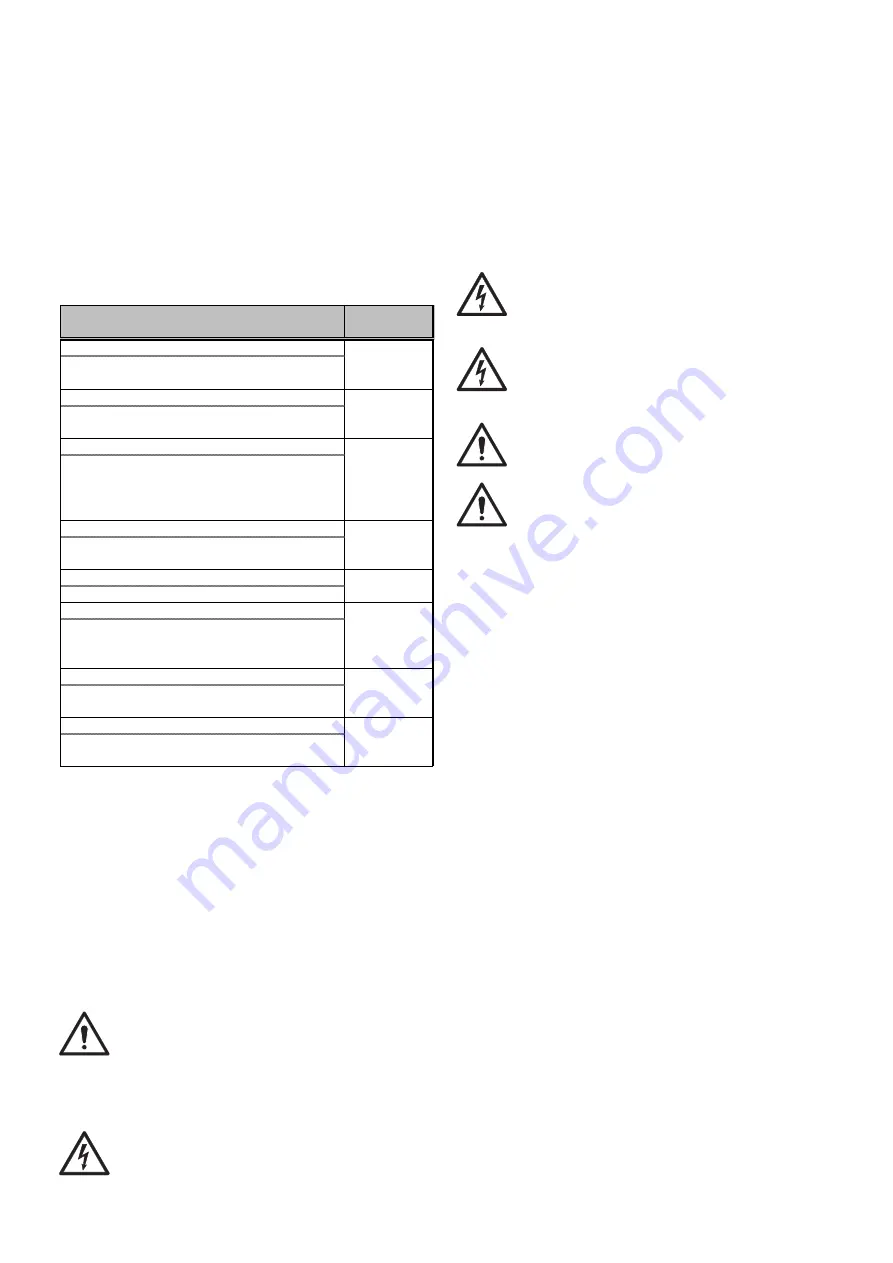
3
9
D.1.3 MAINTENANCE INTERVALS
The inspection and maintenance intervals depend on the
actual machine operation conditions and ambient conditions
(presence of dust, damp, etc.), therefore precise time intervals
cannot be given. In any case, to minimise interruptions of the
service, careful and periodical machine maintenance is
advisable.
It is advisable to stipulate a preventive and scheduled
maintenance contract with the after-sales service.
D.1.3.1 Maintenance frequency
In order to guarantee constant machine efficiency, it is advisable
to carry out the checks with the frequency given in the following
table:
MAINTENANCE, INSPECTIONS, CHECKS AND
CLEANING
FREQUENCY
Routine cleaning
General cleaning of machine and surrounding
area
Mechanical protection devices
Check condition, and for any deformation,
loosening or removed parts.
Control
Check mechanical part, for any breakage or
deformation, tightening of screws. Check
readability and condition of words, stickers and
symbols and restore if necessary.
Machine structure
Tightening of main bolts (screws, fixing systems,
etc.) of machine.
Safety signs
Check readability and condition of safety signs.
Electrical control panel
Check electrical components installed inside the
Electrical Control Panel
. Check wiring between
the Electrical Panel and machine parts.
Electrical connection cable and plug
Check connection cable (replace it if necessary)
and plug.
Extraordinary machine maintenance
Check all components, electrical equipment,
corrosion, pipes, ……
Every 10
years (*)
Daily
Monthly
Yearly
Yearly
Yearly
Yearly
Yearly
(*)
the machine is designed and built for a duration of about 10
years. After this period of time (from machine commissioning)
the machine must undergo a general inspection and overhaul.
Some examples of checks to be carried out are given below.
- check for any oxidised electrical components or parts; if
necessary, replace them and restore the initial conditions;
- check the structure and welded joints in particular;
- check and replace bolts and/or screws, also checking for any
loose components;
- check the electrical and electronic system;
- check the functionality of safety devices;
- check the general condition of protection devices and guards.
ATTENTION!
Machine maintenance, checking and overhaul
operations must only be carried out by a
specialised Technician or the After-Sales Service,
provided with adequate personal protection
equipment (safety shoes, gloves, glasses), tools
and ancillary means.
ATTENTION!
Work on the electrical equipment must only be
carried out by a qualified electrician or the After-
Sales Service.
D.1.4 DISASSEMBLY
If the appliance has to be disassembled and then reassembled,
make sure the various parts are assembled in the correct order
(if necessary mark them during disassembly).
Before disassembling the machine, make sure to carefully
check its physical condition, and in particular any parts of the
structure that can give or break. Before starting disassembly:
- remove all the pieces, if present, in the machine;
- disconnect the power supply;
- enclose the work area;
- place a sign on the Main Electrical Panel indicating that the
machine is undergoing maintenance and not to carry out
manoeuvres;
- carry out the disassembly operations.
ATTENTION!
All scrapping operations must occur with the
machine stopped and cold and the electrical power
supply disconnected.
ATTENTION!
Work on the electrical equipment must only be
carried out by a qualified electrician, with the
power supply disconnected.
ATTENTION!
To carry out these operations, appropriate PPE
must be used.
ATTENTION!
During disassembly and handling of the various
parts, the minimum height from the floor must be
maintained.
D.1.5 DECOMMISSIONING
If the machine cannot be repaired, carry out the decommissioning
operations, signalling the failure with a suitable sign, and
request assistance of the manufacturer’s after-sales service.