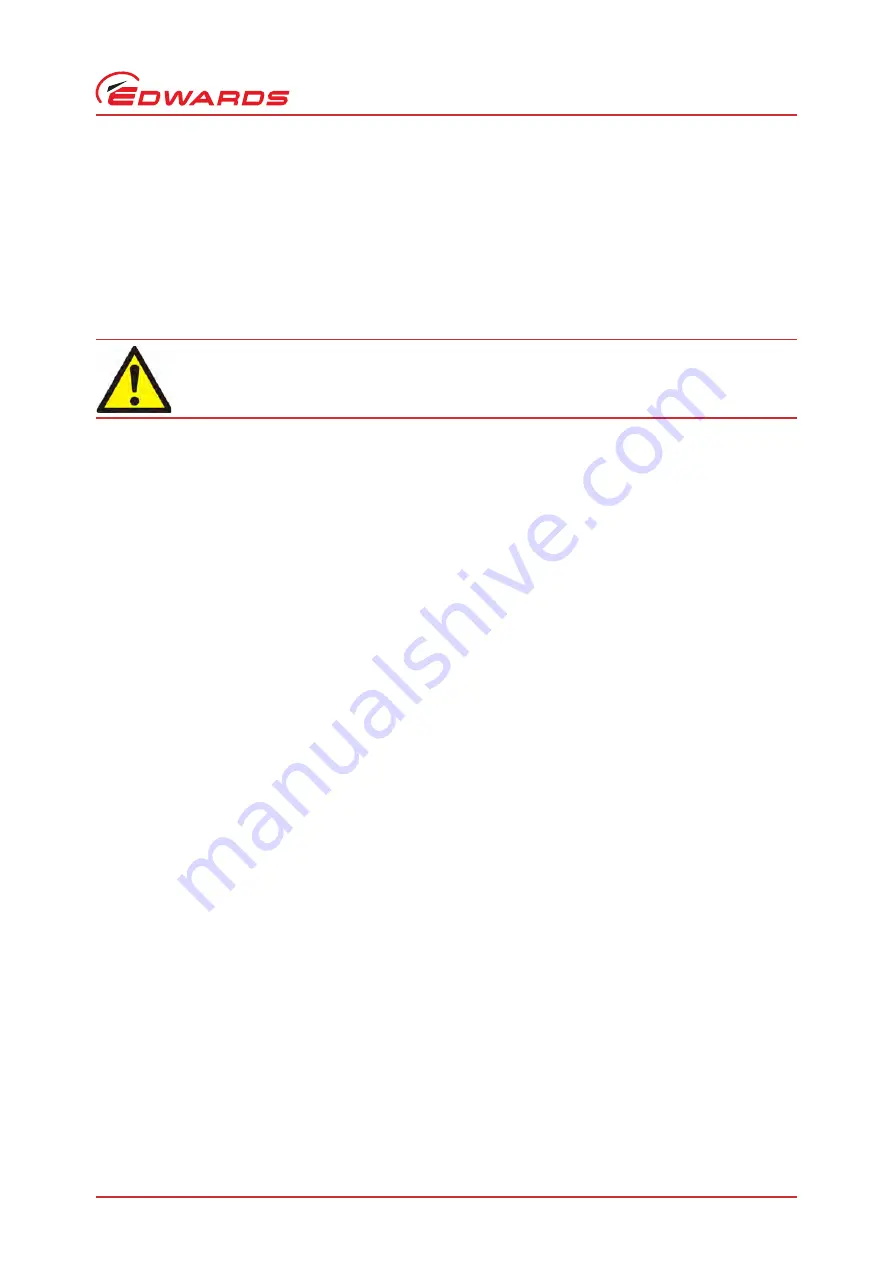
© Edwards Limited 2007. All rights reserved.
Page 23
Edwards and the Edwards logo are trade marks of Edwards Limited.
Operation
A652–07–880 Issue C
4
Operation
Note:
At high inlet pressures (above 200 mbar, 2 x 10
4
Pa), the gas ballast oil return assembly will not work
correctly. If you want to return oil to the pump when the pump is operated at continuous high inlet
pressures, contact your supplier or Edwards for advice.
4.1
Start-up procedure
If the oil is contaminated, or if the pump temperature is below 12 °C, or if the electrical supply voltage is more than
10% below the lowest voltage specified on the voltage indicator (
, item 4), the pump may operate at a
reduced speed for a few minutes. If the pump continues to operate at reduced speed, the motor thermal overload
device will open and stop the pump. When the motor has cooled, the thermal overload device will reset automatically
and the pump will restart.
1. Check that the pump oil-level is between the MAX and MIN marks on the bezel of the oil-level sight-glass; if it is
not, refer to
.
2. Use the on/off switch (
, item 12) to switch on the electrical supply to the pump.
4.2
To achieve ultimate vacuum/pump condensable vapours
If the E-LAB 2 does not achieve the performance specified in
, make sure that this is not due to your system
design before you contact your supplier or Edwards for advice. In particular, the vapour pressure of all materials used
in your vacuum system (including pump oil, see below) must be much lower than the specified ultimate vacuum of
the pump. Refer to
for a list of possible causes for failure to achieve the specified performance; note
however that the most common causes are:
z
Your pressure measurement technique or gauge head is unsuitable or the gauge head is faulty.
z
You have used an oil other than the recommended oil, and the vapour pressure of the oil is higher than the
specified ultimate vacuum of the pump.
Use the following procedure to achieve ultimate vacuum:
1. Isolate the E-LAB 2 from your vacuum system and operate the E-LAB 2 for at least 1 hour (or overnight) to
thoroughly purge the oil of contaminants.
2. Open the vacuum system isolation-valve and pump down to ultimate vacuum.
After you have pumped condensable vapours, you can (if necessary) decontaminate the oil: use the procedure in
WARNING
Ensure that your system design does not allow the exhaust pipeline to be blocked.
Summary of Contents for A652-07-903
Page 3: ......