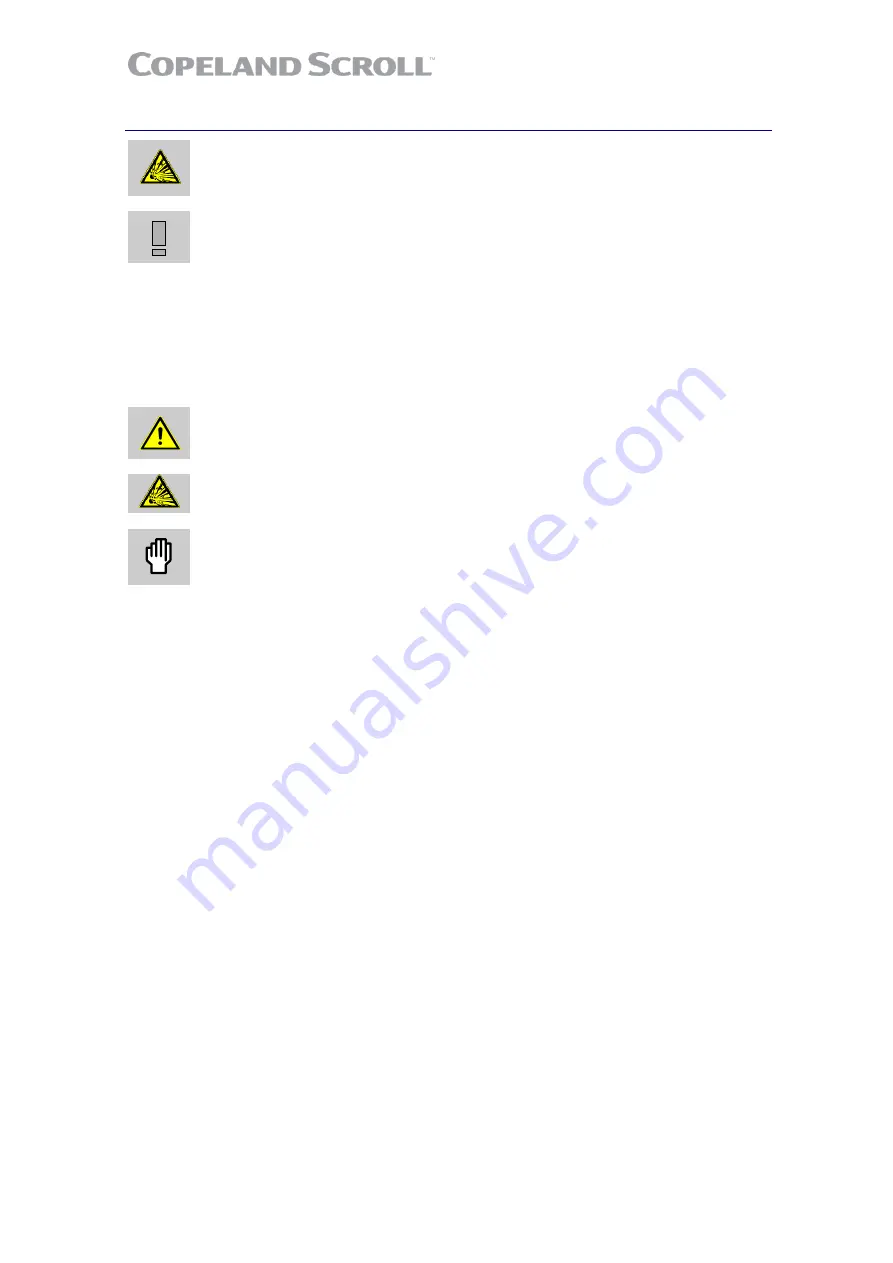
18
C6.2.27/0716-0219/E
6
Starting up & operation
WARNING
Diesel effect!
System explosion!
The mixture of air and oil at high
temperature can lead to an explosion. Avoid operating with air.
IMPORTANT
Oil dilution! Bearing malfunction!
Turn the crankcase heater on 12 hours
before starting the compressor.
6.1
Strength pressure test
The compressor has been strength-tested in the factory. It is not necessary for the customer to
strength- or leak-test the compressor again although the compressor will normally be exposed to
the testing made as part of system testing.
6.2
Tightness/pressure test
WARNING
High pressure! Personal injuries!
Consider personal safety requirements
and refer to test pressures prior to test.
WARNING
System explosion! Personal injuries!
DO NOT USE other industrial gases.
CAUTION
System contamination! Bearing malfunction!
Use only dry nitrogen or dried
air for pressure testing.
If using dry air do not include the compressor in the pressure test
– isolate it first. Never add
refrigerant to the test gas (as leak indicator).
6.3
System evacuation
Before the installation is put into commission, it has to be evacuated with a vacuum pump. Proper
evacuation reduces residual moisture to 50 ppm. During the initial procedure, suction and
discharge shut-off valves on the compressor remain closed. The installation of adequately sized
access valves at the furthest point from the compressor in the suction and liquid lines is advisable.
Pressure must be measured using a vacuum pressure gauge on the access valves and not on the
vacuum pump; this serves to avoid incorrect measurements resulting from the pressure gradient
along the connecting lines to the pump.
Evacuating the system only on the suction side of a Scroll compressor can occasionally result in
a temporary no-start condition for the compressor. The reason for this is that the floating seal could
axially seal with the scroll set, with the higher pressure on the floating seal. Consequently, until
the pressures equalise, the floating seal and scroll set can be held tightly together. The installation
should be evacuated down to 0.3 mbar.
Subsequently, the factory holding charge of dry air in the compressor is released to the ambient.
The shut-off valves are opened and the installation - including the compressor - is once more
evacuated as described after the system has been recharged with dry nitrogen. The highest
demands are placed on the leak-proof design of the installation and on leak testing methods
(please refer to EN 378).
6.4
Preliminary checks
– Pre-starting
Discuss details of the installation with the installer. If possible, obtain drawings, wiring diagrams,
etc. It is ideal to use a check-list but always check the following:
▪
Visual check of the electrics, wiring, fuses etc
▪
Visual check of the plant for leaks, loose fittings such as TXV bulbs etc
▪
Compressor oil level
▪
Calibration of HP & LP switches and any pressure actuated valves
▪
Check setting and operation of all safety features and protection devices
▪
All valves in the correct running position