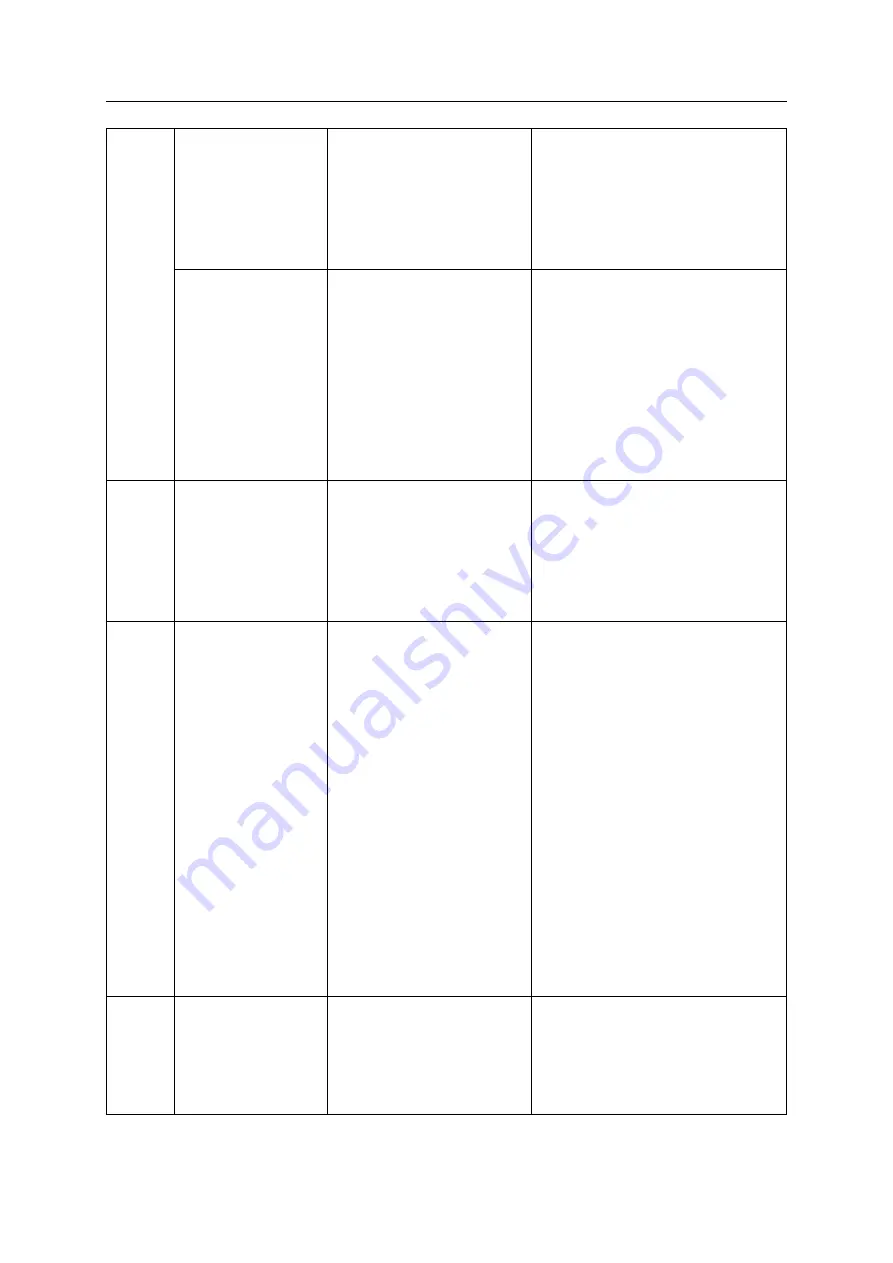
Mechanical Operation and Maintenance Manual for ER20-1100 Industrial Robot
42
operating conditions:
(1) unmatched
parameters;
(2) improper program
commands;
(3) Overload.
abnormal state, increase of the
average current value, and then
overheating.
manual. Control the load within the
allowable range.
Other faults that may
cause the motor
overheating.
(1) Abnormality in the joints
cause overload and overheating of
the motor.
(2) motor failure
(1) Check the joints of the robot whose
motor is overheated, including external
interference and damage of internal
components. If abnormality is detected,
contact our after-sales service department
for repair and replacement;
(2) Change the motor, if overheating is
eliminated, it means that the motor is in
failure.
Joints
cannot
be
locked
The robot joints fail to
be locked, so the robot
arms cannot stay at the
designated position, and
will be dropped by the
influence of gravity.
(1) Wear or circuit faults will
both cause invalid brake of the
motor.
(2) The sealing fails and the
lubricant is leaked into the motor
brake, leading to the brake failure.
(1) If only the motor fails, replace it;
(2) If the lubricant is leaked into the motor
which causes the brake failure, the cause of
sealing failure needs to be found and solved
before the replacement of the motor.
Oil
leakage
Oil leakage of robot
joints.
(1) Collision or long-term
overload cause the abnormality of
the joint components, such as
casting damage, worn O-ring, oil
seal damage, etc;
(2) If the robot has been
disassembled and reassembled,
the O-ring assembly may be
abnormal;
(3) If the joints operate in harsh
environment without proper
protection, the dust would enter in
and damage the oil seal;
(4) It also would cause oil leakage
that the oil port plug screw is
loosened.
(1) Check whether the relevant parts are
normal. If not, replace them in time.
(2) Check for ensuring that the O-ring is
properly assembled;
(3) In case of harsh working environment,
take necessary preventive measures to
protect the robot body;
(4) Check the plug screws at the oil port
and make sure that it is tightened.
Deviatio
n from
the
position
appointe
The repositioning
accuracy of robot is over
the allowable value.
(1) Abnormal connection of the
robot body or screws loosening
would both affect the positioning
accuracy;
(2) Collision or long-term
(1) Tighten the screws and check the joint
connection;
(2) Adjust and recover the deviated joint
positions. Replace the damaged
components in time.