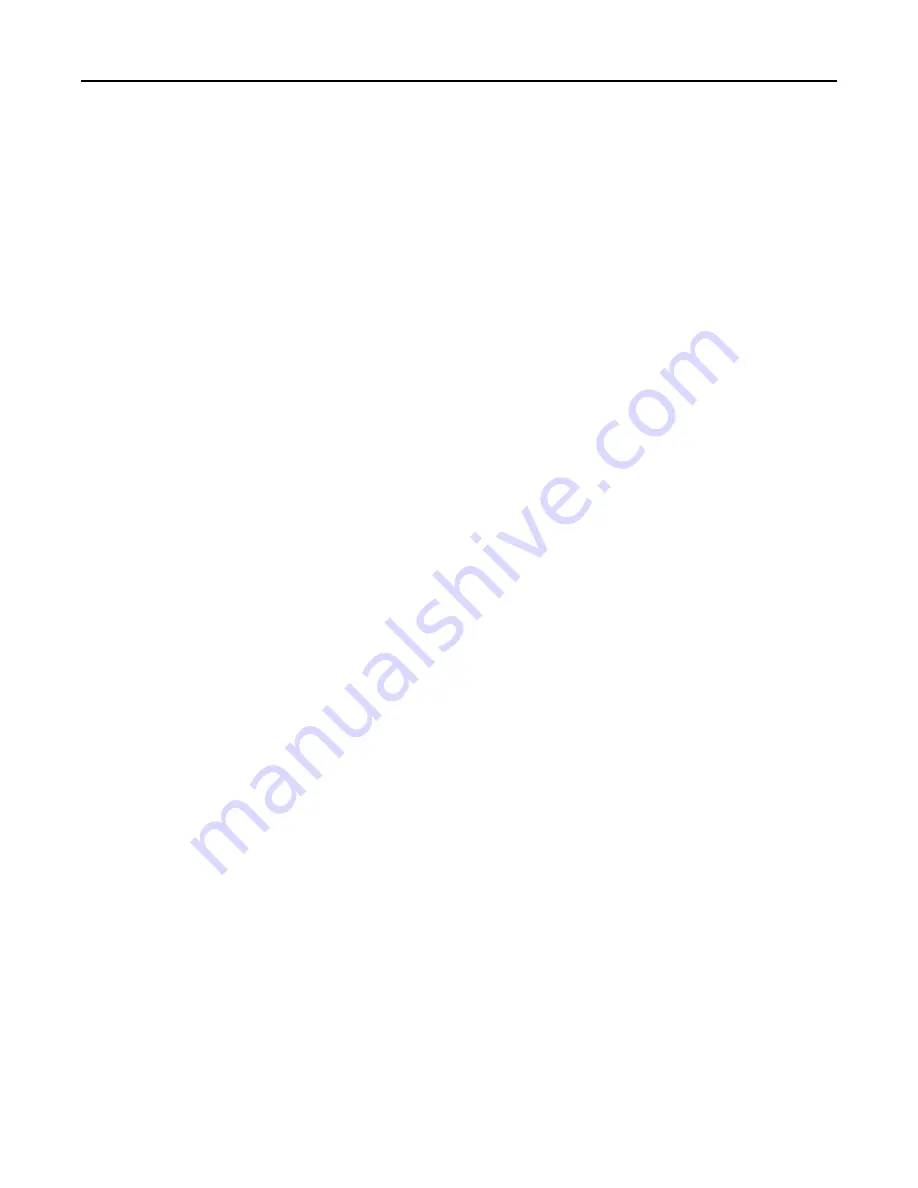
1. Disconnect the pilot supply tubing (key 21) from
the main body (key 17).
2. Remove the two hex head cap screws (key 18)
which hold the lower casing (key 1) to the body.
Separate the lower casing from the body. Inspect
the body O-ring (key 15) and replace if worn
or damaged.
3. Examine the valve disk (key 13) and orifice (key 12)
for nicks, cuts and other damage. Unscrew the disk
holder assembly from the valve stem assembly
(key 16) and replace it with a new part if necessary.
For the Type 299HS, also examine the insert and
O-ring (keys 82 and 83, Figure 6) for any damage.
Replace if needed.
4. If the orifice is being replaced with a new or
differently sized orifice, change the nameplate
(key 63) to state the new size and maximum inlet
pressure. Lubricate the threads and flat face of the
orifice with a good grade of anti-seize lubricant.
Install the orifice using 100 to 120 ft-lbs / 136 to
163 N•m of torque.
5. After replacing all damaged parts, slide the
entire assembly into the valve body (key 17) and
secure with the two hex head cap screws (key 18).
6. Connect the pilot supply tubing (key 21), then refer
to the Startup section for putting the regulator
into operation.
integral Pilot Valve Disk and Orifice
Follow this procedure to inspect, clean or replace the
integral pilot valve disk or orifice. Part key numbers are
referenced in Figures 3 and 4.
1. Remove or loosen the pilot supply tubing (key 21).
2. Remove the inlet fitting (key 47) and the four
machine screws (key 46).
3. Examine the valve disk (key 52) for nicks, cuts and
other damage. Unscrew the disk holder assembly
from the valve stem (key 48) and replace
if necessary.
4. If the seating edge of the orifice (key 50) is nicked
or rough, use a thin-walled socket to remove the
orifice from the inlet fitting (key 47). Install a new
orifice and a lightly lubricated O-ring (key 49) when
reassembling the regulator.
5. Inspect the check valve assembly (key 45) and
the bleed restriction (key 70) for damage and
replace if necessary.
6. The Type 299H has a wire inlet screen (key 51)
in the pilot supply inlet fitting (key 47). If clogging
is suspected in the pilot supply, remove the elbow
fitting (key 19) and clean the wire screen.
7.
Lightly lubricate the O-ring (key 54) on the inlet
fitting (key 47) and reinstall using the four machine
screws (key 46). Torque the machine screws to
30 to 40 in-lbs / 3.4 to 4.5 N•m. Then install and
tighten the pilot supply tubing.
integral Pilot Control Spring
and Diaphragm
Follow this procedure to change the pilot control spring
or to inspect, clean or replace the diaphragm. Part
key numbers are referenced in Figures 3, 4 and 5.
1. Remove the pilot closing cap (key 29) and
loosen the hex lock nut (key 35). Turn the
adjusting screw (key 36) counterclockwise to
ease spring compression.
2.
Unscrew the bonnet (key 34).
3. Remove the bonnet (key 34), spring seat
(key 33) and control spring (key 32).
4. If only replacing the control spring (key 32),
sparingly apply lubricant to the control spring seat
(key 33) and reassemble in the reverse order.
note
When replacing the control spring with
a different spring range, be sure to
delete the spring range appearing on the
nameplate and indicate the new range.
5. Remove the machine screws (key 30) and spring
case (key 31) from the lower casing (key 1).
6. Remove the diaphragm assembly (key 28) by tilting
them so that the pusher post (key 40) slips off the
lever (key 57). To separate the diaphragm from the
attached parts, unscrew the hex nut (key 37) and
separate the parts: washer (key 38), diaphragm
post (key 39), pusher post (key 40), overtravel
spring (key 41), machine screw (key 42), spring
seat (key 88) (Types 299HR and 299HSR), rivet
(key 43) and retaining ring (key 44).
7. To replace the lever assembly (key 57), remove the
lever pin (key 25). To replace the valve stem
(key 48), also perform Integral Pilot Valve Disk and
Orifice maintenance procedure steps 1, 2 and 3
and pull the stem (key 48) out of the lower casing
assembly (key 1). Lightly lubricate the replacement
stem O-ring (key 53) and install it on the valve stem.
11
299H Series