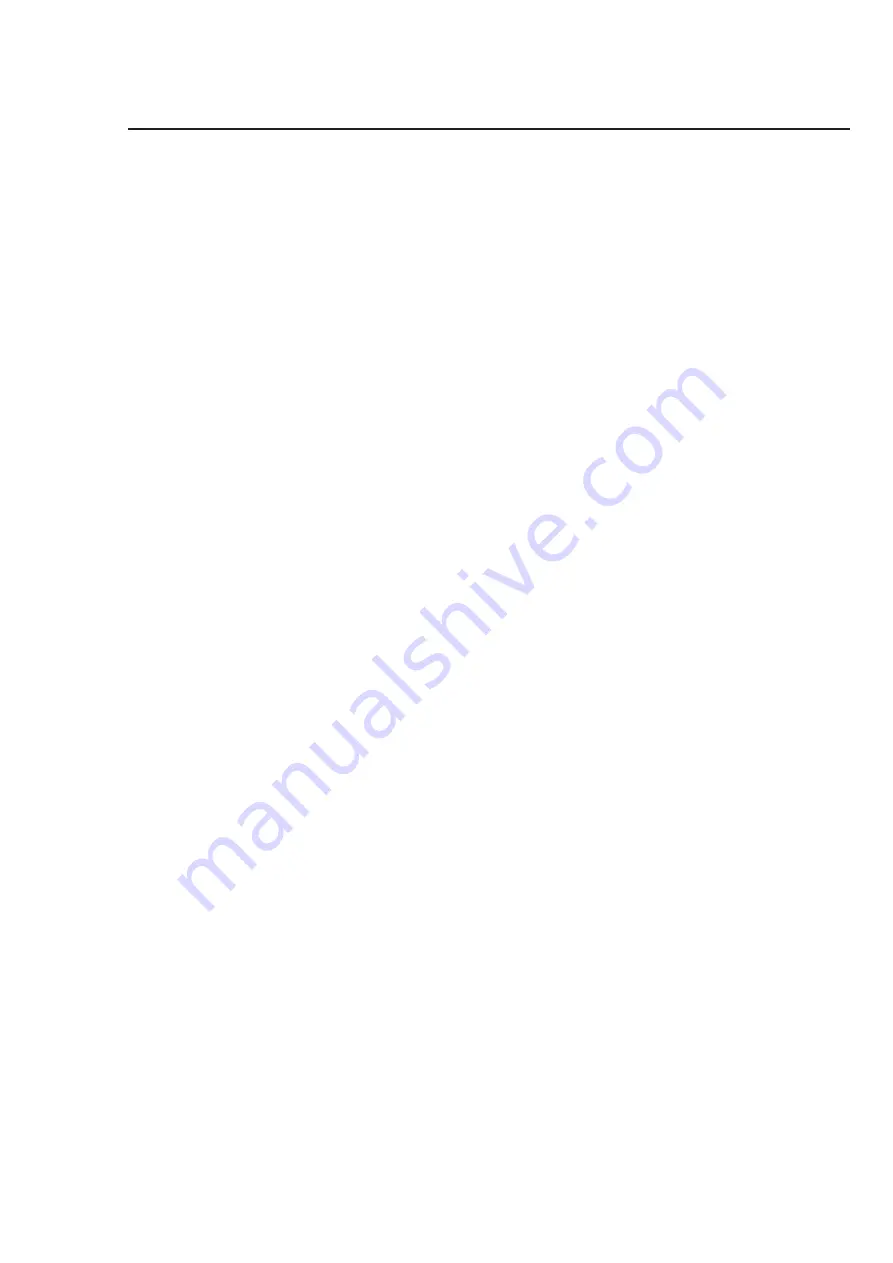
Contents
Contents
Safety precautions .....................................................................................5
Technical data ............................................................................................7
Installation ................................................................................................11
Siting....................................................................................................11
Floor ....................................................................................................11
Casting a plinth....................................................................................12
Installation on an excisting floor or foundation ...................................14
Installation on vinyl floor coverings .....................................................15
Installation, ships, oil-rigs, etc .............................................................16
Welding a foundation ...........................................................................17
Installing the machine ..........................................................................18
Water connections ...............................................................................19
Drain connection .................................................................................21
Steam connection ...............................................................................22
Connection of external liquid supplies ................................................2
Electrical installation ............................................................................28
Function checks .......................................................................................7
The manufacturer reserves the right to make changes to design and
component specifications.