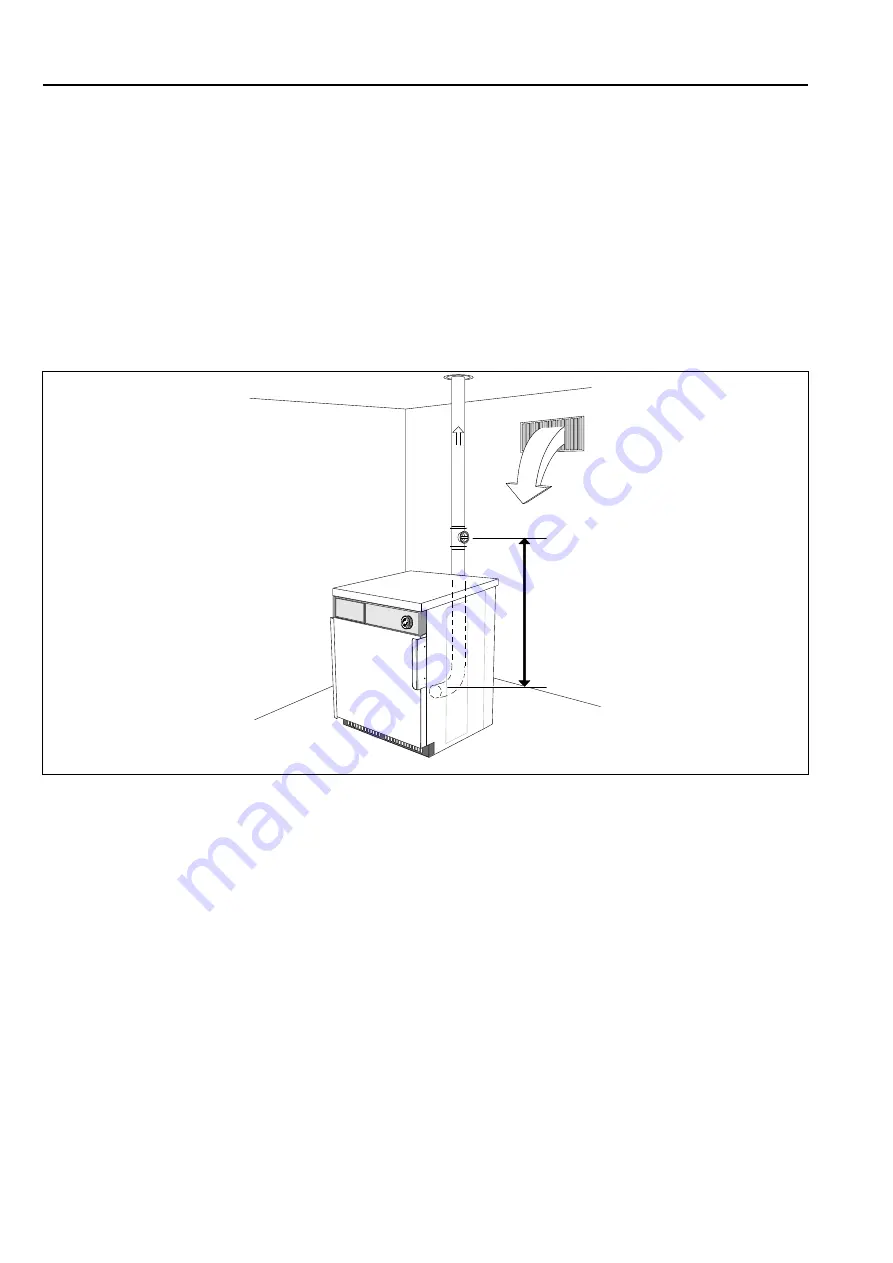
14
Installation manual
5.3
Calibration of air damper
To fulfill the requirements in standard ISO 6330:2012, the air flow in the machine needs to be adjusted. Adjustment
of air flow is preferably done with an air damper installed in the outlet pipe of the dryer.
The air flow should be adjusted to 140±5 m
3
/h. If flow meter is not available, adjust air flow to a peak inlet tempera-
ture of 120-125°C. Check maximum inlet temperature with the following procedure:
• Start a
NORMAL LAB
program without load
• Activate the
STATUS
menu and monitor inlet temperature.
• Start adjustment procedure with fully open damper.
• After approximate 10 min heating, adjust damper to peak inlet temperature of 120-125°C. To increase temperature
– close damper, to decrease temperature open damper. Note that the inlet temperature vary due to temperature
control. Peak inlet temperature should reach 120-125°C.
• Continue to monitor for 10-15 min and if needed readjust air flow.
• Lock air damper setting after adjustment.
A
5 x A
1 m