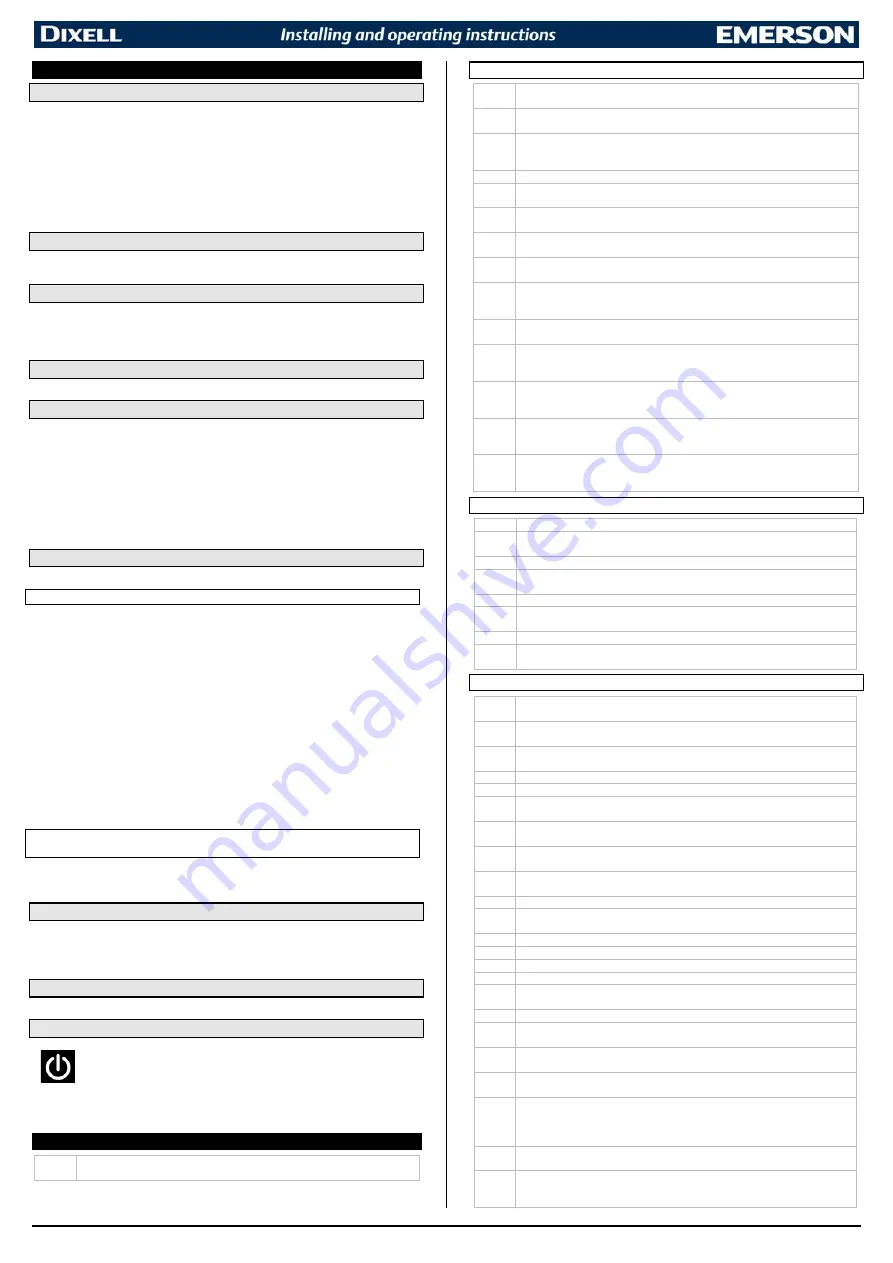
1592020680 XRi60CH EN r2.0 2021.07.14
XRi60CH
3/9
11.
MAIN FUNCTIONS
11.1
TO SET THE CURRENT TIME AND DAY (ONLY WITH RTC)
When the instrument is switched on, it could be required to set the real-time clock.
1.
Enter the Pr1 programming menu by keeping both
SET+DOWN
buttons pressed for 3 sec.
2.
Browse to the
rtC
menu and then push the
SET
key to enter the real time clock menu.
3.
The
Hur
(hour) parameter is displayed.
4.
Push the
SET
and set current hour by the
UP
and
DOWN
keys, then push
SET
to confirm the
value.
5.
Repeat the same operations with
Min
(minutes) and
dAy
(day) parameters and other
parameters.
To exit:
Push both
SET+UP
buttons or wait for 15 sec without pushing any button.
11.2
HOW TO SEE THE SET POINT
1.
Push and immediately release the
SET
key: the display will show the Set point value
2.
Push and immediately release the
SET
key or wait for 5 sec to display the probe value again
11.3
HOW TO CHANGE THE SET POINT
1.
Push the
SET
button for 3 sec to change the Set point value.
2.
The value of the set point will be displayed and the
°C
or
°F
icon will start blinking
3.
Use the
UP
or
DOWN
buttons to modify the current value
4.
Use the
SET
button to store the new value into memory
11.4
HOW TO START A MANUAL DEFROST
Keep the
DEF
button pressed for 3 sec to start a manual defrost.
11.5
HOW TO ENTER PARAMETER
PROGRAMMING MENU “PR1”
Follow these steps:
1.
Enter the Programming mode by pressing the
SET+DOWN
buttons for 3 sec (the
°C
or
°F
LED
will start blinking)
2.
Browse to the required parameter and then press the
SET
button to display its current value
3.
Use
UP
or
DOWN
buttons to change its value
4.
Press
SET
button to store the new value and move to the following parameter
To exit
: press
SET+UP
buttons or wait for 15 sec without pressing any key.
NOTE
: the set value is stored even when the procedure exits by waiting for the time-out
11.6
HOW TO ENTER PARAMETER
PROGRAMMING MENU “PR2”
The manufacturer menu (Pr2) includes all the parameters of the instrument.
11.6.1
ENTERING THE PARAMETER PROGRAMMING MENU “PR2”
1.
Enter the Programming mode by pressing the
SET+DOWN
buttons for 3 sec (the
°C
or
°F
icon
will start blinking).
2.
Released the buttons and then push again the
SET+DOWN
buttons for more than 7 sec. The
Pr2 label will be displayed immediately followed from the
HY
parameter.
NOW THE PARAMETER MENU “PR2” IS AVAILABLE FOR ANY MODIFICATION
3.
Browse to the required parameter.
4.
Press the
SET
button to display its value.
5.
Use
UP
or
DOWN
to change its value.
6.
Press
SET
to store the new value and move to the following parameter.
To exit:
press
SET+DOWN
or wait for 15 sec without pressing any key.
NOTE1:
if no parameter is present in Pr1 menu, after 3 sec
the “
noP
” message
will be displayed. Keep
the buttons pushed till the Pr2 message will be displayed.
NOTE2:
the set value is stored even when the procedure ends by waiting for the time-out
11.6.2
HOW TO MOVE A PARAMETER FROM “PR2” MENU TO “PR1” MENU AND VICE
-
VERSA
Each parameter present in the hidden menu (Pr2) can be moved into the user level (Pr1) by pressing
both
SET+DOWN
buttons. If a parameter is part of the user level, when showed in the hidden menu
the decimal point will be lit.
11.7
HOW TO LOCK THE KEYBOARD
1.
Keep both
UP
and
DOWN
buttons pressed more than 3 sec.
2.
The “
PoF
” message will be displayed, and the keyboard will be locked. At this point it will be
possible only to see the set point or the MAX o Min temperature stored
3.
If a button is pressed more than 3 sec
the “
PoF
” message will be displayed.
11.8
HOW TO: UNLOCK THE KEYBOARD
Keep both
UP
and
DOWN
pressed more than 3 sec till the
“Pon”
message will be displayed.
11.9
THE ON/OFF FUNCTION
By pushing the
ON/OFF
key, the instrument will go in stand-by.
During the stand-by status, all the relays are switched OFF and the regulations are
stopped; if a monitoring system is connected, it does not record the instrument data
and alarms.
WARNING: loads connected to the normally closed contacts of the relays are always supplied
and under voltage, even if the instrument is in stand-by mode.
12.
PARAMETERS
rtC
Real time clock menu (only for controller with RTC):
to set the time and date and
defrost start time.
REGULATION
LS
Minimum Set Point:
(-100.0°C to SET; -148°F to SET) fix the minimum value for the
set point.
US
Maximum Set Point:
(SET to 150.0°C; SET to 392°F) fix the maximum value for the
set point.
HY
Compressor regulation differential in normal mode:
(0.1 to 25.0°C; 1 to 45°F) set
point differential. Compressor Cut-IN is
T > SET + HY
. Compressor Cut-OUT is
T<=SET
.
HY1
Variable Speed Compressor Differential in normal mode:
0.1 to 25.5°C; 1 to 45°F
odS
Output activation delay at start-up:
(0 to 255 min) this function is enabled after the
instrument power-on and delays the output activations.
AC
Anti-short cycle delay:
(0 to 999 sec) minimum interval between a compressor stop
and the following restart.
AC1
Anti-short cycle delay (2nd compressor):
(0 to 999 sec) delay before activating
second compressor.
MCo
Maximum time with compressor ON:
(0 to 255min) maximum time with ONOFF
compressor active. With
MCo=0
this function is disabled.
rtr
Regulation percentage=F(P1; P2):
(0 to 100; 100=P1, 0=P2) it allows to set the
regulation according to the percentage of the first and second probe, as for the
following formula (rtr(P1-P2)/100 + P2).
CCt
Maximum duration for Pull Down:
(0.0 to 23h50min, res. 10min) after elapsing this
time interval, the super cooling function is immediately stopped.
CCS
Pull Down phase differential (SET+CCS or SET+HES+CCS):
(-12.0 to 12.0°C; -21
to 21°F) during any super cooling phase the regulation SETPOINT is moved to
SET+CCS
(in normal mode) or to
SET+HES+CCS
(in energy saving mode)
oHt
Threshold for automatic activation of Pull Down in normal mode (SET+HY+oHt):
(0.1 to 25.5°C; 1 to 45°F) this is the upper limit used to activate the super cooling
function.
Con
Compressor ON time with faulty probe:
(0 to 255 min) time during which the
compressor is active in case of faulty thermostat probe. With
Con=0
compressor is
always OFF.
CoF
Compressor OFF time with faulty probe:
(0 to 255 min) time during which the
compressor is OFF in case of faulty thermostat probe. With
CoF=0
compressor is
always active.
PROBE MENU
PbC
Probe selection:
(ntC; PtC; Pt1)
ntC
=NTC type;
PtC
=PTC type;
Pt1
=PT1000 type
ot
Probe P1 calibration:
(-12.0 to 12.0°C; -21 to 21°F) allows to adjust any possible
offset of the first probe.
P2P
Probe P2 presence:
n
= not present;
Y
= present.
oE
Probe P2 calibration:
-12.0 to 12.0°C; -21 to 21°F) allows to adjust any possible
offset of the second probe.
P3P
Probe P3 presence:
n
= not present;
Y
= the defrost is present.
o3
Probe P3 calibration:
(-12.0 to 12.0°C; -21 to 21°F) allows to adjust any possible
offset of the third probe.
P4P
Probe P4 presence:
n
= not present;
Y
= present.
o4
Probe P4 calibration:
(-12.0 to 12.0°C; -21 to 21°F) allows to adjust any possible
offset of the fourth probe.
VARIABLE SPEED COMPRESSOR
FMi
Minimum value for Variable Speed Compressor (RPM * 10):
(0 to FMA) select
according to the VSC in use
FMA
Maximum value for Variable Speed Compressor (RPM * 10):
(FMi to 500) select
according to the VSC in use
Fr0
Value when Variable Speed Compressor is shut down (RPM * 10):
(0 to 200)
select according to the VSC in use
tSt
PI regulator, temperature sampling time:
(00:00 to 42min:30sec)
iSt
PI regulator, integral sampling time:
(00:00 to 42min:30sec)
vdC
Type of Variable Speed Drive:
(nu; FrE)
nu
= no VSC in use;
FrE
= VSC with
frequency control mode is used
voS
Signal output variation for Variable Speed Compressor:
(1 to 255 RPM*30) VSC
variation when
SET-
HY ≤ T ≤ SET+HY
vo2
Signal output variation for Variable Speed Compressor:
(1 to 255 RPM*30) VSC
variation when
SET-HY-
HY1≤T<SET
-
HY and SET+HY<T≤SET+HY+HY1
vo3
Signal output variation for Variable Speed Compressor:
(1 to 255 RPM*30) VSC
variation when
SET-HY-HY1<T and T>SET+HY+HY1
PdP
Variable Speed Compressor (in %) during any Pull Down:
(0 to 100%)
SPi
Compressor speed (in %) in case of any probe error during Con interval:
(0 to
100%)
Aod
Compressor speed (in %) during any defrost cycle (valid if tdf=in):
(0 to 100%)
AoF
Compressor speed (in%) during a pre-defrost phase (valid if tdf=in):
(0 to 100%)
tHv
PI regulator, max interval for output variation:
(tLv to 255 sec)
tLv
PI regulator, min interval for output variation:
(1 sec to tHv)
rSr
PI regulator, range for output value calculation (RPM * 10):
(0=disabled; 1 to 255
RPM*10)
Str
PI regulator, delay before range drift:
(0 to 255 sec)
dPt
PI regulator, divisor for PI response time reduction (acts on both par. tSt and
iSt):
(1 to 10)
CMn
Continuous control ON in normal mode:
(n;Y)
Y
= VSC is never stopped during
regulation
CME
Continuous control ON in energy saving mode:
(n;Y)
Y
= VSC is never stopped
during regulation
MnP
Compressor speed threshold to activate lubrication (valid for variable speed
compressors only, 0=disabled):
(nu; 1 to 100%; OFF) nu = not used; 1 to 100% =
select the percentage to activate function; OFF = compressor is stopped when the
condition is reached
tMi
Time range with compressor speed below MnP to activate lubrication cycle:
(00:00 to 24h00min) time before activating the lubrication function
tMA
Time range with compressor speed at 100% to activate lubrication cycle:
(0 to
255 min) VSC will be forced to 100%, for
tMA
, after activating the lubrication
function. NOTE: if
MnP=OFF
, VSC will be stopped for
tMA