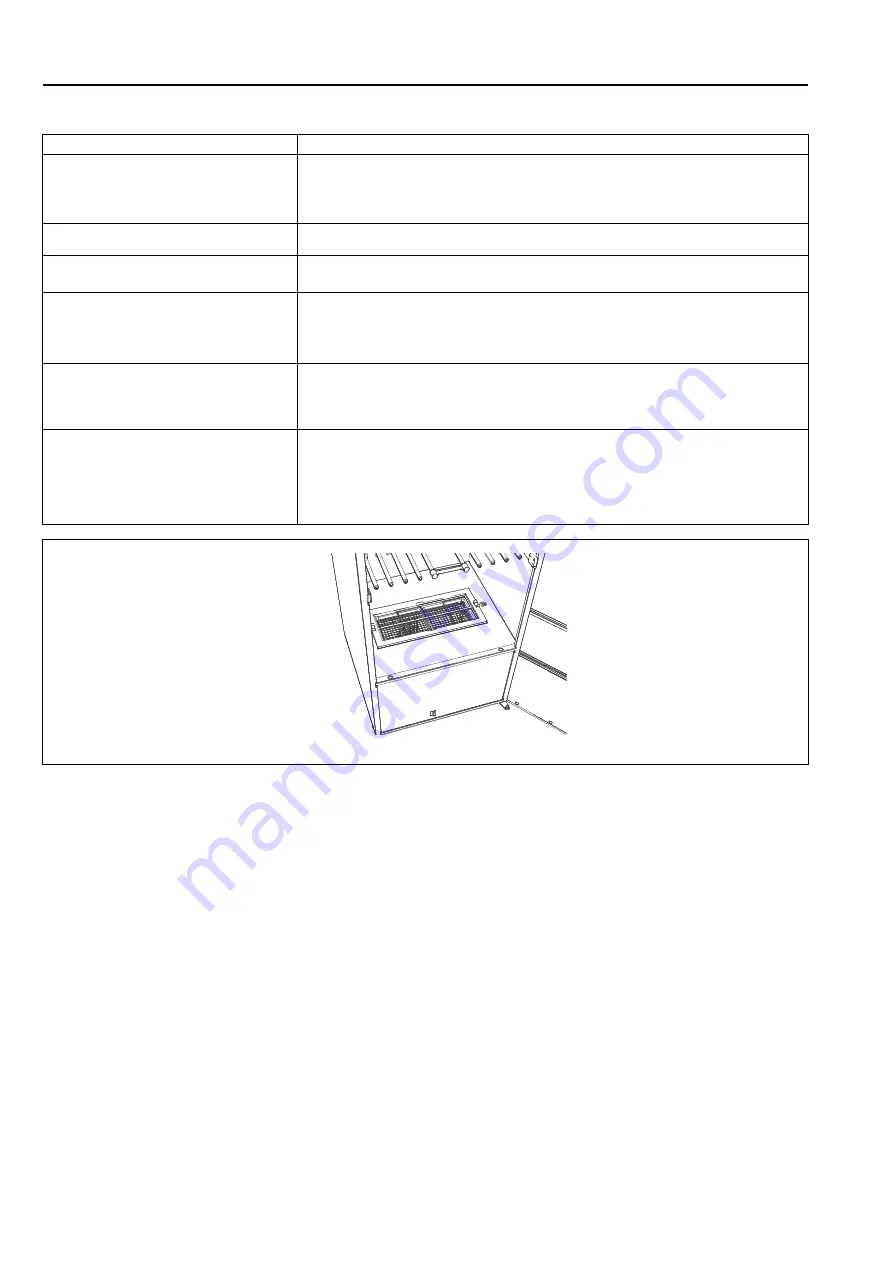
14
User manual
8 Troubleshooting
Problem
What you can do
The drying cabinet does not work
1. Check that the power cord is connected to an electrical outlet.
2. Check that no fuse has been tripped.
3. Did you press the start button?
4. Is the door closed?
The display shows "Check Water Pump"
The safety switch for defective pump has been activated. If this is the case, a service techni-
cian must be called.
The display shows "Clean Filter"
See the figure below
Clean the cleaning filter and restart the cabinet.
The Stop button must be held depressed for 5 seconds to reset the alarm.
Drying takes a long time
1. Clean the cleaning filter (must be done after each drying session).
2. Check that the right program was selected for the type of garments in question.
3. Check to ensure the garments are not extremely wet (poorly centrifuged).
4. Check that there is not too much laundry in the cabinet.
The laundry does not get dry
1. Check that the right program was selected for the type of garments in question.
2. Check that there is not too much laundry in the cabinet.
3. The software that controls the drying process requires adjustment. Contact a service
technician.
The sealing strip does not create a seal/there
is a gap at the door
1. Check that the cabinet is level. Check with a spirit level and adjust via the adjustable feet if
necessary.
2. Check that the cleaning filter and its holder are correctly installed. The holder should be
pressed against the underlying heat pump unit to seal properly.
3. Make sure that no debris, gravel or the like has ended up under the cleaning filter holder,
as this would prevent it from sealing properly.
fig.W01300
Cleaning filter under the shoe rack
Summary of Contents for DC6-4HP
Page 1: ...User manual Drying cabinet DC6 4HP Original instructions 427001219 EN 2022 02 22 ...
Page 2: ......
Page 4: ......
Page 17: ......
Page 18: ......
Page 19: ......
Page 20: ...Electrolux Professional AB 341 80 Ljungby Sweden www electroluxprofessional com ...