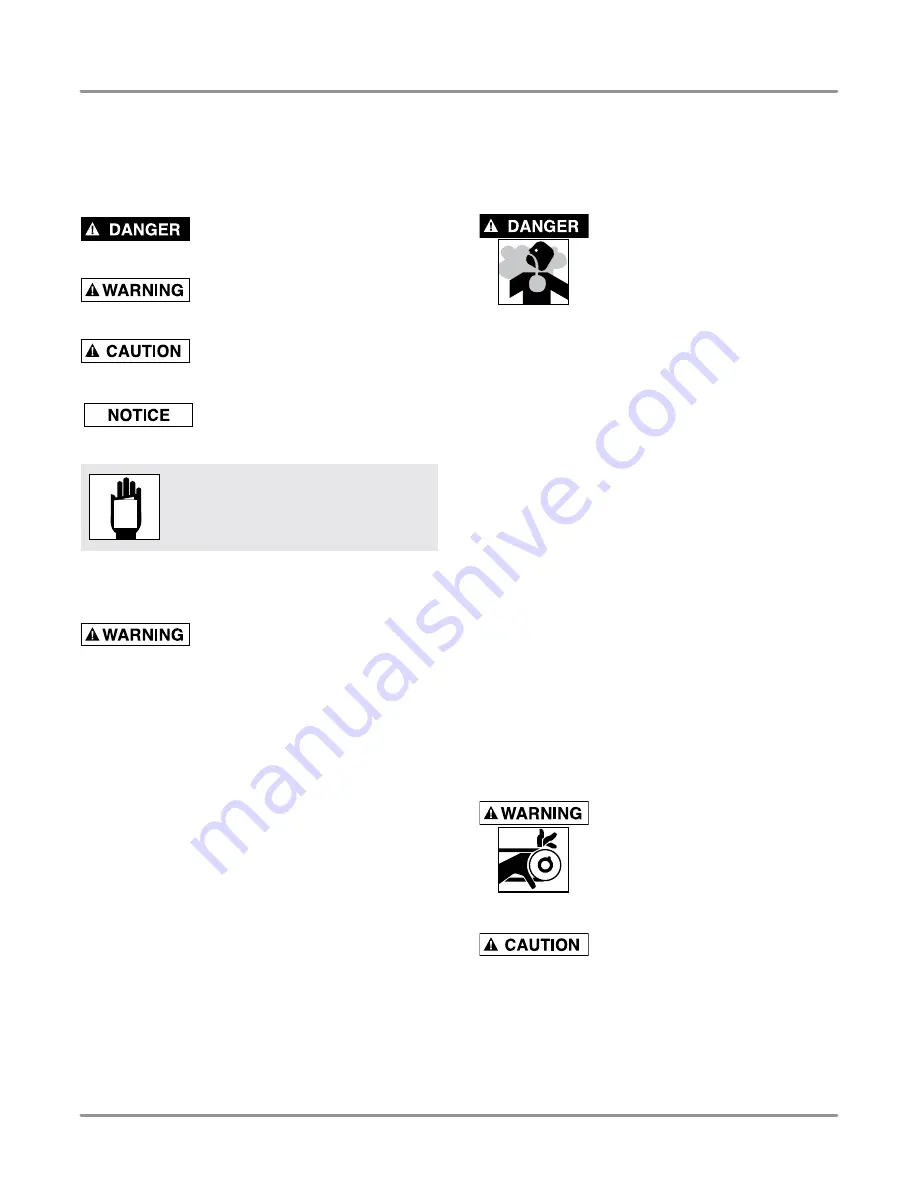
4
EMAX
Electric Operated, Piston Compressors
Safety
This manual contains very important information to
know and understand. This is provided for SAFETY
and to PREVENT EQUIPMENT PROBLEMS. To help un-
derstand this information, observe the following:
Danger indicates an imminently
hazardous situation which, if not
avoided,
will
result in death or serious injury.
Warning indicates a potentially
hazardous situation which, if not
avoided,
could
result in death or serious injury.
Caution indicates a potentially
hazardous situation which, if not
avoided,
may
result in minor or moderate injury.
Notice indicates important infor-
mation, that if not followed, may
cause damage to equipment.
Basic Guidelines
CALIFORNIA PROPOSITION 65
This product or its power cord may
contain chemicals known to the
State of California to cause cancer and birth defects or
other reproductive harm. Wash hands after handling.
1. Allow only trained, authorized persons who
have read and understood these operating
instructions to use this compressor. Failure
to follow the instructions, procedures and
safety precautions in this manual can result
in accidents and injuries.
2. NEVER start or operate the compressor under
unsafe conditions. Tag the compressor,
disconnect and lock out all power to it to
prevent accidental start-up until the condi-
tion is corrected.
3. Install, use and operate the compressor only
in full compliance with all pertinent OSHA
regulations and all applicable Federal, State
& Local Codes, standards and regulations.
4. NEVER modify the compressor and/or controls
in any way.
5. Keep a first aid kit in a convenient place.
Seek medical assistance promptly in case
of injury. Avoid infection by caring for any
small cuts and burns promptly.
MANUAL
Read all manuals included with this
product carefully. Be thoroughly
familiar with the controls and the
proper use of the equipment.
Breathable Air
1. NEVER use air from this compressor for
breathable air except in full compliance with
OSHA Standards 29 CFR 1910 and any other
Federal, State or Local codes or regulations.
Death or serious injury can result
from inhaling compressed air
without using proper safety
equipment. See OSHA standards
on safety equipment.
2. DO NOT use air line anti-icer systems in air
lines supplying respirators or other equip-
ment used to produce breathable air. DO NOT
discharge air from these systems in unventi-
lated or other confined areas.
Pressurized Components
This equipment is supplied with a ASME designed
pressure vessel protected by an ASME rated relief
valve. Pull the ring
before each use
to make sure
the valve is functional. Refer to figure 10. DO
NOT attempt to open valve while the machine is
under pressure.
Personal Protective Equipment
Be sure all operators and others around the
compressor and its controls comply with all appli-
cable OSHA, Federal, State and Local regulations,
codes and standards relating to personal protec-
tive equipment. This includes respiratory protec-
tive equipment, protection for the extremities,
protective clothing, protective shields and barri-
ers, electrical protective equipment, and personal
hearing protective equipment.
Inspection
Inspect compressor prior to any
use. Check for external damage
that might have occurred during
transit.
Be careful of moving parts
then test pulley by turning it
freely by hand.
Report any dam-
age to delivery carrier immediately.
Make sure pallet-mounted
compressors are firmly secured to
the pallet before moving. NEVER attempt to move
a compressor that is not secure as serious injury or
property damage could occur.
A forklift may be necessary for unloading the EMAX
compressor. Use all forklift safety measures and
require a certified forklift operator. Refer to figure 1
for safe unloading procedure.