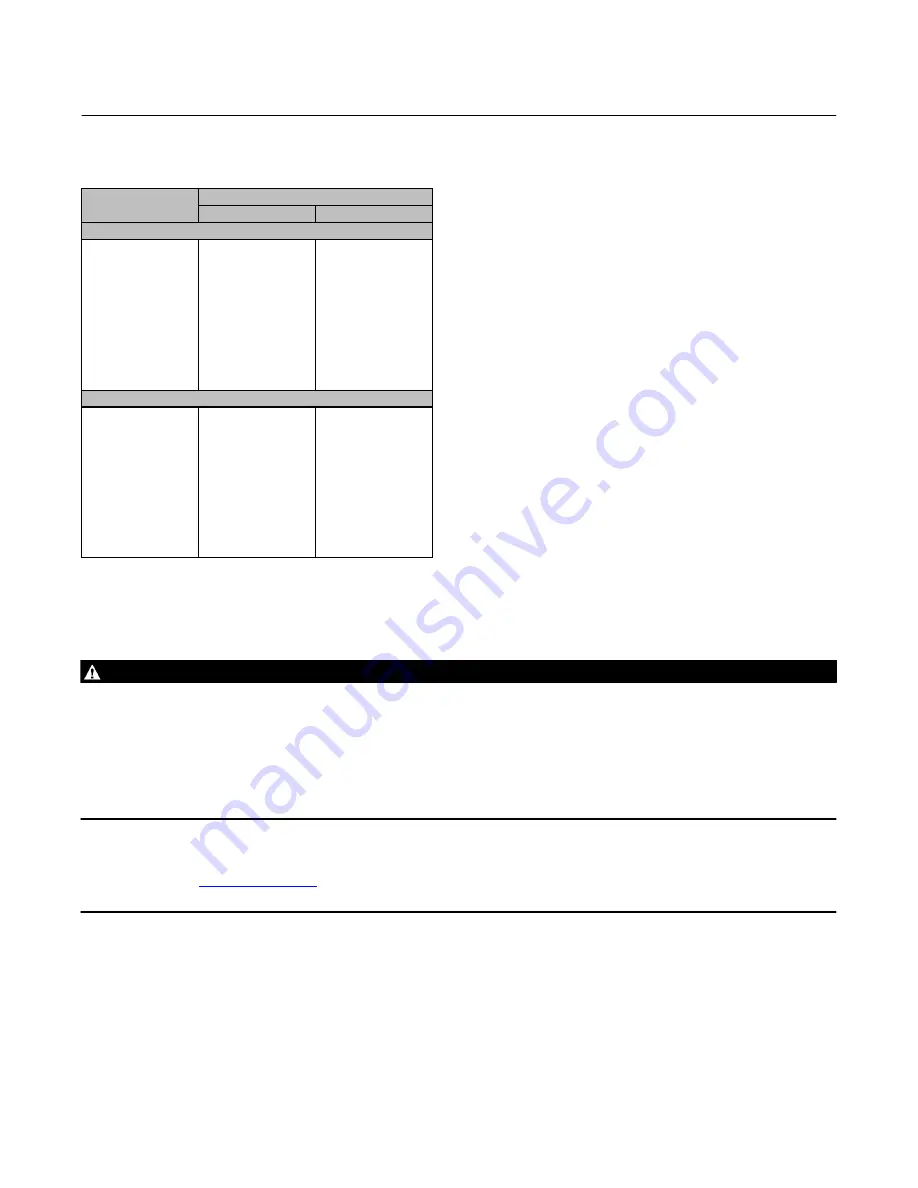
Instruction Manual
D104223X012
A11 Valve
August 2017
4
Table 2. Approximate Weight for Size 3 through
24‐Inch Valves
VALVE
SIZE
CLASS
900
1500
kg
3
4
6
8
10
12
14
16
18
20
24
---
---
59
120
210
450
444
513
703
991
1626
---
---
---
---
311
663
810
1152
1613
2250
---
lbs
3
4
6
8
10
12
14
16
18
20
24
---
---
130
264
463
993
976
1132
1550
2185
3590
---
---
---
---
685
1462
1785
2540
3555
4960
---
Installation
WARNING
Always wear protective gloves, clothing, and eyewear when performing any installation operations to avoid personal
injury.
Check with your process or safety engineer for any additional measures that must be taken to protect against process
media.
If installing into an existing application, also refer to the WARNING at the beginning of the Maintenance section in this
instruction manual.
Note
When installing a valve after it has been in long‐term storage, cycle the valve at least ten times to re‐energize the dynamic seal.
Please contact your
Emerson sales office
or Local Business Partner if you have any questions about preparing a valve for storage or
if you are planning to put into service a valve that has been stored for some time.