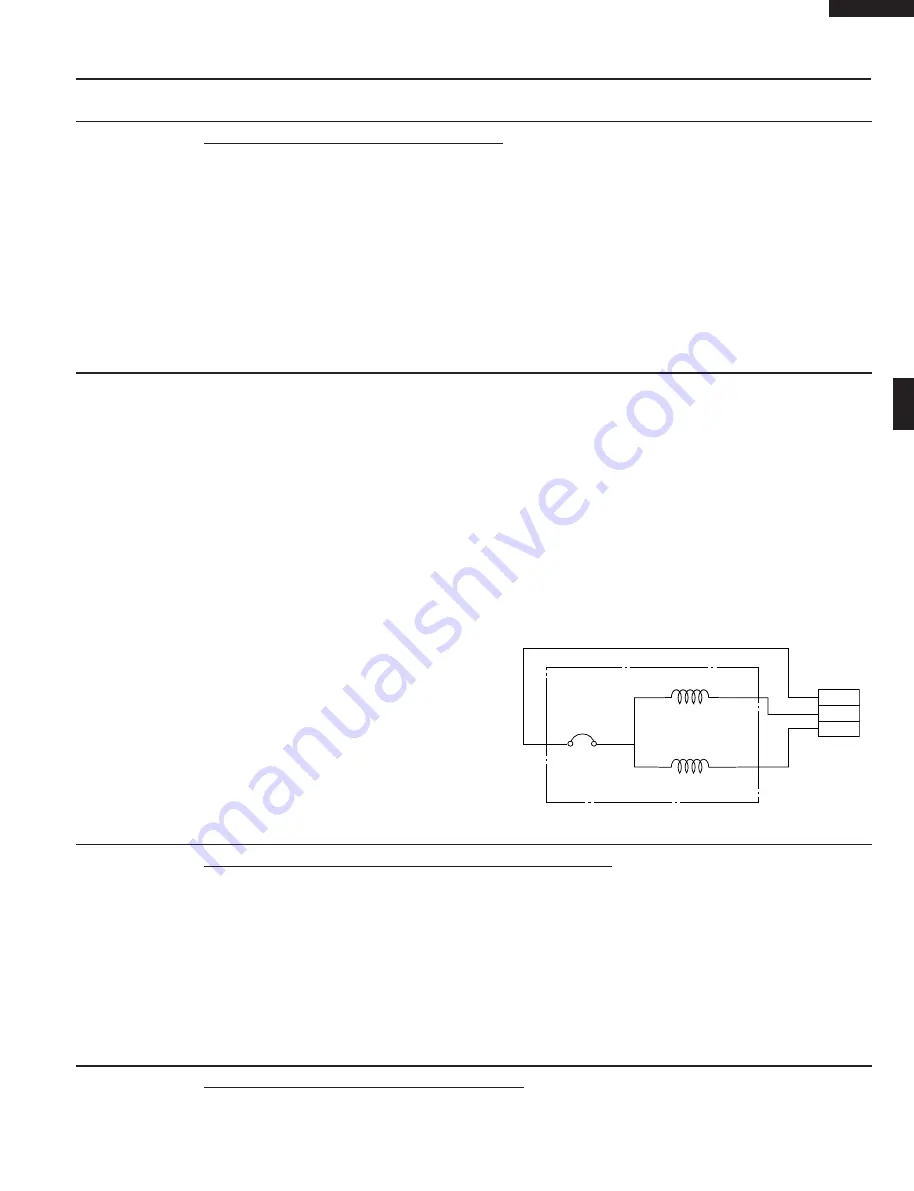
21
E30SO75ESS
TEST PROCEDURES
PROCEDURE
LETTER
COMPONENT TEST
1. Disconnect the power supply cord, and then remove outer case.
2. Open the door and block it open.
3. Discharge high voltage capacitor.
4. Disconnect input leads and check for short or open between the terminals using an ohmmeter.
Checking with a high ohm scale, if the capacitor is normal, the meter will indicate continuity for a short time
and should indicate an open circuit once the capacitor is charged. If the above is not the case, check the
capacitor with an ohmmeter to see if it is shorted between the terminals. If it is shorted, replace the
capacitor.
5. Reconnect all leads removed from components during testing.
6. Reinstall the outer case (cabinet) and the back plate.
7. Reconnect the power supply cord after the outer case and the back plate are installed.
8. Run the oven and check all functions.
R
CONVECTION MOTOR CAPACITOR TEST
BLK
RED
WHT
Main Coil
3-pin
Connector
Sub Coil
Thermal
Cut-out
130ßC OFF
100ßC ON
130‰
140‰
CONVECTION MOTOR
U
TOUCH CONTROL PANEL ASSEMBLY TEST
S
CONVECTION MOTOR TEST
1. Disconnect the power supply cord.
2. Remove the outer case cabinet, referring to “OUTER CASE CABINET REMOVAL”.
3. Open the oven door and block it open.
4. Remove the back plate from the oven, referring to “BACK PLATE REMOVAL”.
5. Disconnect the 3-pin connector of the convection motor from the main wire harness.
6. Measure the resistance of the convection motor with an ohmmeter.
The resistance of the main coil, across the black and the red wires, should be approximately 130 ohms.
The resistance of the sub coil, across the black and the white wires, should be approximately 140 ohms.
7. Also, the convection motor has the thermal cut-out in it.
Measure the resistance of the main coil (or the sub coil). The resistance across the black and the red wires
(or across the black and the white wires) should be above resistance unless the temperature of the thermal
cut-out reaches approximately 266
ο
F (130
ο
C). The thermal cut-out resets automatically at 212
ο
F (100
ο
C).
If an ohmmeter indicates an open circuit under normal condition, replace the convection motor because
the thermal cut-out has opened. An open thermal cut-out indicates overheating of the convection motor.
Check for restricted air flow to the convection
motor or a lock of the convection fan, especially
the fan motor (power transformer side).
8. Reconnect all leads removed from
components during testing.
9. Reinstall the outer case (cabinet) and the
back plate.
10. Reconnect the power supply cord after the
outer case and the back plate are installed.
11. Run the oven and check all functions.
The following test procedure should be carried out with the microwave oven is a fully assembled
condition (outer case fitted).
It is difficult to measure the exact temperature in the convection oven. An accurate thermocouple type
temperature tester must be used. A low priced bi-metal type thermometer is not reliable or accurate.
The temperature should be checked with outer case cabinet installed, approx. 5 minutes after preheat
temperature is reached (audible signal sounds four times). The temperature experienced may be approx.
30½F more or less than indicated on the display, however, in most cases the food cooking results will be
satisfactory.
Difference in power supply voltage will also affect the oven temperature. The Household power supply voltage
may sometimes become lower than the rated voltage (240 V) and cause under-cooking. If the power supply
voltage is 10% lower than the rated voltage, longer cooking time is required by 10% to 20%.
T
CHECKING TEMPERATURE IN THE CONVECTION MODE
The touch control panel consists of circuits including semiconductors such as LSI, ICs, etc. Therefore, unlike
conventional microwave ovens, proper maintenance cannot be performed with only a voltmeter and
ohmmeter.
Summary of Contents for E30SO75ESS - 30" Wall Oven
Page 50: ...48 E30SO75ESS NOTES ...
Page 51: ...49 E30SO75ESS NOTES ...