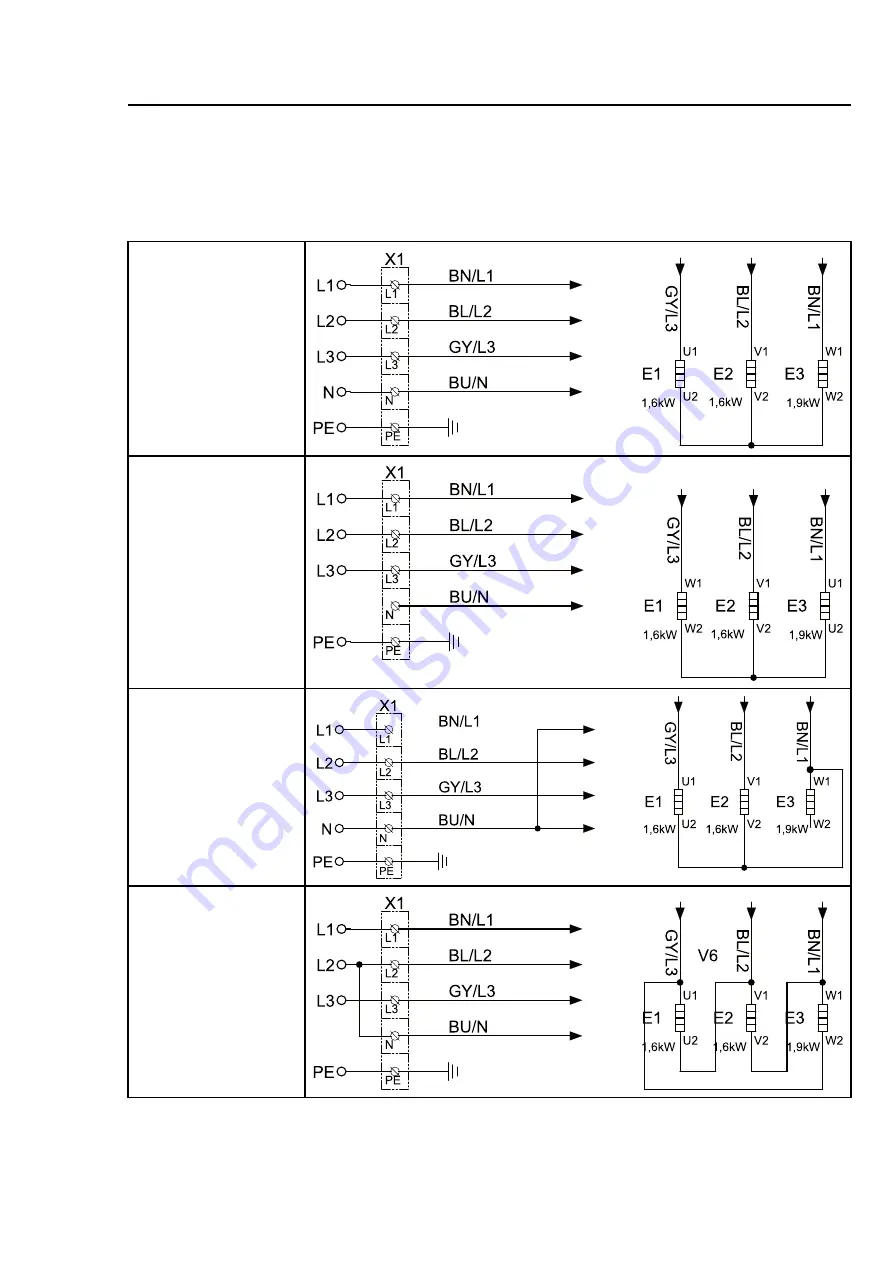
23
7.3 Three-phase connection
Demount the cover panel from the supply unit. Connect the earth and other wires as shown.
Table 1T5130
3 x 400/415V+N
BN/L1
BL/L2
GY/L3
BU/N
G
Y
/L
3
B
L
/L
2
B
N
/L
1
X1
L1
L2
L3
N
P E
U1
U2
E1
1,6kW
V1
V2
E2
1,6kW
W1
W2
E3
1,9kW
L1
L2
L3
P E
N
3 x 400/440V
BN/L1
BL/L2
GY/L3
BU/N
G
Y
/L
3
B
L
/L
2
B
N
/L
1
X1
L1
L2
L3
N
P E
W1
W2
E1
1,6kW
V1
V2
E2
1,6kW
U1
U2
E3
1,9kW
L1
P E
L2
L3
3 x 400/415V+N
B
N
/L
1
U2
U1
V2
V1
W2
W1
B
L
/L
2
G
Y
/L
3
BU/N
GY/L3
BL/L2
BN/L1
E1
E2
E3
1,9kW
1,6kW
1,6kW
X1
L1
L2
L3
N
P E
P E
L3
N
L2
L1
3 x 230/240V
BN/L1
BL/L2
GY/L3
BU/N
V6
G
Y
/L
3
B
L
/L
2
B
N
/L
1
X1
L1
L2
L3
N
P E
U1
U2
E1
1,6kW
W1
W2
E3
1,9kW
V1
V2
E2
1,6kW
L1
P E
L2
L3