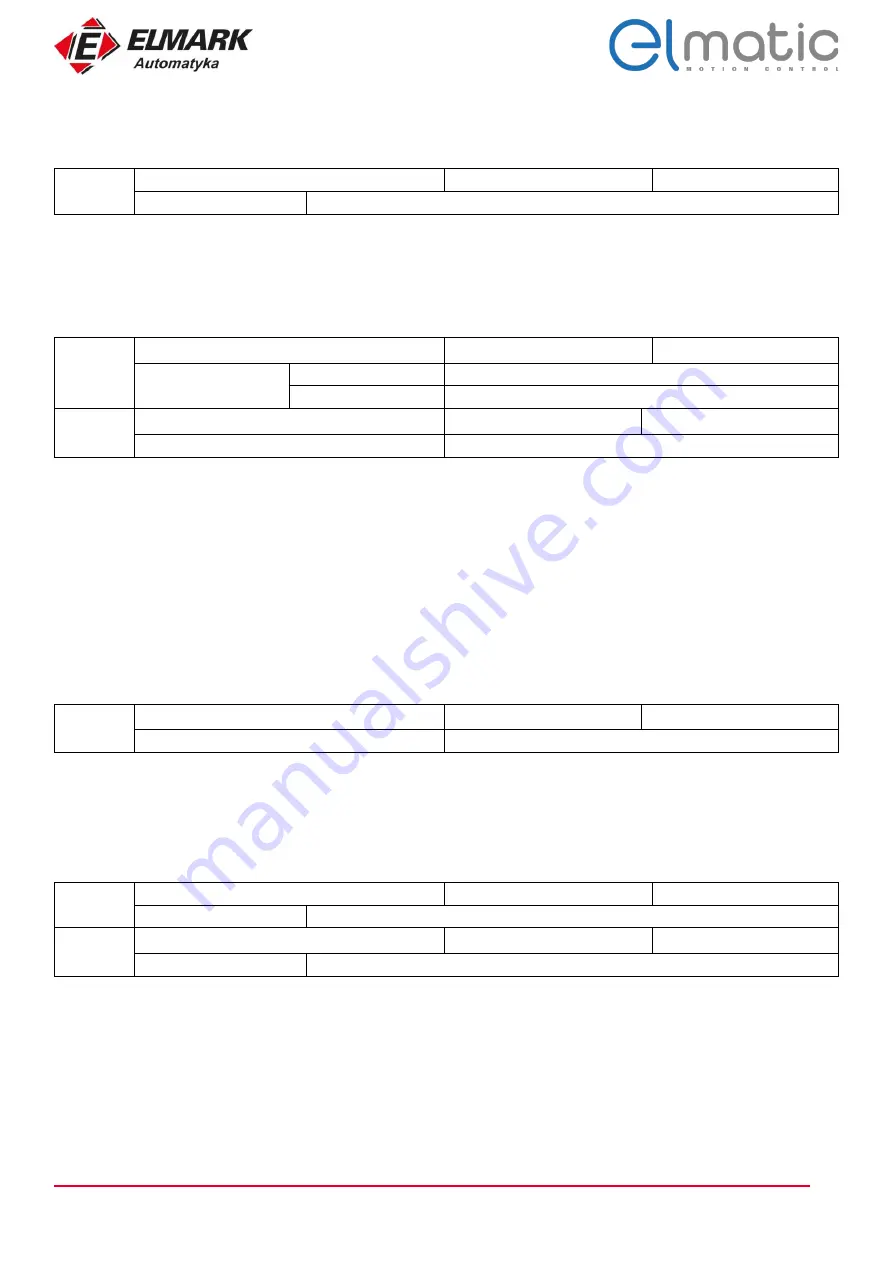
64
Elmark Automatyka S.A.
ul. Niemcewicza 76, 05-075 Warszawa, tel. (+48) 22 773 79 37; [email protected]; www.elmark.com.pl
NIP: 5252072585; KRS: 0000803828, Sąd Rejonowy dla M-St. Warszawy, XIV Wydział Gosp. KRS; Kapitał Zakładowy 525.000 zł, w pełni opłacony
Generally, set the wakeup frequency equal to or higher than the dormant frequency. If the wakeup frequency and dormant
frequency are set to 0, the dormant and wakeup functions are disabled.
When the dormant function is enabled, if the frequency source is PID, whether PID operation is performed in the dormant state
is determined by PA.28. In this case, select PID operation enabled in the stop state(PA.28 = 1).
P8.53
Current running time reached
Default
0.0 Min
Setting Range
0.0 Min ~ 6500.0 Min
If the current running time reaches the value set in this parameter, the corresponding M01 becomes ON, indicating that the
current running time is reached.
Group P9: Fault and Protection
P9.00
Motor overload protection selection
Default
1
Selling Range
0
Disabled
1
Enabled
P9.01
Motor overload protection gain
Default
1.00
Setting Range
0.20 ~ 10.00
P9.00 = 0
The motor overload protective function is disabled. The motor is exposed to potential damage due to overheating. A thermal relay
is suggested to be installed between the AC drive and the motor.
P9.00 = 1
The AC drive judges whether the motor is overloaded according to the inverse time-lag curve of the motor overload protection.
The inverse time-lag curve of the motor overload protection is: 220% *P9.01 *rated motor current (if the load remains at this
value for one minute, the AC drive reports motor overload fault), or 150%
*P9.01 • rated motor current (if the load remains at this value for 60 minutes, the AC drive reports motor overload fault).
Set P9.01 properly based on the actual overload capacity. If the value of P9.01 is set too large, the damage to the motor may result
when the motor overheats but the AC drive does not report the alarm.
P9.02
Motor overload warning coefficient
Default
80%
Setting Range
50% ~ 100%
This function is used to give a warning signal to the control system via M01 before motor overload protection. This parameter is
used to determine the percentage, at which pre-warning is performed before motor overload. The larger the value is, the less
advance
d the prewarning will be.
When the accumulative output current of the AC drive is greater than the value of the overload inverse time-lag curve multiplied
by P9.02, the multifunction digital M01 terminal on the AC drive (Motor overload pre-warning) becomes ON.
P9.03
Overvoltage stall gain
Default
10
Setting Range
0 (no stall overvoltage) ~ 100
P9.04
Overvoltage stall protective voltage
Default
130%
Setting Range
120%-150% (Three phase)
When the DC bus voltage exceeds the value of P9.04 (Overvoltage stall protective voltage) during deceleration of the AC drive,
the AC drive stops deceleration and keeps the present running frequency. After the bus voltage declines, the AC drive continues
to decelerate. P9.03 (Overvoltage stall gain) is used to adjust the overvoltage suppression capacity of the AC drive. The larger the
value is, the greater the overvoltage suppression capacity will be.
In the prerequisite of no overvoltage occurrence, set P9.03 to a small value.
For small-inertia load, the value should be small. Otherwise, the system dynamic response will be slow. For large-inertia load, the
value should be large. Otherwise, the suppression result will be poor and an overvoltage fault may occur. If the overvoltage stall
gain is set to 0, the overvoltage stall function is disabled.
Summary of Contents for elmatic ED2000
Page 1: ......