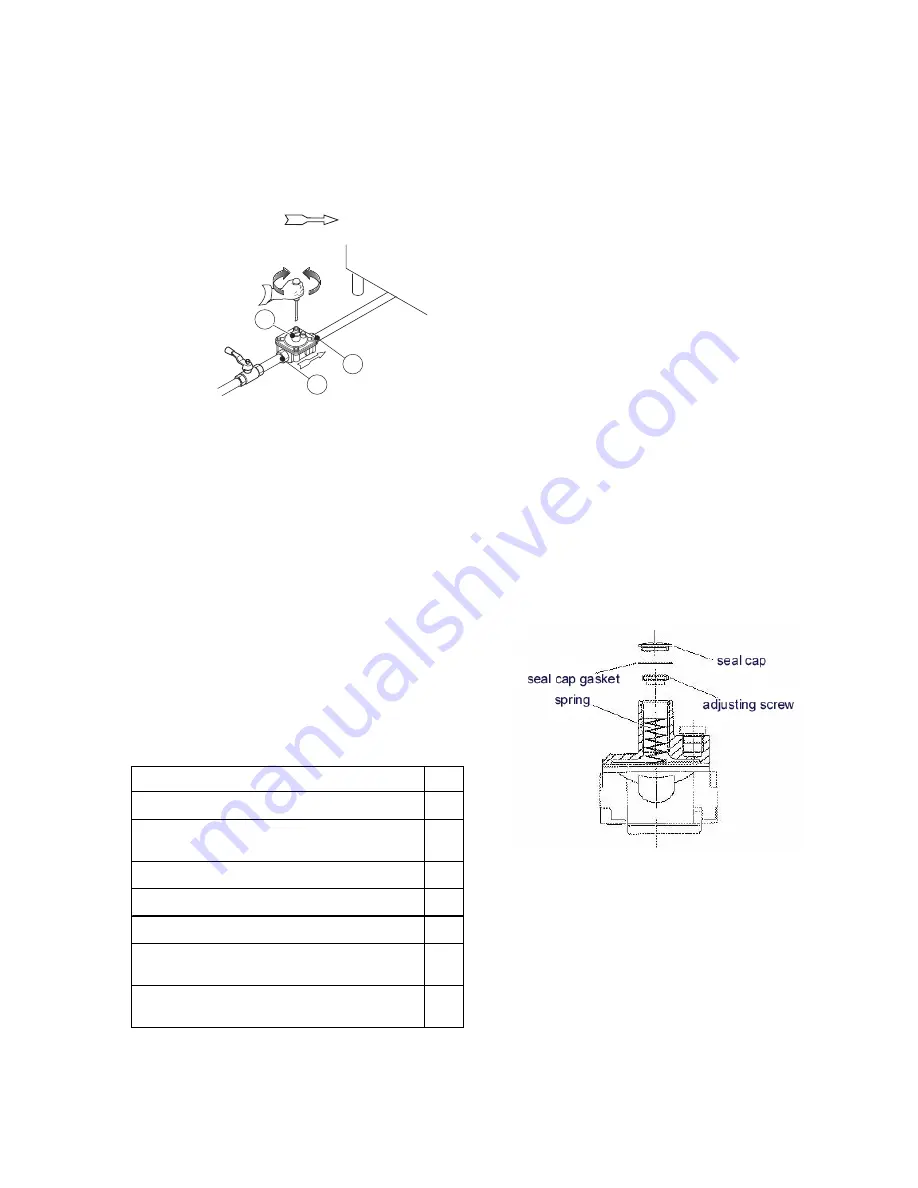
25
5.1.4 GAS PRESSURE REGULATOR
•
A gas pressure regulator (supplied in a plastic bag with the
appliance)must be installed in an easily accessed posi-
tion ahead of the appliance.
The pressure regulator should preferably be fitted horizontally,
to ensure the right outlet pressure:
•
“1” connection side gas from mains.
•
“2” pressure regulator (3.3"x2.9"x2.7" / 85x75x71mm);
•
“3” connection side gas towards the appliance;
The arrow on the regulator (
) indicates the gas flow
direction.
3
1
2
AUSTRALIA: the gas pressure regulator supplied with the
appliance must be fitted to the appliance inlet. Adjust the
test point pressure with all hob burners operating at maximum
setting as follow:
- 1.0 KPa for Natural gas
- 1.8 KPa for Propane gas
5.1.5. PRIMARY AIR CHECK
When the primary air is correctly adjusted, the flame does
not “float” with burner cold and there is no flareback with
burner hot.
•
Undo screw “A” and position aerator “C” at distance “H”
given in Table B; retighten screw “A” and seal with paint
(fig. 3A).
5.1.6. CONVERSION TO ANOTHER TYPE OF GAS
Table B “Technical data/gas nozzles” gives the types of
nozzles (contained in a bag supplied with the appliance,
together with the pressure regulator) to be used when
replacing those fitted by the manufacturer; the number is
stamped on the nozzle body. At the end of the procedure,
carry out the following check-list:
Check
Ok
• burner nozzle/s replacement
• correct adjustment of primary air supply to
burner/s
• pilot nozzle/s replacement
• minimum flame screw/s replacement
• correct adjustment pilot/s if necessary
• correct adjustment of supply pressure
(see technical data/gas nozzles table)
• apply sticker (supplied) with data of new gas
type used
5.1.6.1 MAIN BURNER NOZZLE REPLACEMENT
•
Remove the control panel.
•
Unscrew nozzle “C” and replace it with one suitable for
the type of gas (fig.3A) according to that given in Table B.
•
The nozzle diameter is given in hundredths of mm on the
nozzle body.
•
Tighten down nozzle “C”.
5.1.6.2 PILOT BURNER NOZZLE REPLACEMENT
•
Remove the control panel.
•
Undo screw coupling “H” and replace nozzle “G” with one
suitable for the type of gas (Table B, fig.3b).
•
The nozzle identification number is given on the nozzle
body.
•
Retighten screw coupling “H”.
5.1.6.3 REPLACING THE ADJUSTMENT SPRING OF
THE PRESSURE REGULATOR
•
Replace the spring of the pressure regulator with one
suitable for the gas pressure type given in table B (see
handbook Appendix) as follows:
-
Remove the seal cap, seal cap gasket, adjusting screw
and the spring.
-
Insert the new spring and replace the adjusting screw.
-
Connect a pressure gauge to the appliance’s test point
pressure (fig. 2A/2B).
-
Ignite the appliance’s burners so to have the maximum
gas consumption.
-
Regulate the adjustment screw until the pressure gauge
shows the working pressure value (section 5.1.4 Gas
pressure regulator).
-
Replace the seal cap and gasket and screw tightly closed.
-
Remove the pressure gauge and close the test point
pressure.
-
Prior to operation, test the gas pressure regulator for leaks.
6. BEFORE COMPLETING THE
INSTALLATION OPERATIONS
Use soapy water to check all gas connections for leaks. DO
NOT use a naked flame to check for gas leaks. Light all the
burners individually and also together, to check correct
operation of the gas valves, rings and lighting. For each
burner, adjust the flame regulator to the lowest setting,
individually and together; after completing the operations,
the installer must instruct the user on the correct method of
use. If the appliance does not work properly after carrying
out all the checks, contact the local after-sales service
centre.