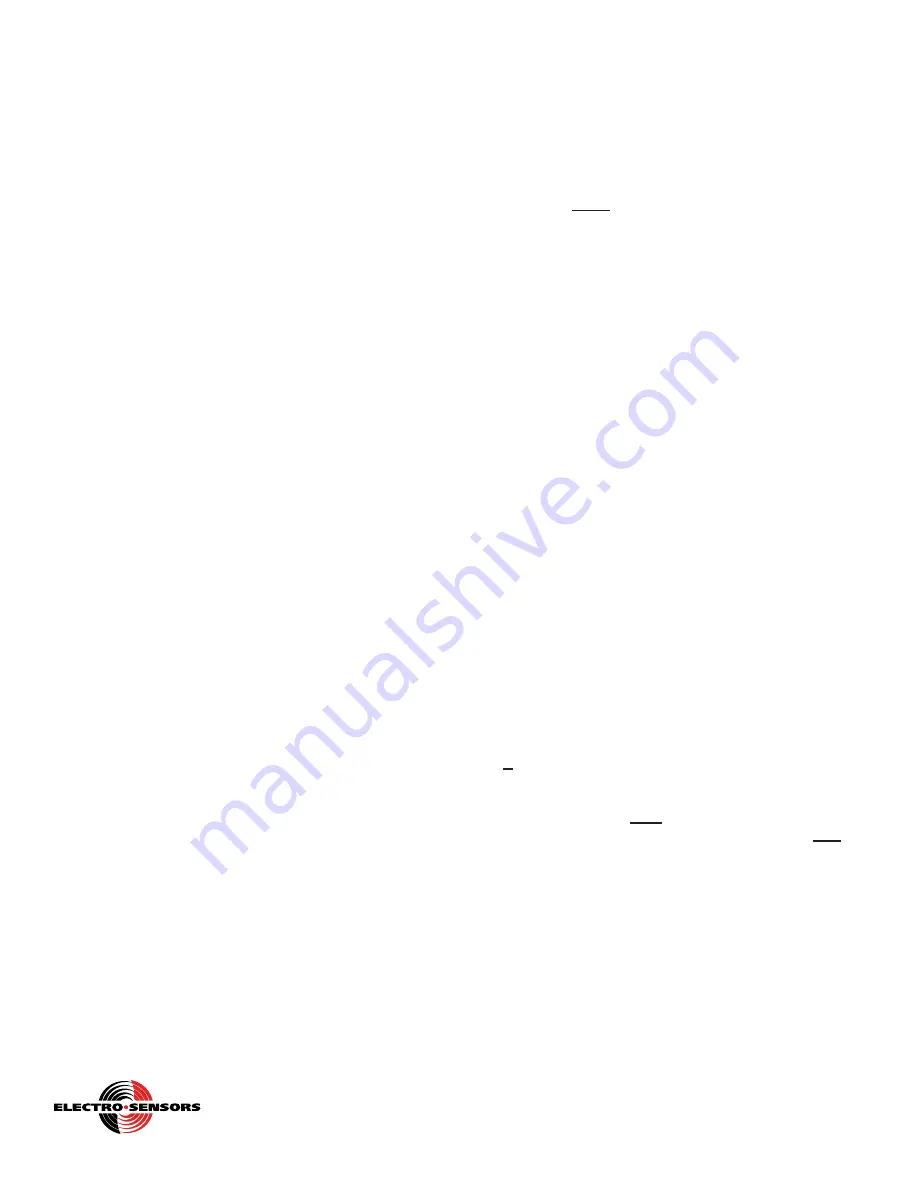
Valid Calibration (cont.)
• If the process shaft is moved to a position that is slightly
beyond (outside of) the fully-open (100% open) calibrated
position, then the output signal remains at 20 mA. This is
known as 100% ‘run-out’, and it holds to a certain point.
If the encoder is turned far enough beyond the fully-open
calibrated position, then the encoder “wraps-around” and the
output signal jumps to the fully-closed value of 4 mA.
• For a properly calibrated SG1000F, the direction of
calibration (CW or CCW), and the encoder values for the
fully-closed and fully-open process shaft positions are all
stored in the SG1000F’s EEPROM memory.
Note:
Since a properly calibrated SG1000F can never enter the
calibration mode again by itself after the calibration mode
is exited, the direction switch SW1 and the calibration
switch SW2 are ignored (during normal operating mode).
This means that for a properly calibrated SG1000F the
calibration results are protected until the user wants to
purposefully enter calibration mode again.
If re-calibration is needed, see the section below titled
“
How to clear-out the existing calibration and
reprogram the SG1000F.”
Invalid Calibration (Error condition behavior)
Assuming the user followed the calibration procedure
incorrectly
, the SG1000F behaves as follows:
• The output signal remains at a constant 12 mA after the
calibration mode is automatically exited.
An “invalid calibration” is most likely due to one of the
following errors:
- If the user did not move the process shaft (or moved it but
less than a 30º turn) between teaching the SG1000F the
fully-closed and fully-open positions, then the closed and
open positions have the same (or nearly the same) encoder
count.
- The user “double-pressed” SW2 during power-up or while
teaching the SG1000F the fully-closed position.
Power-ups; calibration vs. normal operating mode
• An SG1000F that is un-calibrated (or if the calibration
attempt was invalid) automatically powers-up in the
calibration mode, the next time power is applied.
• A properly calibrated SG1000F powers-up in the normal
operating mode, when power is applied.
• If the user accesses calibration mode via the “power-up”
method then any previous calibration is immediately cleared.
• If the user accesses calibration mode via the “on-the-fly”
method, then any previous calibration is retained until the
new calibration points have been acquired. (This allows
the user the option to bail out of calibration mode before
completing the new calibration by simply removing the
+24Vdc power. In this case of intended power interruption,
the EEPROM never gets called to save any new calibration,
thus the old calibration is retained).
Troubleshooting Hints
As an aid to troubleshooting, see figure 3 on how to connect an
ammeter to directly measure the 4-20mA output signal.
1) If your SG1000F outputs a 4 mA to 20 mA signal, but not at
the process shaft positions expected, then double-check the
following:
A) Before you performed the calibration procedure, did you
set the direction switch SW1 to the proper position (CW
or CCW) before entering calibration mode?
B) As your process shaft moves from fully-closed to fully-
open, does the SG1000F’s encoder shaft turn more than
718º (i.e. two turns), or less than a 30º turn? If so, then
the SG1000F will not work in your application.
C) Is your SG1000F terminal TB1 wiring correct?
• Power supply (+24Vdc) terminal red wire is TB1-1.
• 4-20mA signal clear wire is TB1-2.
• Power supply (-) terminal black wire is TB1-3.
D) Assuming conditions (A), (B), and (C) are proper, and
your SG1000F still seems to behave improperly, then try
re-calibrating again, paying close attention to the eight
calibration steps.
2) If you have gone through troubleshooting hints (1A), (1B),
(1C), and (1D), and if your SG1000F seems to otherwise
respond properly, from fully-closed to fully-open, with
the only exception being that strange values other than 4
mA and 20 mA are output for the fully-closed/fully-open
positions (e.g., 3 mA at one-end and 23 mA at the other-
end), then possibly the R7 and R8 factory potentiometer
settings have been tampered with. See Figure 4 for
location of these pots.
Evidence of R7 and R8 tampering is most easily seen
when in the calibration mode. When R7 and R8 are at
their factory-settings, the output signal is 12 mA during
calibration mode. (Recall that the output signal remains
at 12 mA until the calibration procedure is completed). If
during calibration mode the output signal is not 12 mA,
then most likely the R7 and R8 factory-settings have been
tampered with.
If
you feel confident that you have followed the calibration
procedure properly (perhaps have done it several times
over), and followed the troubleshooting hints in (1A),
(1B),(1C), and (1D),
AND
you still see strange values
other than 4 mA at one end and 20 mA at the other,
then
you can attempt to restore R7 and R8 to the factory-settings
by doing the following: (This assumes you have already
calibrated your SG1000F for the fully-closed and fully-
open process shaft positions).
A) During normal operating mode, move the process shaft
to your fully-closed calibrated position. Adjust R7
until 4 mA is output from the signal line.
B) During normal operating mode, move the process shaft
to the fully-open calibrated position. Adjust R8 until
20 mA is output from the signal line.
C) You can now test and verify that your R7 and R8 are
3-4
Free Catalog and Application Assistance
1.800.328.6170
Website: www.electro-sensors.com
990-002450 Revision C