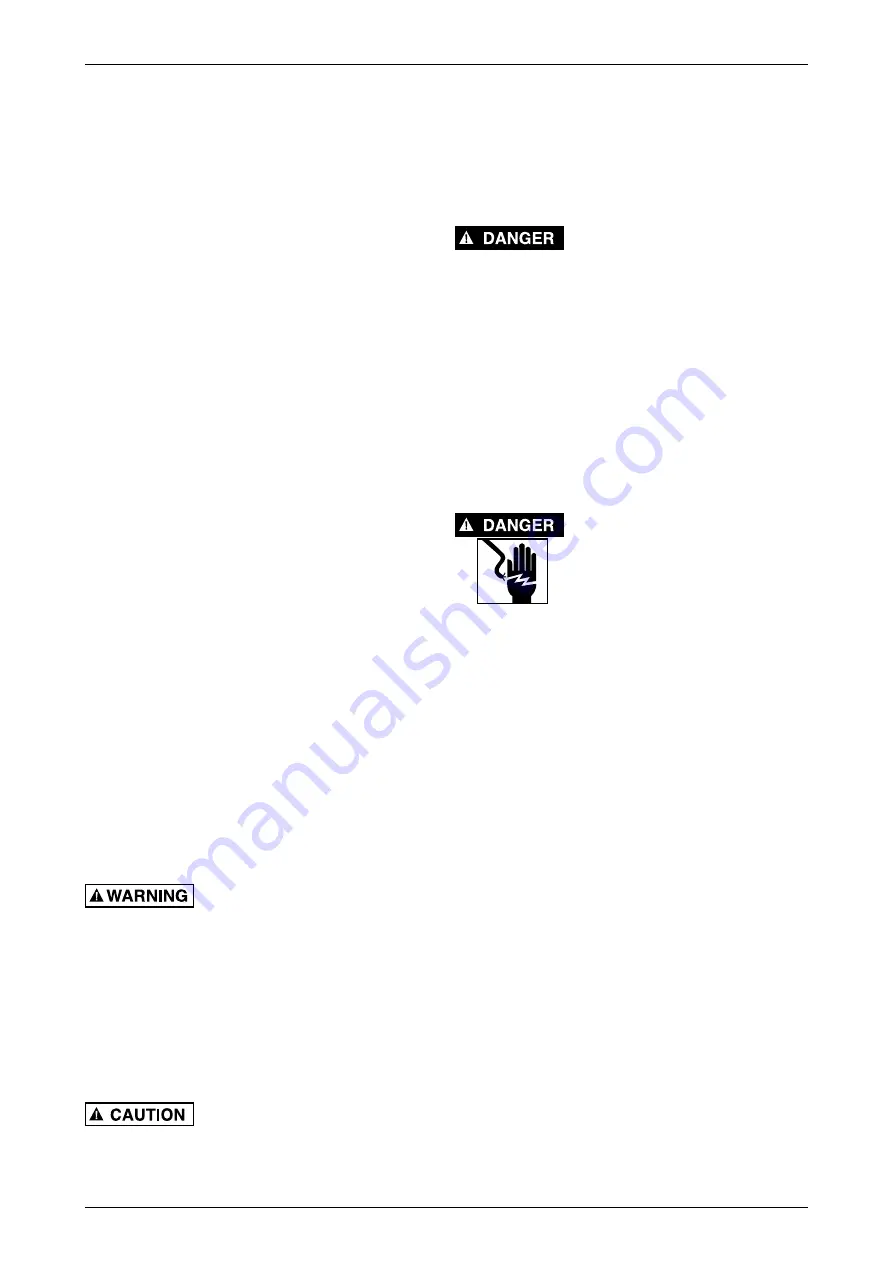
5
HP15P005SS man v.170804
Silent Air Series
welding, drilling or other modifications. Such
modifications may weaken the air tank and
cause a hazardous condition.
5. If the air tank develops a leak, replace it
immediately. Never repair, weld or make
modifications to the air tank or its attachments.
6. Do not make adjustments to the factory-set
pressures.
7. Never exceed attachments' manufacturer's
maximum-allowable pressure rating.
8. Do not use plastic pipe or lead tin solder
joints for a discharge line as the may not
withstand the high heat developed during air
compression.
Personal Protective Equipment
Be sure all operators and others around the
compressor and its controls comply with all
applicable OSHA, Federal, State and local
regulations, codes and standards relating to
personal protective equipment. This includes
respiratory protective equipment, protection for
the extremities, protective clothing, protective
shields and barriers, electrical protective
equipment, and personal hearing protective
equipment.
1. Eye protection should be worn at all times
when operating this tool. Use ANSI approved
safety glasses. Everyday eyeglasses are NOT
safety glasses. Dust mask, non-skid safety
shoes, hard hat, or hearing protection should
be used in appropriate conditions.
2. Wear proper apparel.
Loose clothing, gloves, neckties, rings,
bracelets, or other jewelry may present a
potential hazard when operating this tool.
Please keep all apparel clear of the tool.
Inspection
Inspect compressor prior to any use. Check for
external damage that might have occurred during
transit. Be careful of moving parts. Report any
damage to delivery carrier immediately.
Do not operate unit if damaged
during shipping, handling or use.
Damage may result in bursting and cause injury
or property damage.
Installation
Area
1. Install compressor in a clean, dry and well-lit
area. Be sure installation area can maintain a
temperature range between 35° - 110° F (2° -
43° C).
If ambient temperature drops
below 32˚F (0° C), be sure to
protect safety/relief valves and drain valves from
freezing. NEVER operate compressor with
temperatures below 15˚F (-9.5° C) or above 125˚F
(52° C).
2.
Allow sufficient space around compressor for
maintenance access and adequate airflow.
Mount unit leaving a minimum of 15 inches (38
cm) of clearance.
3. Use shims to level compressor if installation
area is not flat. This will avoid excessive
vibration and premature pump wear.
DO NOT install compressor in
boiler room, paint spray room, or
area where sandblasting occurs. Make sure inlet
air is away from exhaust fumes or other toxic,
noxious or corrosive fumes or substances.
4. If acid is used in operating environment or air
is dust laden, pipe intake to outside, fresh air.
Increase pipe size by one size for every 20
feet of run. Be sure to install protective hood
around intake filter.
5. Insulate cold water or other low temperature
pipes that pass overhead to avoid
condensation dripping on compressor which
could cause rust and/or motor shorting.
Electrical Safety
Be sure only trained and
authorized personnel maintain
this compressor in accordance
with all applicable federal, state
and local codes, standards and
regulations. Follow all NEC
(National Electric Code) standards especially
those concerning equipment grounding
conductors.
1. Follow all NEC and local codes for electrical
wiring. Allow only authorized Polar Air service
person or certified electrician to install
electrical components.
2. Put unit on dedicated circuit and make sure
no other electrical equipment is wired into it.
Failure to wire unit on independent circuit can
cause circuit overload and/or imbalance in
motor phasing. Install proper No Fuse Breaker
(NFB) according to kW output of compressor.
3. Ensure incoming service has adequate
ampere rating.
4. Ensure supply line has the same electrical
characteristics (voltage, cycles and phase) as
the electric motor.
5. Refer to amp load information on the
specifications label and use correctly sized
wiring. Be sure to consider distance between
power supply and machine.
6. Install surge protection device between power
supply and compressor motor.
7. Make sure to install properly sized breakers
and fuses.
8. The unit must be properly grounded. DO NOT
connect ground wire to air or cooling lines.