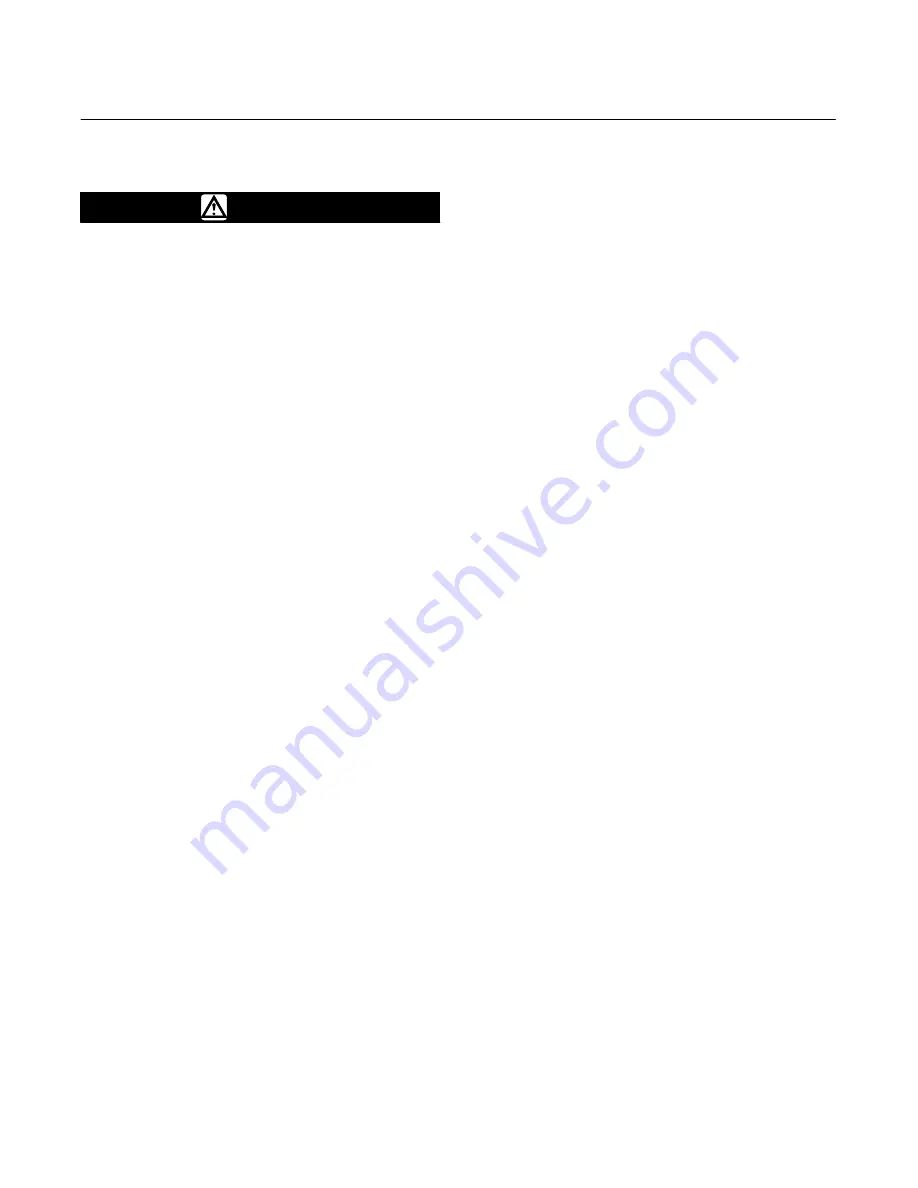
1077 Actuator
Instruction Manual
Form 5605
March 2007
8
Maintenance
WARNING
Avoid personal injury or property
damage from sudden release of
process pressure or bursting of parts.
Before performing any maintenance
operations:
D
Always wear protective gloves,
clothing, and eyewear when
performing any maintenance
operations to avoid personal injury.
D
Be sure the actuator cannot
suddenly open or close the valve.
D
Use bypass valves or completely
shut off the process to isolate the
valve from process pressure. Relieve
process pressure from both sides of
the valve. Drain the process media
from both sides of the valve.
D
Vent the pneumatic actuator
loading pressure and relieve any
actuator spring precompression.
D
Use lockout procedures to be
sure that the above measures stay in
effect while you work on the
equipment.
D
The valve packing box may
contain process fluids that are
pressurized,
even when the valve has
been removed from the pipeline.
Process fluids may spray out under
pressure when removing the packing
hardware or packing rings, or when
loosening the packing box pipe plug.
D
Check with your process or safety
engineer for any additional measures
that must be taken to protect against
process media.
Individual part key numbers and part descriptions
referenced in the following procedures are shown in
figure 6 except where otherwise indicated.
Lubrication
The interior parts of a Type 1077 actuator should be
lubricated on a regular schedule with a quality gear
lubricant. The interior parts should also be lubricated
whenever difficulty in handwheel rotation indicates a
need for lubrication.
To lubricate the Type 1077 actuator, perform the
following steps:
1. Note the location of the travel indicator pointer in
relation to the indicator dial. When reassembling the
actuator, the travel indicator pointer must be
returned to its original position. Remove the machine
screws and the travel indicator pointer.
2. For a size 0-KE actuator only, remove the O-ring
grease seal from the hub of the drive sleeve gear.
3. Remove the cap screws which secure the
gearbox cover plate and remove the gearbox cover
plate.
4. Coat the worm, the drive sleeve gear teeth, and
the bearing surfaces of the gearbox housing and
worm with a quality gear lubricant.
5. Install the cover on the gearbox (key 1) and
secure it with the cap screws.
6. For a size O-KE only, install the the O-ring
grease seal onto the hub of the drive sleeve gear.
7. Attach the travel indicator pointer so that it
indicates the same point of rotation as was noted
before the pointer was removed. Secure the pointer
with the machine screws.
Disassembly
Parts are subject to normal wear and must be
inspected periodically. The following procedure
describes actuator disassembly for general
inspection and replacement of the drive sleeve gear.
Note
In order to remove the drive sleeve
gear, it is necessary to first remove the
actuator input shaft and worm.
1. Remove the pin (key 6) and the handwheel
(key 5).
2. For a size 10-KE:6 actuator only, remove the cap
screws which secure the reduction drive (item not
shown) and slide the reduction drive off the input
shaft.
3. Perform steps 1, 2, and 3 of the lubrication
procedure above.
4. Remove the pin which secures the worm to the
input shaft by following the appropriate procedure for
the actuator size: