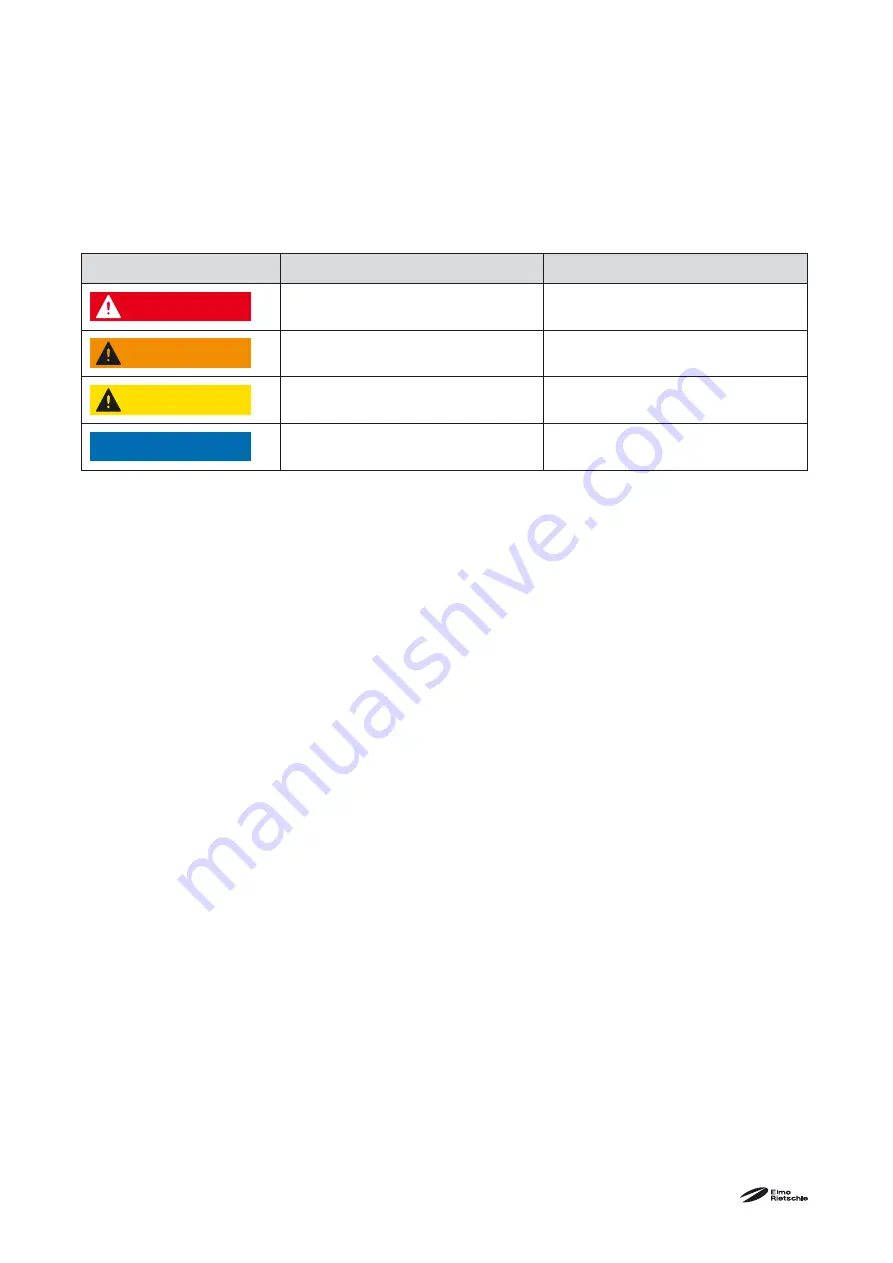
6
|
www.elmorietschle.com
© Gardner Denver Schopfheim GmbH, Gardner Denver Deutschland GmbH
Safety
2 Safety
The manufacturer is not responsible for damage if
you do not follow all of this documentation.
2.1 Warning instruction markings
Warning
Danger level
Consequences if not obeyed
DANGER
immediately imminent danger
Death, severe bodily injury
WARNING
possible imminent danger
Death, severe bodily injury
CAUTION
possible hazardous situation
Slight bodily injury
NOTICE
possible hazardous situation
Material damage
2.2 General
These operating instructions contain basic
instructions for installation, commissioning,
maintenance and inspection work which must be
obeyed to ensure the safe operation of the pump
and prevent physical and material damage.
The safety instructions in all sections must be taken
into consideration. The operating instructions must
be read by the responsible technical personnel/
operator before installing and commissioning and
must be fully understood. The contents of the
operating instructions must always be available on
site for the technical personnel / operator. Instruction
labels affixed to the pump must be obeyed and
must always remain legible. This applies for example
to:
• Symbols for connections
• Data and motor data plate
• Instruction and warning plates
The operator is responsible for observing all local
codes and regulations.
Summary of Contents for S-VSI 300 (44)
Page 35: ......