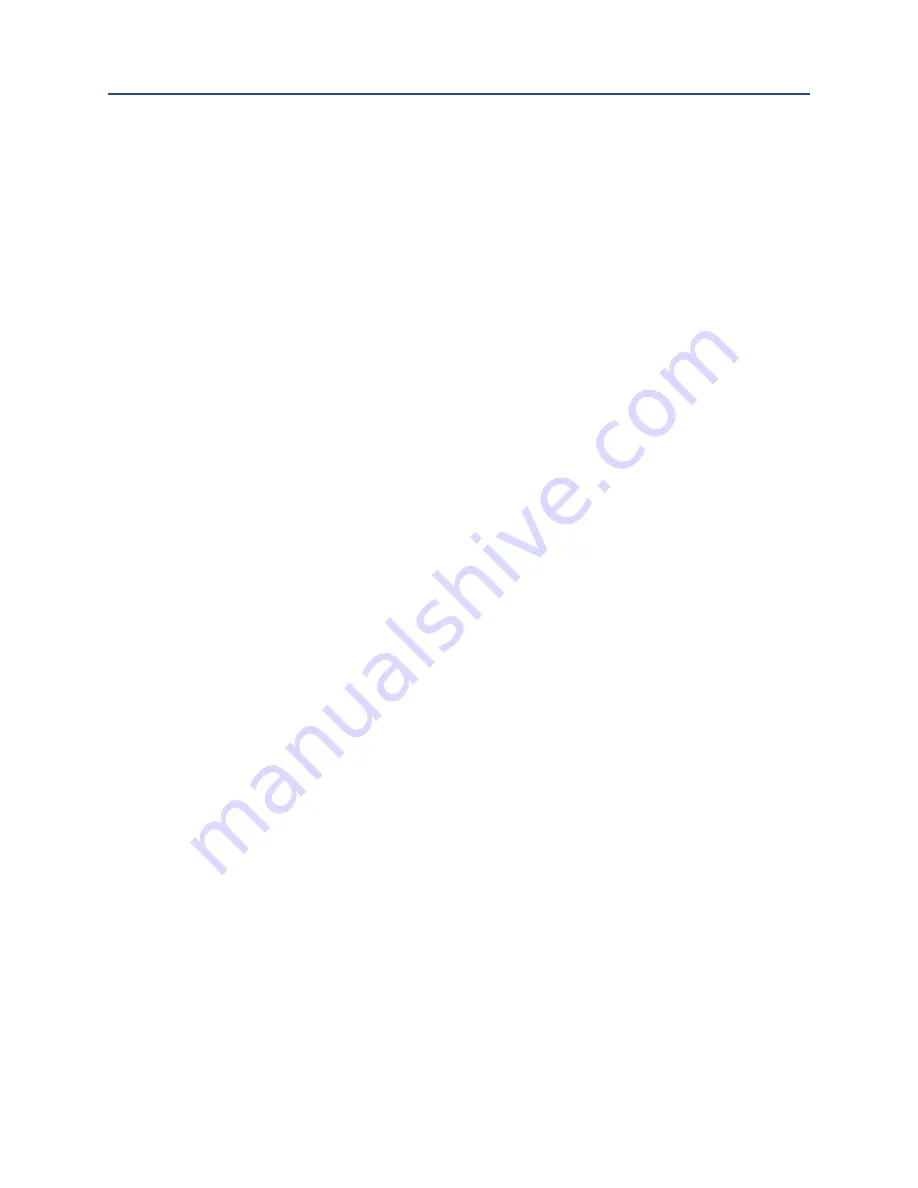
October 2015
Service Instructions
VA001-196-30 Rev. 1
5
Section 1: Introduction
Introduction
1�11�2
Check Connections:
1.
Pneumatic/hydraulic components connected as per schematic enclosed
or in service manual supplied.
2.
Pneumatic supply connected to identified ports.
3.
Electrical connections terminals are secure.
4.
Wiring as per enclosed diagram or service manual supplied.
1�11�3
When actuator is first put into service it should be cycled with regulated
pneumatic pressure. This is necessary because the seals have been stationary,
causing them to take a "set". Therefore, the actuator should be operated through
several cycles, exercising the seals, resulting in a service ready condition.
1�11�4
The actuator speed of operation is determined by a number of factors including:
1.
Power supply line length
2.
Power supply line size
3.
Power supply line pressure
4.
Control valve and fitting orifice size
5.
Torque requirements of the valve
6.
Size of the actuator
7.
Setting of speed controls
1�11�5
Due to the interaction of these variables it is difficult to specify a "normal"
operating time. Faster operating times may be obtained by using one or more of
the following:
1.
Larger supply lines
2.
Larger control valve
3.
Higher supply pressure*
4.
Quick exhaust valves
*Not to exceed maximum operating pressure of actuator or control components
1�11�6
Slower operating times may be obtained by using flow control valves to meter the
exhaust. Excessive exhaust flow metering may cause erratic operation. Normally,
incoming supply should not be metered.
1�12
Actuator Operation
1�12�1
Controlled Operation: Controlled operation is accomplished by pressurizing and/or
depressurizing the appropriate cylinder inlet(s) of a double-acting.
Do not exceed pressures indicated on actuator nameplate�
1�12�2
Manual Operation: All pressure must be vented or equalized on both sides of the
pneumatic piston prior to manual operation.