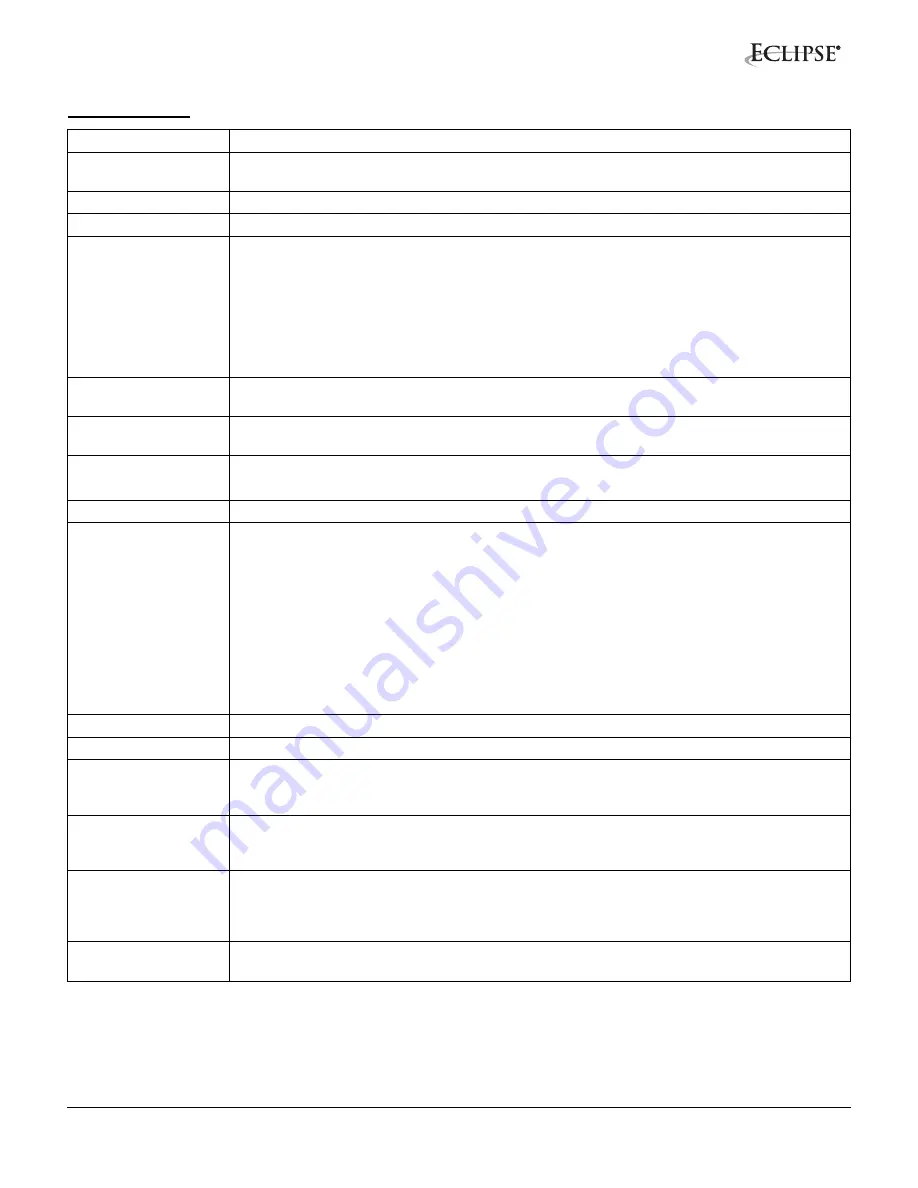
6
AirHeat, V1, Operating Instructions, Edition 09.12
Specifications
*Based on blower motor limitations.
**Based on parallel air flow. If mounted in a cross flow, the flame will be shorter
Input
1,000,000 Btu/h per lineal foot (962 kW/m).
Fuels
Natural gas or 100% propane vapor. Call Eclipse for information on using other fuels. See
Table 1 below.
Gas Turndown
40:1
Pilot Input
Approximately 25,000 Btu/h (7.3 kW)
Gas Inlet Pressure
800,000 Btu/h/ft (769 kW/m)
Natural Gas: 2.2 ”w.c. (5.5 mbar)
Propane: 0.9 ”w.c. (2.2 mbar)
1,000,000 Btu/h/ft (962 kW/m)
Natural Gas: 3.5 ”w.c. (8.7 mbar)
Propane: 1.3 ”w.c. (3.2 mbar)
Gas pressure shown is a differential measured between the gas inlet and a tap on the duct
wall, 10” to 20” (250 to 500 mm) downstream of the burner.
Ambient Temperature
Limits*
-40° to +104°F (-40° to + 40°C)
Downstream
Temperature Limits
1500°F (815°C)
Flame Length**
800,000 Btu/h/ft (769 kW/m): 2.3 ft (0.71 m)
1,000,000 Btu/h/ft (962 kW/m): 3.8 ft (1.17 m)
Piloting
Integral spark-ignited pilot; ignited plug included.
Flame Monitoring
Flame rod supplied. UV scanner adapters are available. For UV scanners, Eclipse
recommends a flame monitoring system that terminates the ignition spark and proves the
pilot flame without spark prior to opening the main gas valves.
CGA requires two flame rods on burners over 3 ft (0.9 m) long. Use a flame monitoring
endplate (Datasheet 140-5) to mount a second flame rod on the end opposite the gas inlet.
All burners where the flame must travel over 10’ must have flame supervision at both ends.
One device must be at the pilot end while the other device must be at the furthest point from
the pilot.
Motor
Standard: 230/460/3/60 TEFC. Other motors can be supplied.
Materials
All portions of the burner exposed to the flame are cast iron or 321 stainless steel.
Emissions
Emissions performance depends not only on the burner, but also on other factors such as
chamber temperature, chamber design, and heat loading. For estimates of emissions
performance in your application, contact Eclipse.
Packaging Options
Available with complete valve trains and control systems. AH burners and systems can be
supplied already mounted on duct sections as specified by the customer. Contact Eclipse for
information on custom packaged systems.
Models
AH Line-shape, blower mounted on rear Datasheet 140-1
TAH “I”-shape, blower mounted on rear Datasheet 140-3
CAH Cross-shape, blower mounted on rear Datasheet 140-4
Related Documents
For more information on AirHeat accessories such as blower and motor specifications, see
Datasheet 140-5
Summary of Contents for Eclipse AirHeat AH
Page 13: ...Notes i ...