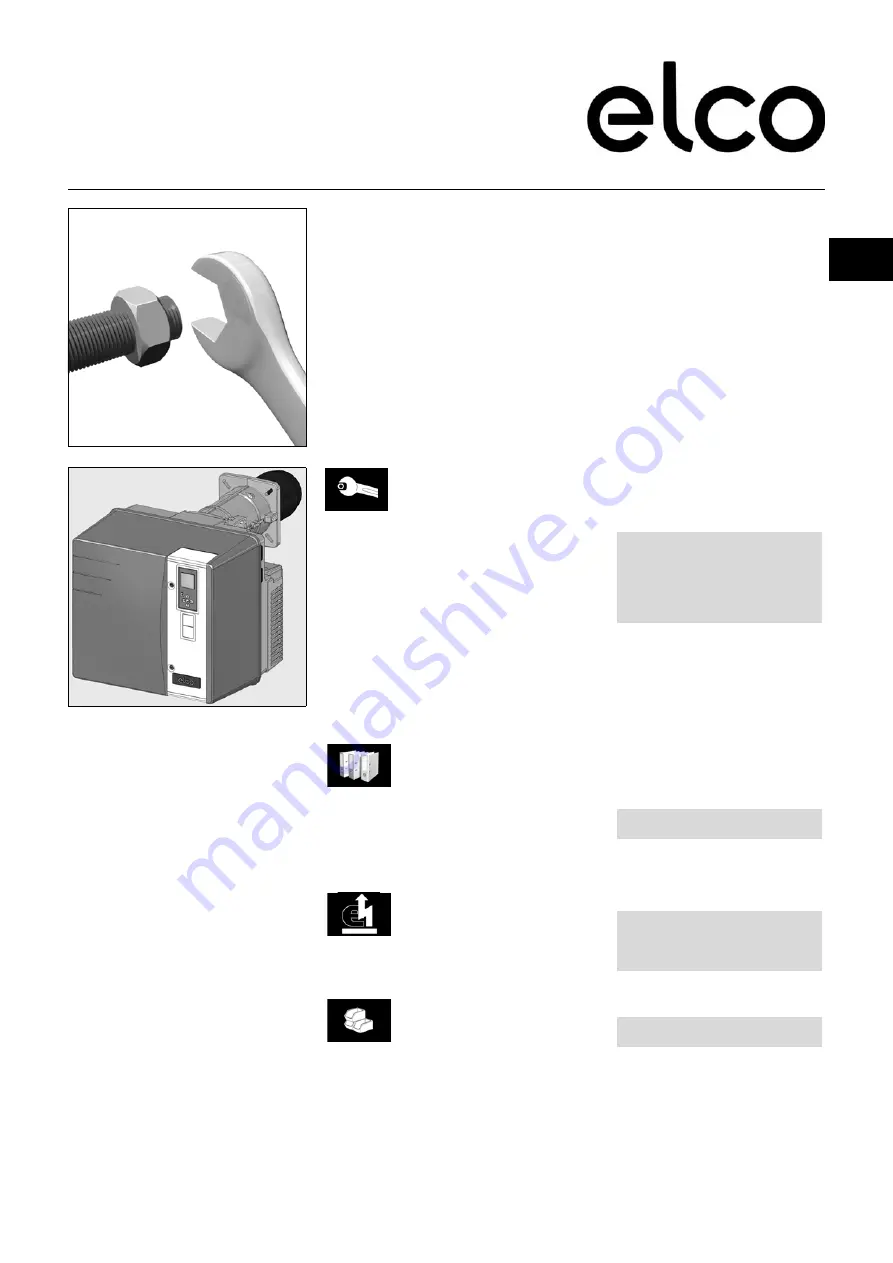
06/2016 - Art. Nr. 4200 1041 1103A
en
......................................... 4200 1060 1202
VG5 M/TC (PED) 4201 1006 6900
VG5 MV/TC (PED) 4201 1016 9500
Original operating instructions
For authorised specialist engineers
Gas burners
VG5.950 M(V)/TC (/PED)
VG5.1200 M(V)/TC (/PED)
de, fr................................. 4200 1041 0903
it, nl.................................. 4200 1041 1003
en..................................... 4200 1041 1103
de, fr, it, nl, en................. 4200 1041 0803