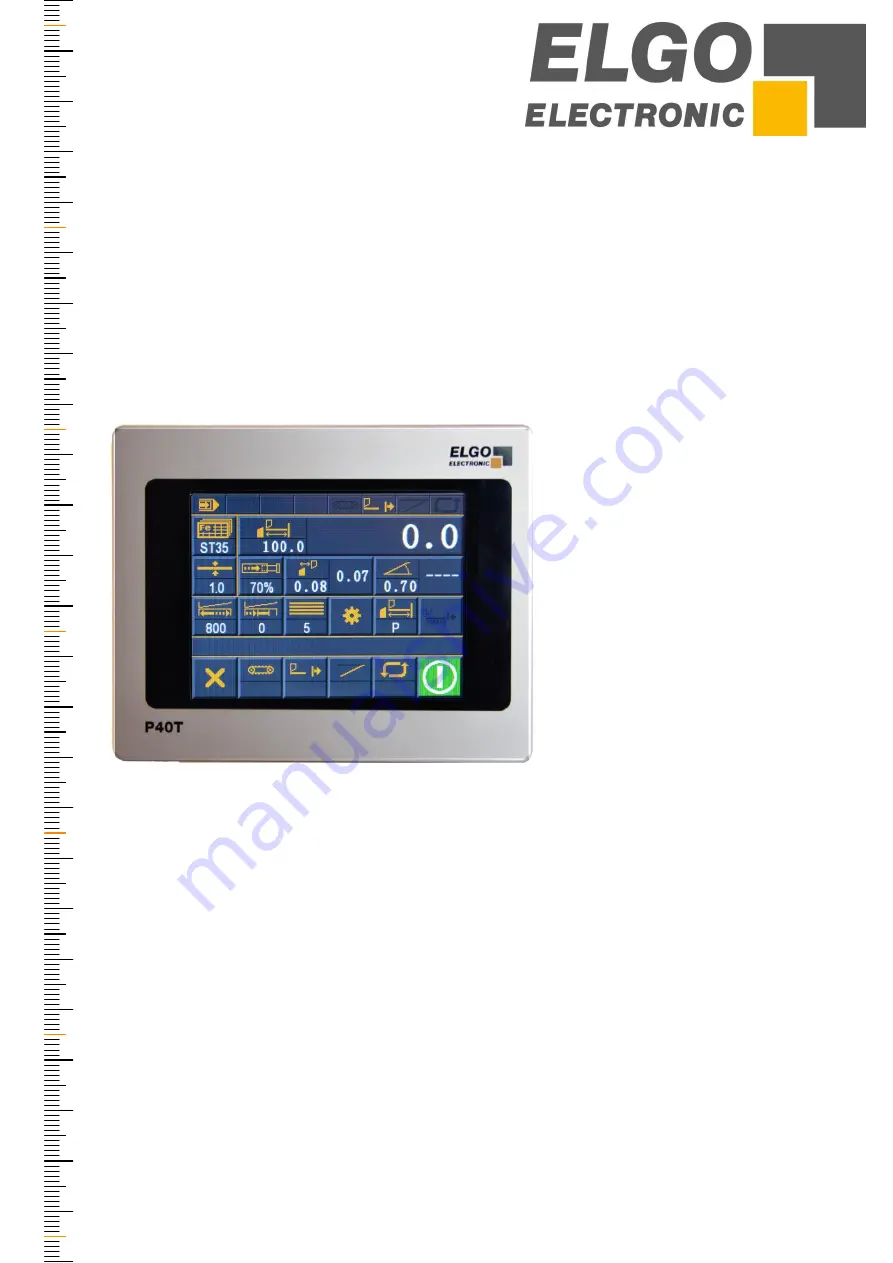
Operation Manual
SERIES P40T-002
Programmable controller for the application of metal shares
(Translation of the original document)
TFT-Display with touch operation
Manual function
Single set operation
Program memory
Digital outputs until 2A
Analog outputs
Material depending gap, angle and pressure calculation
Cut automat
Sheet support
Sheet return
78800681 / Rev. 5
/ 31.03.2014
Summary of Contents for P40T-002
Page 5: ...Content 5 19 Appendix 92 20 Index 100 21 Content of Figures 102 22 Content of Tables 103...
Page 14: ...Technical Data 14 6 2 Dimensions ELGO Ele c troni c P40T...
Page 58: ...Service Mode Parameter Level 58 13 11 Sub Menu Time System Figure 27 System Times...
Page 67: ...Service Mode Parameter Level 67 Set value 6 Park Position backgauge...
Page 75: ...Service Mode Parameter Level 75 Connection examples see Appendix of operation manual...
Page 78: ...Service Mode Parameter Level 78 Connection examples see Appendix of operation manual...
Page 97: ...97 Notes...
Page 98: ...98 Notes...
Page 99: ...99 Notes...