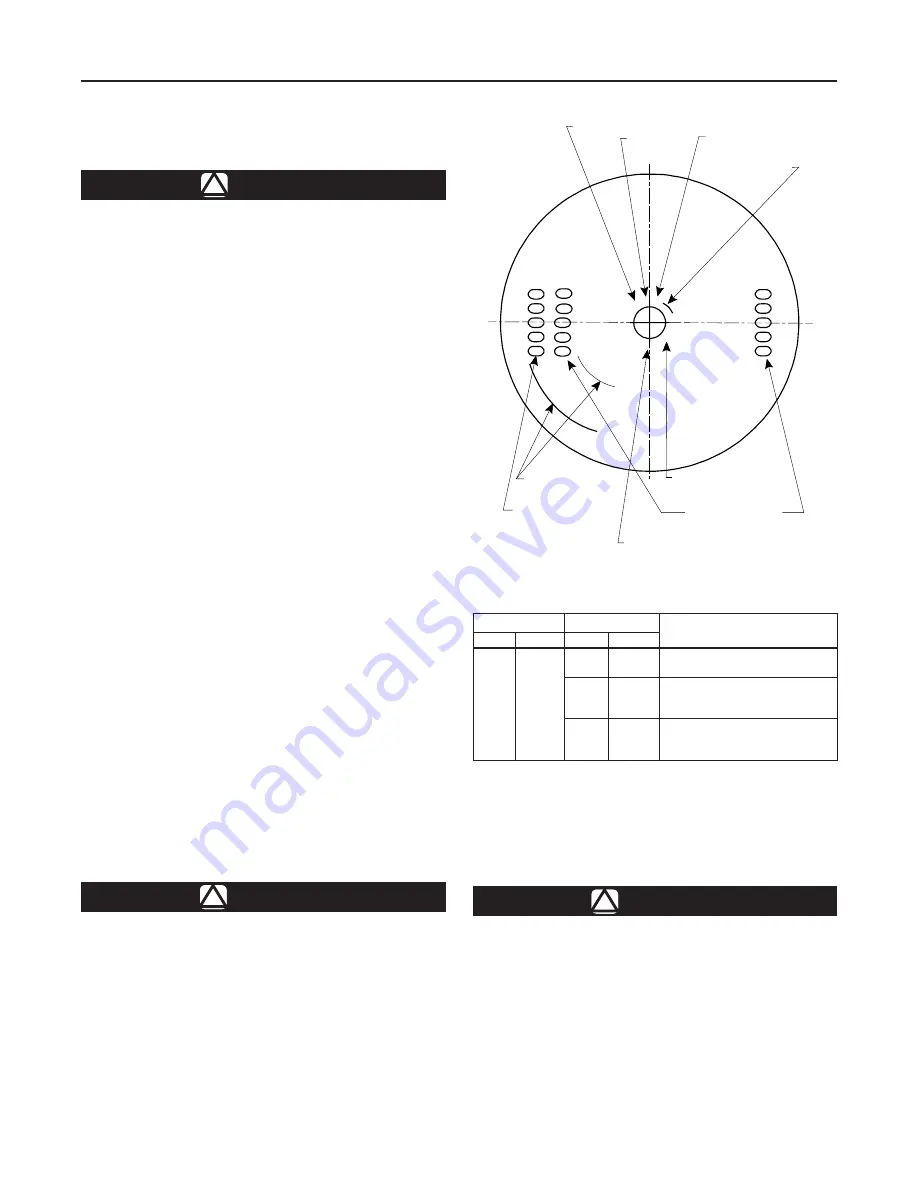
Shutdown for Both Single-Regulator and
Monitoring Installations
!
WARNING
If pilot supply pressure is shut down
first, the downstream system may be
subjected to full inlet pressure.
1. If the pilot setting must be disturbed, be sure to
keep some tension on the spring. This will prevent
trapping inlet pressure during blow down.
2. Close the valves shown in Figure 3 or 4, in the
following order:
a. Inlet block valve
b. Outlet block valve
c. Control line valve(s), if used
3. Open the vent valves to depressurize the system.
Maintenance
Regulator parts are subject to normal wear and
must be inspected periodically and replaced as
necessary. Due to the care Emerson takes in meeting
all manufacturing requirements (heat treating,
dimensional tolerances, etc.), use only replacement
parts manufactured or furnished by Emerson. Also,
when lubrication is required, use a good quality
lubricant and sparingly coat the recommended part.
The frequency of inspection and parts replacement
depends upon the severity of service conditions,
applicable codes and government regulations and
company inspection procedures. Table 12 lists various
regulator problems and possible solutions for them.
Type EZR Main Valve Trim Parts
Instructions are given for complete disassembly and
assembly. The main valve body may remain in the
pipeline during maintenance procedures. Key numbers
are referenced in Figures 14 through 18.
CAUTION
Avoid personal injury or damage to
property from sudden release of pressure
or uncontrolled gas or other process
fluid. Before starting to disassemble,
carefully release all pressures according
to the Shutdown procedure. Use gauges
to monitor inlet and outlet pressures
while releasing these pressures.
Converting a Fisher™ E-Body to Type EZR
Remove all trim parts from the main valve and clean
the body interior. Then follow procedure in Assembly
section to convert a Fisher E-body to a Type EZR.
CAUTION
When installing a Type EZR trim package
make sure flow is up through the center
of the cage and down through the cage
slots. In some cases, correct flow path
is achieved by removing the body from
the line and turning it around. If this is
done, change the flow arrow to indicate
the correct direction. Damage may result
STYLE
MATERIAL
DIAPHRAGM MATERIAL
Imprint Ink Mark Imprint Ink Mark
2
130
2
17E68
17E68 - Nitrile (NBR)
(low temperature)
4
17E88
17E88 - Fluorocarbon (FKM)
(high aromatic hydrocarbon
content resistance)
5
17E97
17E97 - Nitrile (NBR)
(high pressure and/or
erosion resistance)
Table 11.
Diaphragm Imprint Codes
1
1
1
1
1
1 11
Figure 8.
Diaphragm Markings
LOCATE INK CODE
BETWEEN RADII
MATERIAL
INK CODE
MANUFACTURER
CODE
THICKNESS INK
CODE (USE ONE
LOCATION ONLY)
DOME IDENTIFICATION
ELASTOMER/FABRIC
MATERIAL CODE
THICKNESS
CODE
YEAR OF MANUFACTURE
RADIAL LOCATION
TO LOCATE
IMPRINT CODE
16
Type EZR