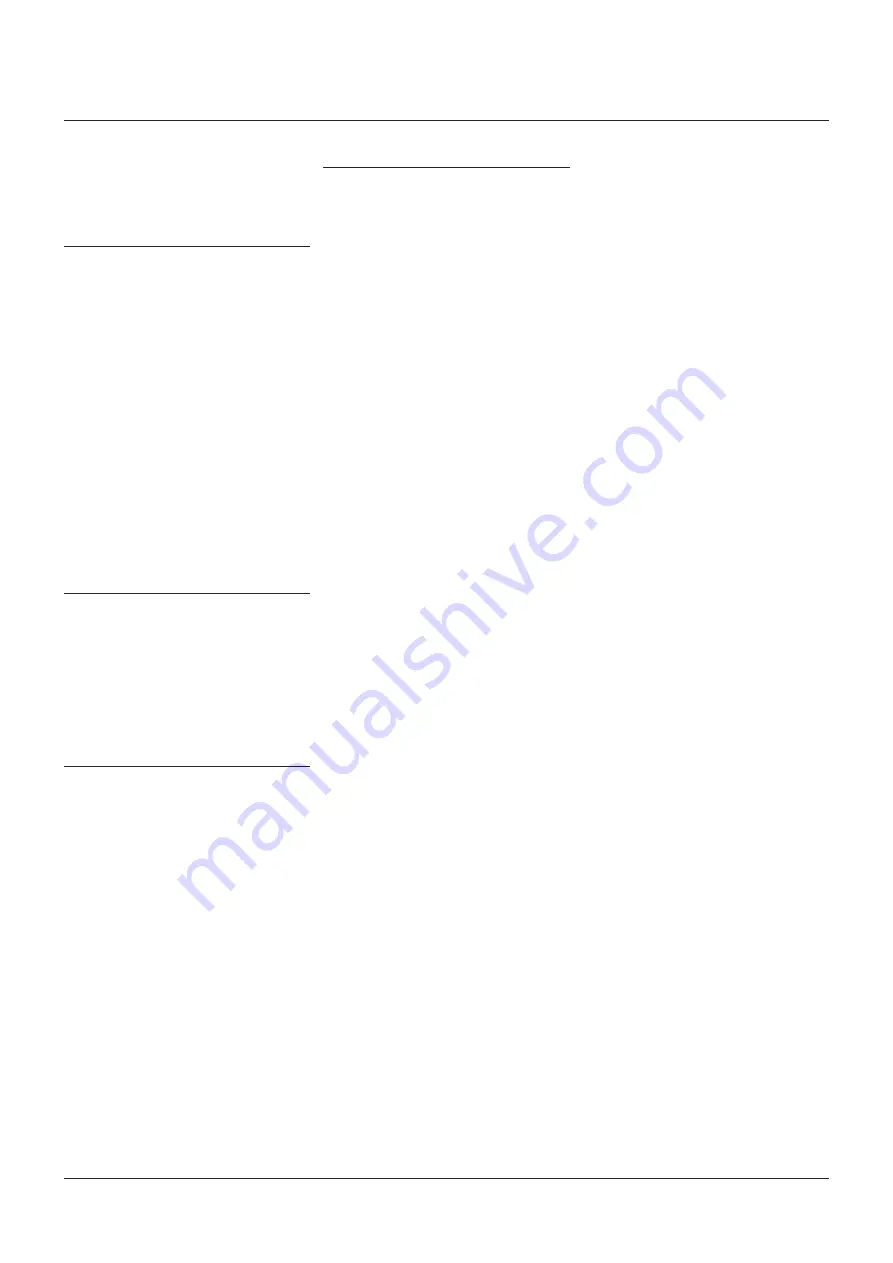
5
Crosby
SerieS HSJ Safety valveS
InstallatIon, operatIon and maIntenance InstructIons
4 hydrostatiC testing
When a hydrostatic test is made on the system,
it is recommended that blank flanges be used
in preference to gagging of the safety valves.
excessive tightening of the gag (test rod) may
damage or bend the valve spindle. However,
when the valves are to be gagged for a
hydrostatic test, a gag as shown in figure 4 on
page 10 should be used.
Blank flanges must be removed and the safety
valve reinstalled before the vessel is placed in
service.
When test rods are used, care must be
exercised to prevent overtightening that could
damage the spindle and valve seats. Generally,
a test rod which is finger tight will provide
sufficient force to hold the valve closed.
after the hydrostatic test, the test rod (gag)
must be removed and replaced by either a cap
plug or a cap not fitted with a test rod.
5 testing safety valves
Before a new boiler is put in service all safety
valves should be tested. each valve has been set
and tested at the factory but service conditions
differ and it is sometimes necessary to make
adjustments. Safety valves may be tested by
raising the system pressure and popping the
valve. all safety valves on the system with lower
set pressures should be gagged.
6 desCription of operation
the valve will open with a sharp pop at the
pressure for which it is set and remain open,
relieving full capacity at 3% overpressure. as
pressure decays below the popping pressure,
the valve will remain open until the blowdown
pressure is reached. the valve will close sharply.
7 adjustment
set pressure adjustment
Before making any adjustments, reduce the
system pressure under the valve 10% to 20%
below the set pressure stamped on the valve.
this will prevent damage to internal parts and
minimize the chance of an inadvertent valve
opening.
for parts identification see figure 1 on page 2:
a. remove the cap (19) and lifting lever device
(if any) following the instructions on page 8.
b. loosen the adjusting bolt nut (18).
c. turn the adjusting bolt (17) clockwise to
increase set pressure or counterclockwise
to reduce set pressure.
d. retighten the adjusting bolt nut (18)
following each adjustment.
e. Once the set pressure has been established
replace the cap (19) and lifting lever device
(if any) following the instructions on page 9
and install a new seal and wire.
nozzle ring and guide ring adjustment
the nozzle ring (3) and guide ring (9)
adjustment is made at the factory and resetting
in service seldom is necessary.
Should it be necessary to change blowdown
or reduce valve simmer, the following steps
should be taken:
Whenever ring adjustments are changed, a
record should be kept of the number of notches
and the direction in which the ring was moved.
this will make it possible to return to the
original setting in case of error.
Caution
Gags should not be used when inlet pressures are
more than 10% greater than the safety valve set
pressure. Damage to the valve may result.
Caution
Should any ring adjustments be made while the
valve is installed on a pressurized vessel, the
valve should be gagged. Care must be exercised
to prevent excessive tightening of the gag that
could damage the valve spindle and valve seats.
However, sufficient force must be applied to the
gag to prevent the valve from lifting.
important
Crosby steel safety valves have the shipment ring
settings stamped on the machined surface on the
bonnet directly under the cap. See Figure 2.