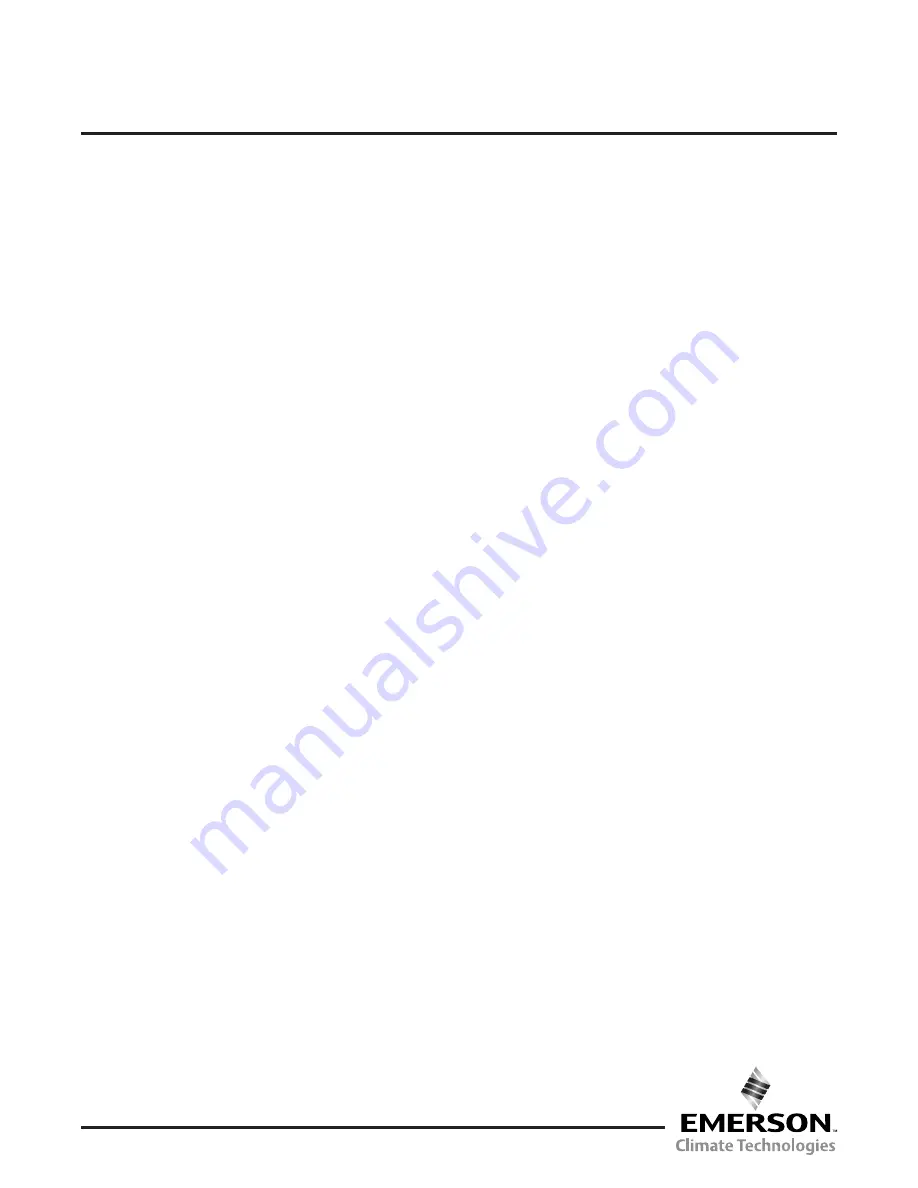
FD113 Oil Pressure Safety Control
FD113 Oil Pressure Safety Control
Instruction Sheet
PA-00250
June 2013
THE FLEXIBLE CONTROL
• The FD113 Oil Pressure Safety Control senses the effective oil
pressure differential in compressors with positive displacement oil
pumps. If inadequate oil pressure exists, a time delay is energized.
If the oil pressure does not recover to safe levels within the time
delay setting, the compressor is shut down. The time delay allows
the compressor adequate time to establish oil pressure on start–up
and avoids nuisance shutdowns on pressure drop of short duration
during the run cycle.
• Maximum application flexibility is assured by providing an
adjustable differential pressure switch which can be adjusted to
the compressor’s minimum required oil pressure needs and an
adjustable time delay which allows you to select the length of
time the compressor runs below the minimum pressure before
shutdown. The minimum pressure setting and time delay values
specified by the compressor manufacturer should be used when
installing the FD113 control.
FEATURES
• Pressure Range adjustable from 4 to 65 PSID.
Timer start pressure – timer stop pressure is 3 PSID above
timer start pressure.
• A SPDT switch is used in the pressure portion of the control
which allows the addition of a “safe light” if desired.
• Timer is Time – Adjustable from 20 to 150 seconds.
Supply voltage – 24 to 240 Volt AC/DC. Timing unaffected by
voltage or ambient temperature variations.
• A SPDT Manual Reset Switch is used in the Timer Module.
Upon time-out, the compressor is stopped and an alarm circuit
is energized. To restart the compressor and de-energize the
alarm circuit, the reset button is pushed.
• A factory installed Jumper allows the FD113 to be powered from
a single power source. Should separate circuits be desired for
the timer and “Lockout” switch, the Jumper can be removed.
SAFETY INSTRUCTIONS
1. Read all Instructions thoroughly. Failure to comply can result
in control failure, system damage or personal injury.
2. Do not use with ammonia or on hazardous or corrosive fluids.
3. Do not install in Hazardous Locations.
4. Disconnect electrical power before installation. Do not reapply
power until control installation is complete, wiring connections
secured and cover is in place.
5. Before making pressure control connections, depressurize
system and make certain lines are at atmospheric pressure.
Pilot Duty Ratings:
120/240 VAC
U.L. B300
360 VA Maximum
CONTROL RATINGS
INSTALLATION INSTRUCTIONS–GENERAL
1.
Cover Removal
—Loosen cover screw, pull cover forward.
2.
Mounting
—Mount the control in a protected area on the
mounting bracket or a flat surface with screws provided.
CAUTION: If other screws are used, use 8-32 screws that
do
not
penetrate into the control more than 1/8’’.
Oil Pressure Safety Controls should always be mounted
above the oil level in the compressor crankcase. The
capillary tubes or pressure connections should be routed
to allow them to be free–draining to the compressor
crankcase. This will prevent oil logging in the capillary
tubes during low ambient conditions.
3.
Capillary Tube Connections
: Proper installation of
capillary tubes and/or pressure control lines will insure
a trouble–free installation.
WARNING:
Before making any
pressure control connections, depressurize system. Failure
to do so can cause system damage or personal injury.
• If the control is mounted on the compressor, all lines
must be secured to the compressor so they do not
vibrate independently from the compressor.
• If the control is mounted remote from the compressor
an open coiled vibration loop, 2 to 3 coils, 2 to 3’’
diameter should be provided between the compressor
base and the moving compressor. The lines coming
from the coil should be secured to the base and
compressor so the coil takes all the vibration. Avoid
any “violin string” runs of control capillary tubes.
• Sharp bends or kinks
must
be avoided in the capillary
or pressure lines. Do not allow the lines to rub and
abrade against any moving surface. Avoid any excess-
ive handling or reforming of the copper lines to
minimize work hardening of the copper.
4.
Electrical Connections
—
WARNING:
Before making any
electrical connections, disconnect all electrical power.
Check with a voltmeter as more than one source of power
may be supplied. Make certain the load to connected is
within the electrical rating of the control (see Table 1).
• All wiring should conform to National Electrical Code
and/or local codes. Use
14AWG or larger copper
conductors ONLY
.
• The terminals are of a clamp design. Loosen the
terminal screws with a small screwdriver, insert
approximately 3/8’’ stripped wire and securely tighten.
SPECIFICATIONS – FD113ZU/ZUK
Ambient Temperature Range
–5°F to +140°F
Pressure Range
– PSID – Adjustable
Timer Energize
: 4 to 65 PSID net effective oil pressure on
pressure drop.
Timer De-energize
:3 PSI above timer energize setting on
pressure rise.
Timer
Voltage:
24 to 240 volts AC or DC
Timing:
20 to 150 seconds – Adjustable
Maximum Over Pressure:
During installation and service, the
control’s power element should not be exposed to pressures
exceeding 330 PSIG.
NEMA CLASS I – Mount the control body in an area
protected from the weather, water or excessive moisture,
dirt, dust and corrosive or explosive atmospheres.
SPECIFICATIONS – ENCLOSURE
EmersonClimate.com/FlowControls