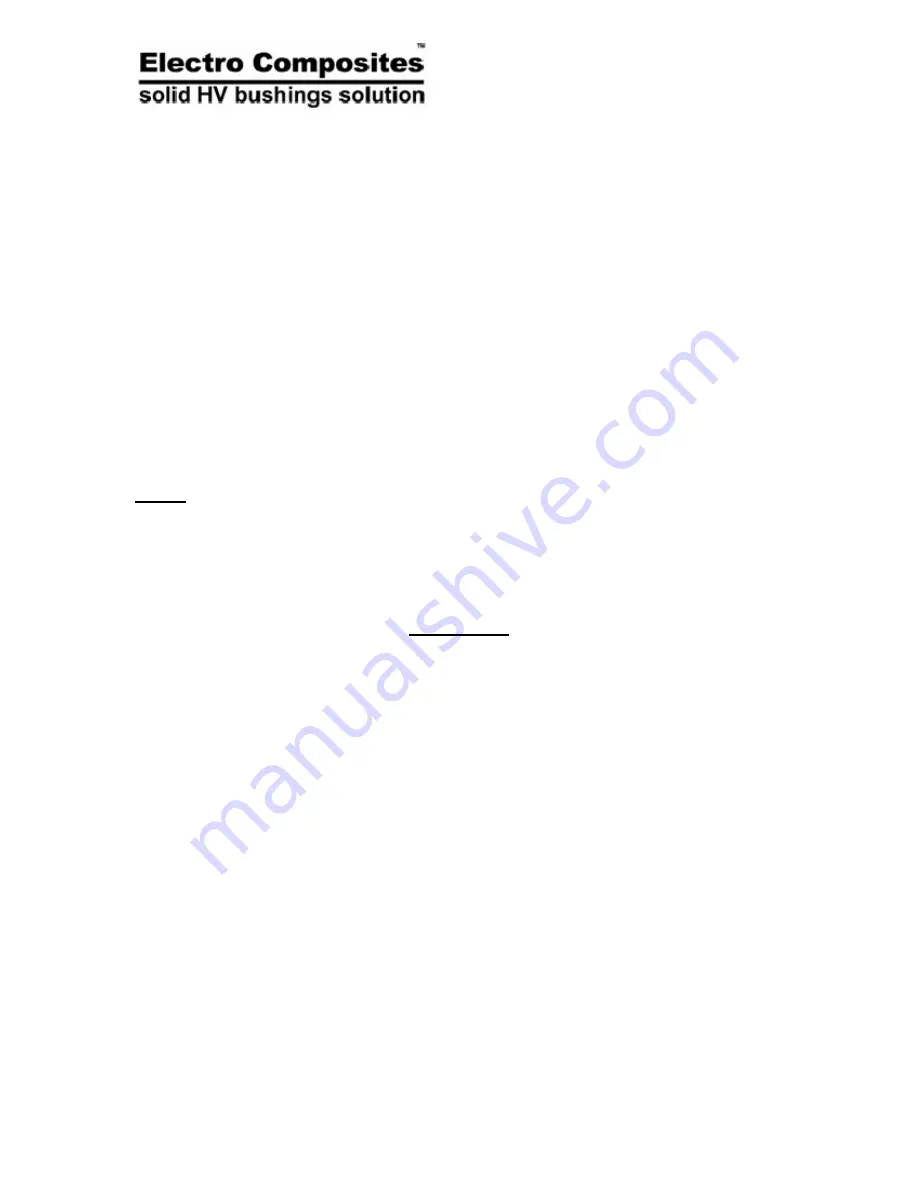
Page
8
of
12
INSTALLATION/TESTING
Before installation, remove all wrapping material and foreign particles from the bushing.
Clean the conductor end terminal threads, aluminum flange seat and wipe clean the
epoxy (grey color) insulation with a dry clean cloth (both ends). The insulation can also
be thoroughly cleaned with a clean cloth and isopropyl alcohol or acetone to remove any
trace oil or grease that may be present.
We recommend performing the capacitance and power factor tests prior to energizing
the bushing. Remove the bushing from its crate and clean beforehand. Refer to the
Doble M400 Test set instructions, the Doble Bushing Field Test and our Routine Test
Report for the measured values (these should match the values indicated on the bushing
name plate). Bushings can be tested immediately after removal from the crate.
Discrepancies between the measured values and the indicated values on the name plate
can occur since nameplate values are obtained under controlled conditions at the
factory. Values measured at receiving should be used as a baseline to compare with
future field measurements. Only C1 power factor and capacitance have meanings for
SDC
TM
bushings
NOTE:
Electro Composites (2008) ULC recommends against measuring C2 power
factor and capacitance of our bushings for any purpose. Should C2 power factor
and capacitance measurements be part of your tracking procedure,
measurements should be made once the bushing is installed on the equipment.
Measured values can then be used as benchmarks for monitoring purposes.
Values will generally vary from nameplate.
ATTENTION!
Never test the bushing while in the shipping crate
When possible, place the bushing in a grounded test stand. It is important
to isolate the flange from the grounded stand using a good insulation
material. Wood can contain significant moisture and should not be used.
The readings may be taken with the bushing installed in the equipment
provided that top terminal connections are not made.