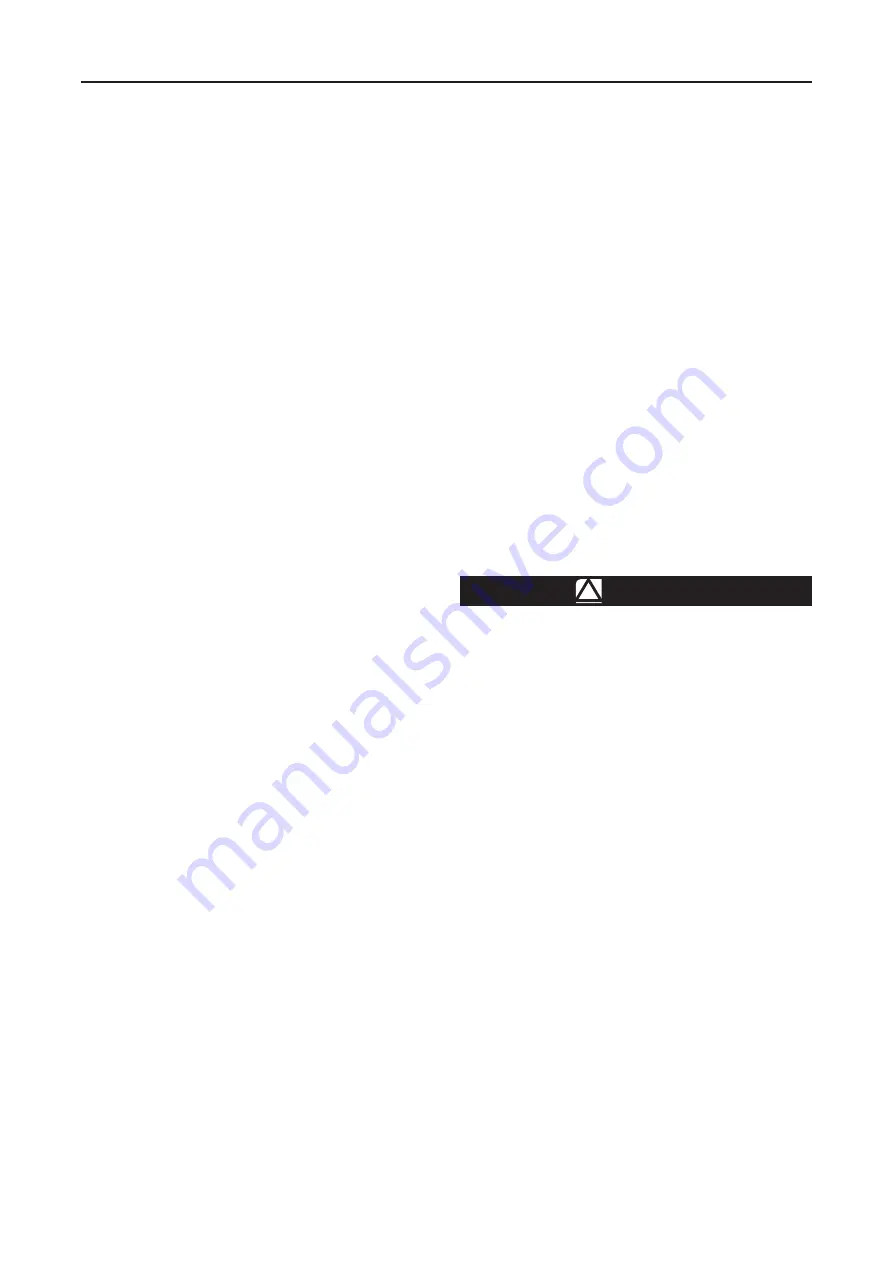
2
167D Series
To avoid such injury or damage,
provide pressure-relieving or pressure-
limiting devices (as required by
the appropriate code, regulation,
or standard) to prevent service
conditions from exceeding limits.
Additionally, physical damage to
the switching valve could result in
personal injury and property damage
due to escaping fluid. To avoid
such injury and damage, install the
switching valve in a safe location.
Clean out all pipelines before installation of the
switching valve and check to be sure the switching
valve has not been damaged or has collected
foreign material during shipping. For NPT bodies,
apply pipe compound to the external pipe threads.
Install the switching valve in any position desired,
unless otherwise specified, but be sure flow through
the body is in the direction indicated by the arrow on
the body.
Note
It is important that the switching valve
be installed so that the vent hole in
the spring case is unobstructed at all
times. For outdoor installations, the
switching valve should be located
away from vehicular traffic and
positioned so that water, ice, and other
foreign materials cannot enter the
spring case through the vent. Avoid
placing the switching valve beneath
eaves or downspouts, and be sure it is
above the probable snow level.
Overpressure Protection
The recommended pressure limitations are stamped
on the switching valve nameplate. Some type of
overpressure protection is needed if the actual inlet
pressure exceeds the maximum operating outlet
pressure rating. Overpressure protection should
also be provided if the switching valve inlet pressure
is greater than the safe working pressure of the
downstream equipment.
Switching valve operation below the maximum
pressure limitations does not preclude the possibility
of damage from external sources or debris in the
line. The switching valve should be inspected for
damage after any overpressure condition.
*Recommended spare part.
Startup
The switching valve is factory set at approximately
the midpoint of the spring range or at the pressure
setting specified on the order. The allowable spring
range is stamped on the nameplate. If a pressure
setting other than specified is desired, be sure to
change the pressure setting by following the proper
procedure as mentioned in the Adjustment section.
With proper installation completed and relief valves
properly adjusted, slowly open the upstream and
downstream shut-off valves.
Adjustment
If outlet pressure adjustment is necessary, monitor
outlet pressure with a gauge during the adjustment
procedure. The switching valve is adjusted by
loosening the hex nut, if used, and turning the
adjusting screw or handwheel clockwise to increase
or counterclockwise to decrease the outlet pressure
setting. Retighten the hex nut to maintain the
adjustment position.
Taking Out of Service (Shutdown)
!
WARNING
To avoid personal injury resulting from
sudden release of pressure, isolate
the switching valve from all pressure
before attempting disassembly.
Parts List
167D Series
Key Description
1 Body
3
Flange Screw
7
Spring Case Assembly
11
Valve Stem
12
*
Valve Spring
14
*
O-ring (Spring Retainer)
15
Soft Seat (for Types 167D and 167DS only)
16
*
Diaphragm Assembly
17
Control Spring
18
Adjusting Screw
19
Hex Nut
20
Upper Spring Seat
23
1/4 NPT Pipe Plug
30
NACE Tag (not shown)
31
Panel Mounting Nut
32
Wire Seal (not shown)
33
Closing Cap
45
Screen Vent (for Types 167DS and 167DAS only)
48
Spring Retainer
50
*
O-ring (Stem and Plug)
57
Valve Plug
58
*
Seat
64
Retaining Ring