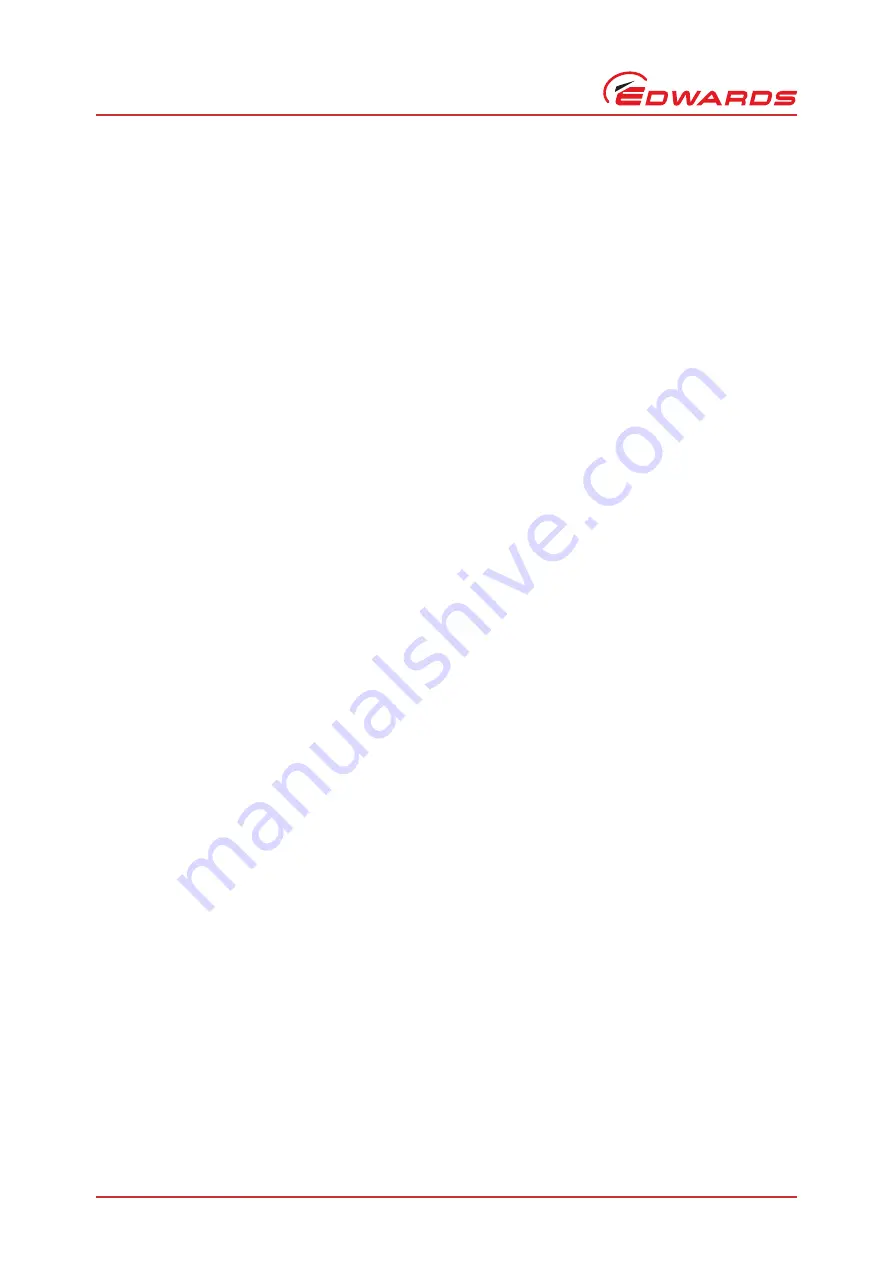
B800-00-880 Issue A
Page 4
© Edwards Limited 2009. All rights reserved.
Edwards and the Edwards logo are trademarks of Edwards Limited.
Introduction
If your application does not require the pump to be running at maximum speed at all times, you can use the Standby
speed feature rather than switching the pump off. This feature can be used for vacuum system tuning or as a system
power saving option.
The Standby speed is a user-selectable value (refer to
).
1.4.3
Timer
When the pump is started, an internal timer is automatically started within the drive electronics. The default timer
setting is 8 minutes. If the pump fails to reach 50% of full rotational speed within the timeout period, the controller
will signal a Fail and will decelerate the pump to rest. This feature prevents the controller from driving the pump at
maximum power for a long time. The pump may fail to reach 50% speed if the gas load is too high (for example if
there is a leak in the system), if the backing pump fails, or if the pump is too hot.
The timeout period is a user-selectable feature (refer to
), so if your application requires the pump to
ramp up slowly, you can extend the timeout period. The Timer is permanently enabled for ramp-up.
The Timer has an additional function: if the pump rotational speed drops below 50% full speed for any reason, you
may wish to allow the pump time to recover rather than trigger a Fail condition. The Timer starts as soon as the speed
drops to below 50% full speed. If, during the timeout period, the pump recovers to above 50% full speed then the
Timer will be reset. If the pump rotational speed fails to recover by the end of the timeout period, the controller
will trigger a Fail condition and will decelerate the pump to rest. When you receive the pump, the Timer function
will be enabled, however you can disable it if you wish to. With the Timer disabled, the pump will Fail and decelerate
to rest as soon as pump rotational speed falls below 50%.
1.4.4
Analogue output
The pump controller produces an analogue output that allows you to monitor four different system parameters:
Measured pump rotational speed (default condition)
Measured motor power
Measured motor temperature
Measured controller temperature
The analogue output signal ranges from 0 to 10 V and is directly proportional to the system parameter (refer to
Connect the analogue output to a suitable meter or indicator to display the appropriate system parameter or connect
to your control equipment (for example, to operate other components in the pumping system at preset values).
You can only monitor one system parameter at a time using the analogue output. However, it is easy to configure the
controller to monitor a different system parameter (refer to
1.4.5
Automatic vent options
An Edwards TAV vent valve can be connected directly to the nEXT pump’s controller. The controller is capable of
providing a number of different venting options.
The drive electronics can control the rate of venting. Using this feature the pump can be vented from full rotational
speed in a controlled manner that will not damage the pump bearings. Once the pump rotational speed has dropped
to below 50% of maximum speed, it is safe to hard vent (open the vent valve fully.)
There are many venting options available to you, such as:
Hard vent when rotational speed drops below 50%
Controlled vent when above 50% speed and hard vent below 50% speed
Hard vent immediately through a suitable restrictor
Summary of Contents for nEXT240
Page 2: ......