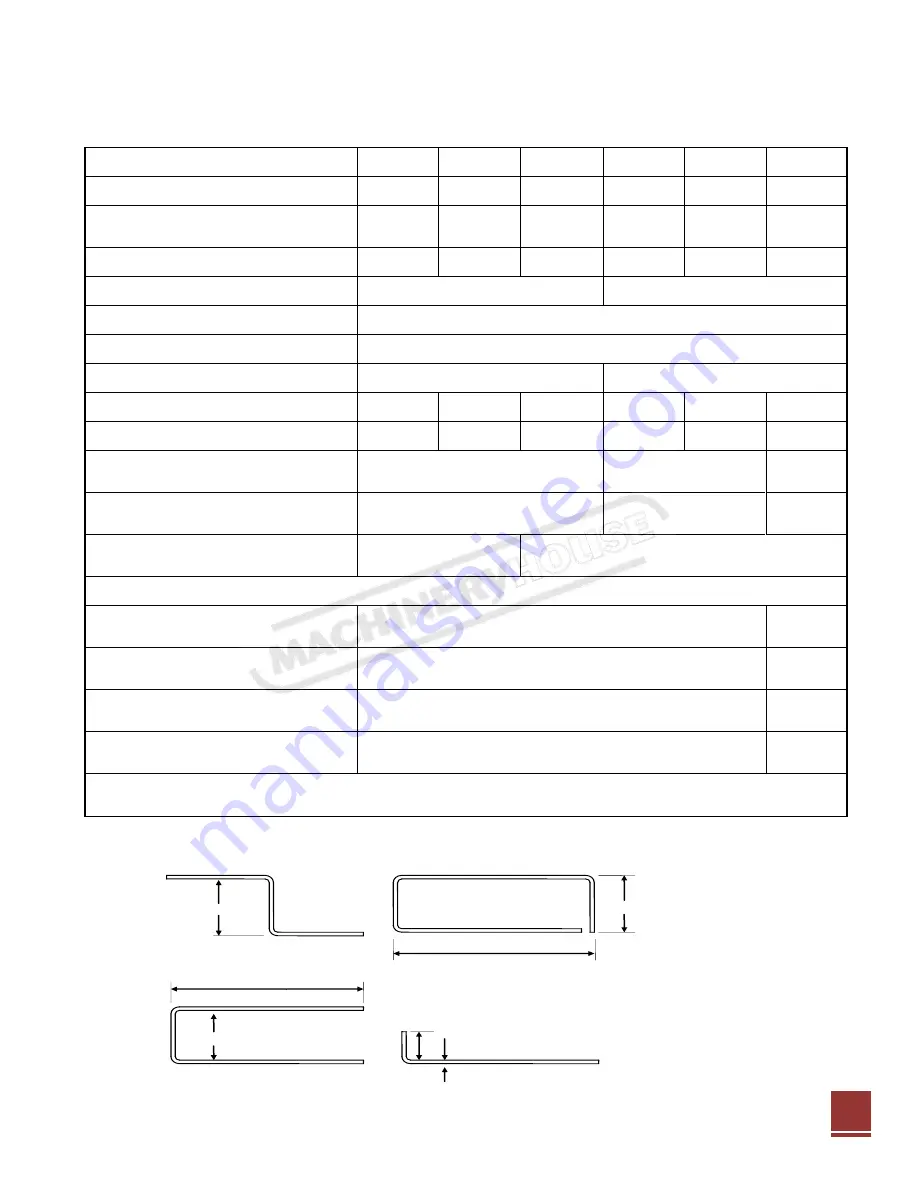
27
SPECIFICATION SHEET
Model
EB0625
EB1000
EB1250
EB2000
EB2500
EB3200
Weight of Machine
Kg
72
110
150
270
315
380
Nominal Capacity
(length
x thickness)
mm
0625
x1.6
1000 x
1.6
1250 x
1.6
2000 x
1.6
2500 x
1.6
3200 x
1.2
Clamping Force
Tons
3
4.5
6
9
12
10
Electricity Supply
1 phase, 220/240vac, 10A
1 phase, 220/240vac, 16A
Duty Cycle
%
30
Protection
°C
Thermal cut-out 70°/80°C
Foot Switch
No
Standard
Bending-edge Length
mm
670
1050
1300
2090
2590
3290
Distance between Lifters
mm
630
1010
1260
2028
2528
3228
U-Channel bends,
minimum spacing
mm
16***
19***
45***
Closed channel,
minimum
internal
mm
99 x 27***
114 x 22***
114 x
45***
Z-reverse bends,
minimum
spacing
mm
35** / 16*
36** / 18*
Thickness Capacities, full length
(material thickness can increase depending on the length of bend)
…Mild steel
mm
1.6** / 1.2*
1.2** /
1.0*
…Aluminium (medium-
hard)
mm
1.6** / 1.2*
1.2** /
1.0*
…Copper, Zinc, Brass
(medium-hard)
mm
1.6** / 1.2*
1.2** /
1.0*
…Stainless steel
mm
1.0** / 0.9*
0.9** /
0.8*
*** with standard full length clamp bar **with bending beam extension bar *extension bar
removed
Bending dimensions.
Refer to Chart
19mm
(min)
19mm (min)
- 98mm (min) Standard Clampbar
- 49mm (min) Narrow Clampbar
19mm (min)
Unlimited
27
Instruction Manual for EB2500 (S5321)
24/8/2012
Summary of Contents for EB0625
Page 4: ...4 4 Instruction Manual for EB2500 S5321 24 8 2012 ...
Page 5: ...5 5 Instruction Manual for EB2500 S5321 24 8 2012 ...
Page 6: ...6 6 Instruction Manual for EB2500 S5321 24 8 2012 ...
Page 23: ...23 EB0625 AND EB1000 PANEL 23 Instruction Manual for EB2500 S5321 24 8 2012 ...
Page 24: ...24 EB 2000 TO 3200 WIRE PANEL 24 Instruction Manual for EB2500 S5321 24 8 2012 ...
Page 25: ...25 EB 0625 1250 CIRCUIT 25 Instruction Manual for EB2500 S5321 24 8 2012 ...
Page 26: ...26 EB 2000 EB3200 CIRCUIT DIAGRAM 26 Instruction Manual for EB2500 S5321 24 8 2012 ...
Page 29: ...29 DIMENSIONAL SPECIFICATIONS EB1250 29 Instruction Manual for EB2500 S5321 24 8 2012 ...
Page 31: ...31 DIMENSIONAL SPECIFICATIONS EB3200 31 Instruction Manual for EB2500 S5321 24 8 2012 ...
Page 35: ...37 35 Instruction Manual for EB2500 S5321 24 8 2012 ...