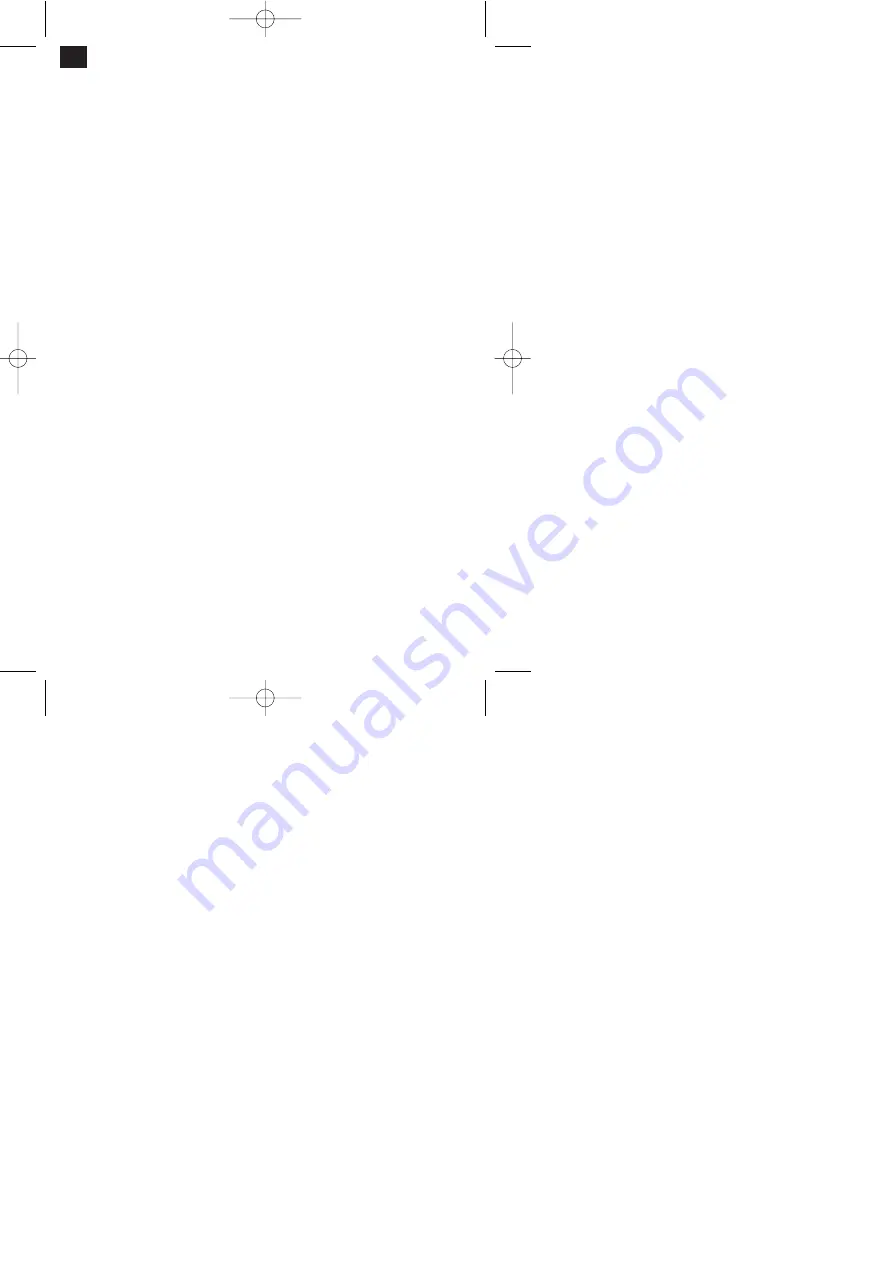
GB
6
2.
If you are not acquainted with the use of a
cutting-off machine, get advice from a
supervisor, trainer or other qualified person.
3.
Wear safety goggles, a visor, a breathing mask,
an apron, safety shoes, long tight sleeves and
gloves.
4.
Use only recommended, reinforced cutting-off
wheels.
5.
Securely tighten the shaft screw and all clamps
before beginning your work.
6.
Make sure that the shaft lock is released before
starting.
7.
Always leave the safety devices in position and
make sure that they are in good working order.
8.
Keep your hands away from the cutting-off
wheel.
9.
Secure the workpiece carefully. It has to be
securely clamped in a straight position in order to
prevent it from moving and skewing while the cut
is being made.
10. Never cut free-handed.
11. Never reach behind or near the cutting-off wheel.
12. Make sure that the cutting-off wheel stops
completely before you remove the workpiece,
clamp in a new workpiece, or adjust the angle.
13. Make sure that there are no foreign bodies on
the cutting-off wheel and flange.
14. When you fit a cutting-off wheel, take care to
tighten the shaft screw just enough to hold the
wheel in place and prevent it from spinning.
Overtightening the shaft screw may damage the
cutting-off wheel or cause it to break off the
wheel flange.
15. Use only recommended cutting-off wheels that
are suitable for 3400/min or higher and are
marked accordingly.
16. Always check the cutting-off wheel for cracks or
other signs of damage. Replace cracked or
damaged cutting-off wheels immediately.
17. Use only the cutting-off wheel flanges specified
for your machine.
18. Before you switch on, make sure that the cutting-
off wheel does not touch the machine.
19. Allow the motor to reach top speed before you
begin to cut.
20. After you have switched on, lower the cutting-off
wheel slowly until it comes into contact with the
workpiece. Then carry out a smooth cut. Avoid
causing the cutting-off wheel to jump or chatter.
This will only lead to premature wear and result
in poor cuts or a broken cutting-off wheel.
21. Workpieces are best cut when their angle in
relation to the cutting-off wheel is kept as small a
possible.
22. The number of cuts per cutting-off wheel and
their quality may vary considerably with the time
taken to make the cuts. Fast cuts may accelerate
wheel wear, but they also prevent discoloring of
the workpiece and the formation of burr. This
requires particular attention when cutting thin-
walled tubes. Do not reduce the cutting speed
toward the end of the cut, but cut right through to
the end with full power. This will help to prevent
the material from overheating and forming burr.
23. Always use the guard over cutting-off wheel.
24. Never use the machine in the vicinity of
combustible liquids or gases.
25. To avoid electric shocks, never use the machine
in damp or wet locations, and never expose it to
rain.
26. This electric tool was developed exclusively for
cutting ferrous metals. Do not try to cut wood,
brick or magnesium on this machine.
27. Do not stand in the cutting direction after a new
cutting-off wheel has been fitted. Allow the
machine to run for approximately one minute
before you begin with the cutting. If the cutting-
off wheel has an invisible fracture or defect, it will
burst in less than one minute.
28. Switch off the power supply before you carry out
any maintenance or adjustment work on the
machine.
29. Should any part of your machine be missing,
damaged or out of order in any way, or should
any electrical components fail to work correctly,
switch off the machine and pull the power plug
out of the socket-outlet. Replace the missing,
damaged or defective part before you carry on
with your work.
30. In the case of cutting-off wheels with straight-
sided flanges, be sure to observe the
recommend values for thickness and hole
diameter.
Wear safety goggles
Ꮯ
Wear ear-muffs
Wear a breathing mask
Anleitung MKS 355-1 GB SPK7 17.03.2006 11:20 Uhr Seite 6