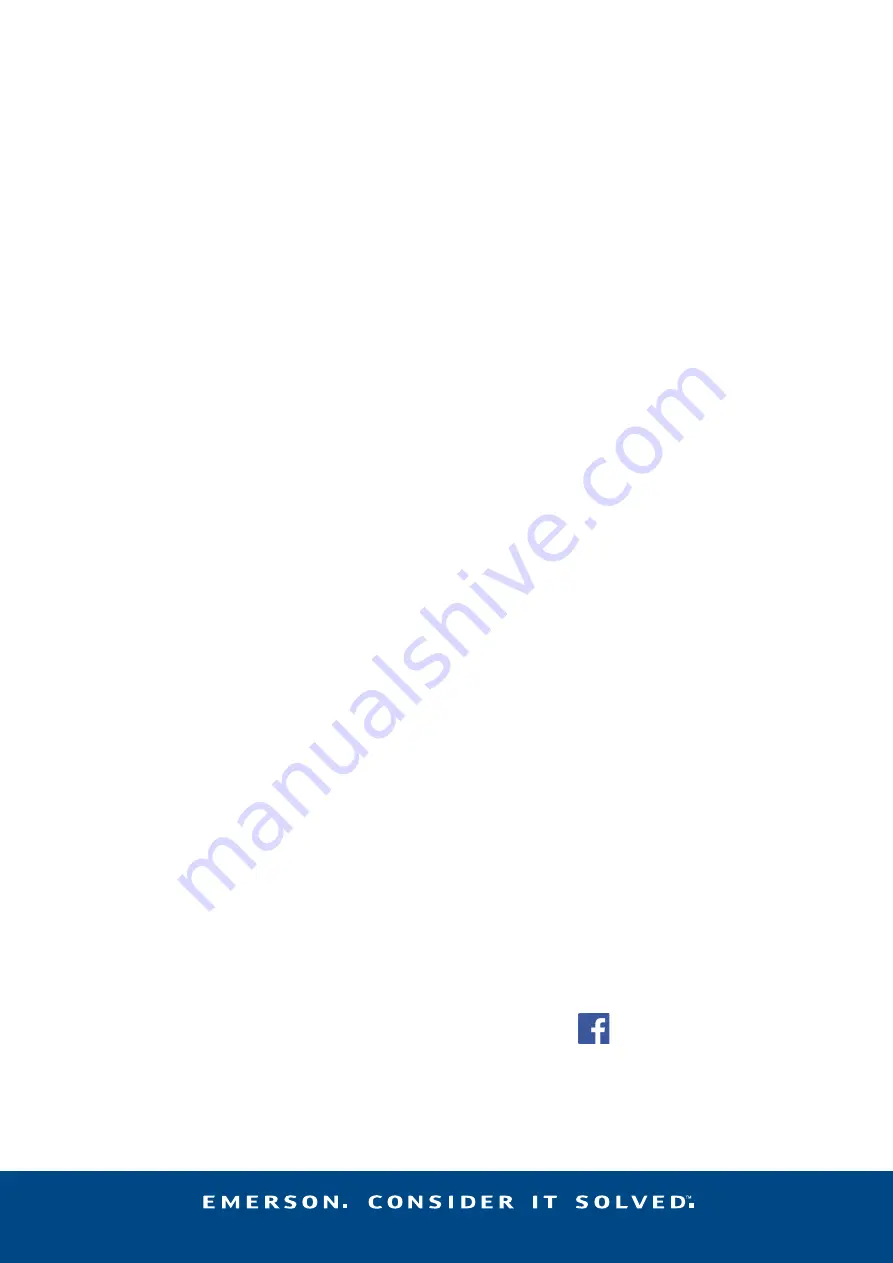
C6.1.11/0718-0619/E
BENELUX
Josephinastraat 19
NL-6462 EL Kerkrade
Tel: +31 45 535 06 73
Fax: +31 45 535 06 71
UK & IRELAND
Unit 17, Theale Lakes Business Park
Reading, Berkshire RG7 4GB
Tel: +44 1189 83 80 00
Fax: +44 1189 83 80 01
BALKAN
Selska cesta 93
HR-10 000 Zagreb
Tel: +385 1 560 38 75
Fax: +385 1 560 38 79
GERMANY, AUSTRIA & SWITZERLAND
Theo-Mack Str. 3
DE-63477 Maintal
Tel: +49 6109 605 90
Fax: +49 6109 60 59 40
SWEDEN, DENMARK, NORWAY & FINLAND
Pascalstr. 65
DE-52076 Aachen
Tel: +49 2408 929 0
Fax: +49 2408 929 525
FRANCE, GREECE & MAGHREB
8, Allée du Moulin Berger
FR-69134 Ecully Cédex, Technoparc - CS 90220
Tel: +33 4 78 66 85 70
Fax: +33 4 78 66 85 71
EASTERN EUROPE & TURKEY
Pascalstr. 65
DE-52076 Aachen
Tel: +49 2408 929 0
Fax: +49 2408 929 525
ROMANIA & BULGARIA
Parcul Industrial Tetarom 2
Emerson Nr. 4 400641 Cluj-Napoca
Tel: +40 374 13 23 50
Fax: +40 374 13 28 11
ITALY
Via Ramazzotti, 26
IT-21047 Saronno (VA)
Tel: +39 02 96 17 81
Fax: +39 02 96 17 88 88
POLAND
Szturmowa 2
PL-02678 Warsaw
Tel.
+48 22 458 92 05
Fax
+48 22 458 92 55
MIDDLE EAST & AFRICA
PO Box 26382
Jebel Ali Free Zone - South, Dubai - UAE
Tel: +971 4 811 81 00
Fax: +971 4 886 54 65
ASIA PACIFIC
Suite 2503-8, 25/F., Exchange Tower
33 Wang Chiu Road, Kowloon Bay
Kowloon , Hong Kong
Tel: +852 2866 3108
Fax: +852 2520 6227
CZECH REPUBLIC
Hajkova 22
CZ - 133 00 Prague
Tel: +420 733 161 651
Fax: +420 271 035 655
SPAIN & PORTUGAL
C/ Pujades, 51-55 Box 53
ES-08005 Barcelona
Tel: +34 93 412 37 52
RUSSIA & CIS
Dubininskaya 53, bld. 5
RU-115054, Moscow
Tel: +7 - 495 - 995 95 59
Fax: +7 - 495 - 424 88 50
For more details, see www.climate.emerson.com/en-gb
The Emerson logo is a trademark and service mark of Emerson Electric Co. Emerson Climate Technologies Inc. is a subsidiary of Emerson Electric Co.
Copeland is a registered trademark and Copeland Scroll is a trademark of Emerson Climate Technologies Inc.. All other trademarks are property of their respective owners.
Emerson Climate Technologies GmbH shall not be liable for errors in the stated capacities, dimensions, etc., as well as typographic errors. Products, specifications, designs and
technical data contained in this document are subject to modification by us without prior notice. Illustrations are not binding.
© 2019 Emerson Climate Technologies, Inc.
Emerson Commercial & Residential Solutions
Emerson Climate Technologies GmbH - Pascalstrasse 65 - 52076 Aachen, Germany
Tel. +49 (0) 2408 929 0 - Fax: +49 (0) 2408 929 570 - Internet: www.climate.emerson.com/en-gb
Connect with us: facebook.com/EmersonCommercialResidentialSolutions
Summary of Contents for Copeland EazyCool OME-4MTL-09X
Page 1: ...Copeland Eazycool CO2 Refrigeration Units Application Guidelines ...
Page 5: ......
Page 68: ...C6 1 11 0718 0619 E 63 ...