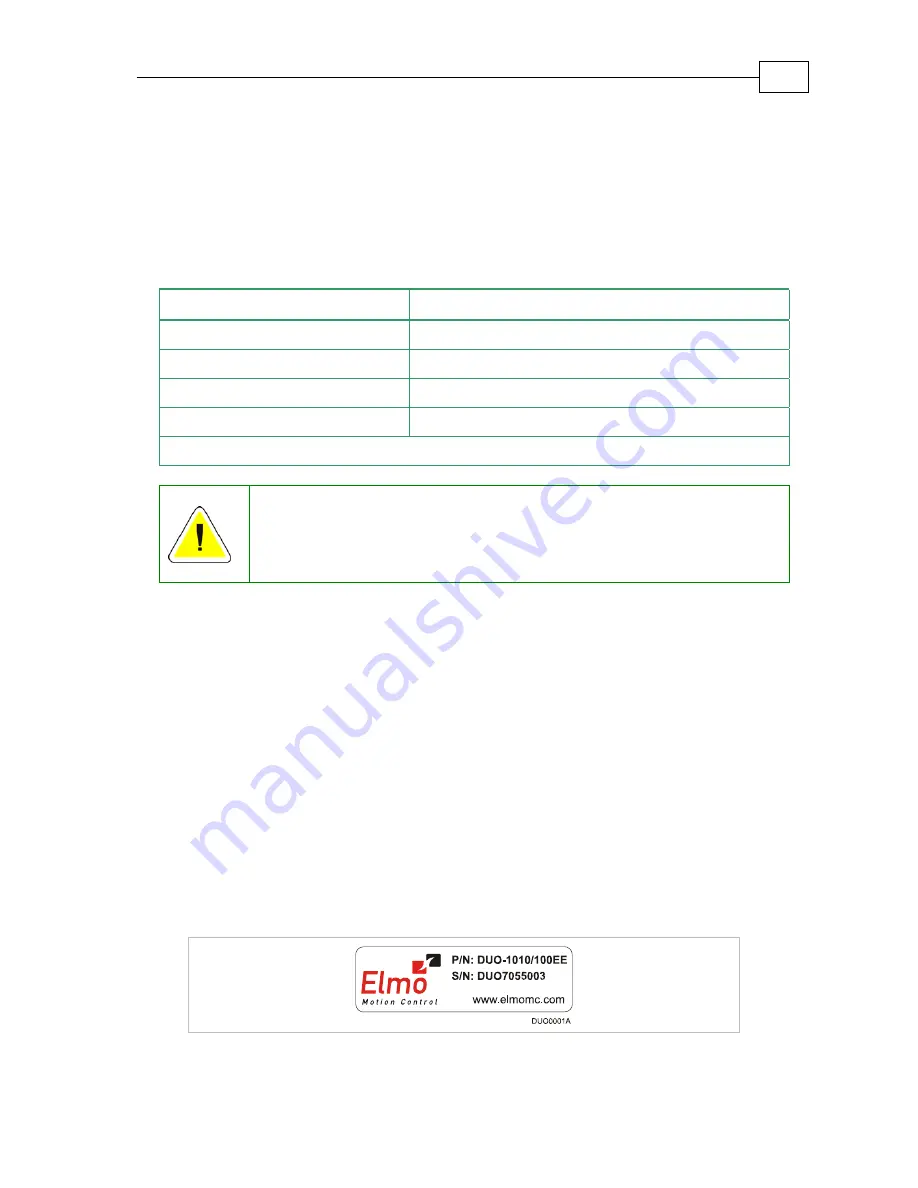
Duo User Guide
3-1
Chapter 3: Installation
3.1
Site Requirements
You can guarantee the safe operation of the Duo by ensuring that it is installed in an
appropriate environment.
Feature Value
Ambient operating temperature
0
°
to 40
°
C (32
°
to 104
°
F)
Maximum operating altitude
10,000m (30,000ft)
Maximum relative humidity
90% non-condensing
Operating area atmosphere
No flammable gases or vapors permitted in area
Models for extended environmental conditions are available.
The Whistle on the Duo dissipates its heat by convection. The maximum
operating ambient temperature of 0
°
to 40
°
C (32
°
to 104
°
F) must not be
exceeded. Refer to the Heat Dissipation section of the
Whistle Installation Guide
for more information.
3.2
Unpacking the Drive Components
Before you begin working with the Duo, verify that you have all of its components, as
follows:
The Duo.
The Composer software and software manual.
The Duo is shipped in a cardboard box with styrofoam protection.
To unpack the
Duo
:
1.
Carefully remove the Duo from the box and the Styrofoam.
2.
Check the Duo to ensure that there is no visible damage to the instrument. If any damage
has occurred, report it immediately to the carrier that delivered your Duo.
3.
To ensure that the Duo you have unpacked is the appropriate type for your requirements,
locate the part number sticker on the side of the Duo. It looks like this:
MAN-DUOUG (Ver. 1.0)
Summary of Contents for 95VDC
Page 1: ...Duo Integrated Solution Installation Guide June 2007 Ver 1 0...
Page 19: ...Duo User Guide MAN DUOUG Ver 1 0 3 7 3 7 Duo Block Diagram Figure 3 2 Duo Block Diagram...
Page 23: ...Figure 3 6 Shared Supply Connection Diagram Duo User Guide MAN DUOUG Ver 1 0 3 11...
Page 49: ...Duo Installation Guide MAN DUOIG Ver 1 0 A 4 A 3 Duo Dimensions...