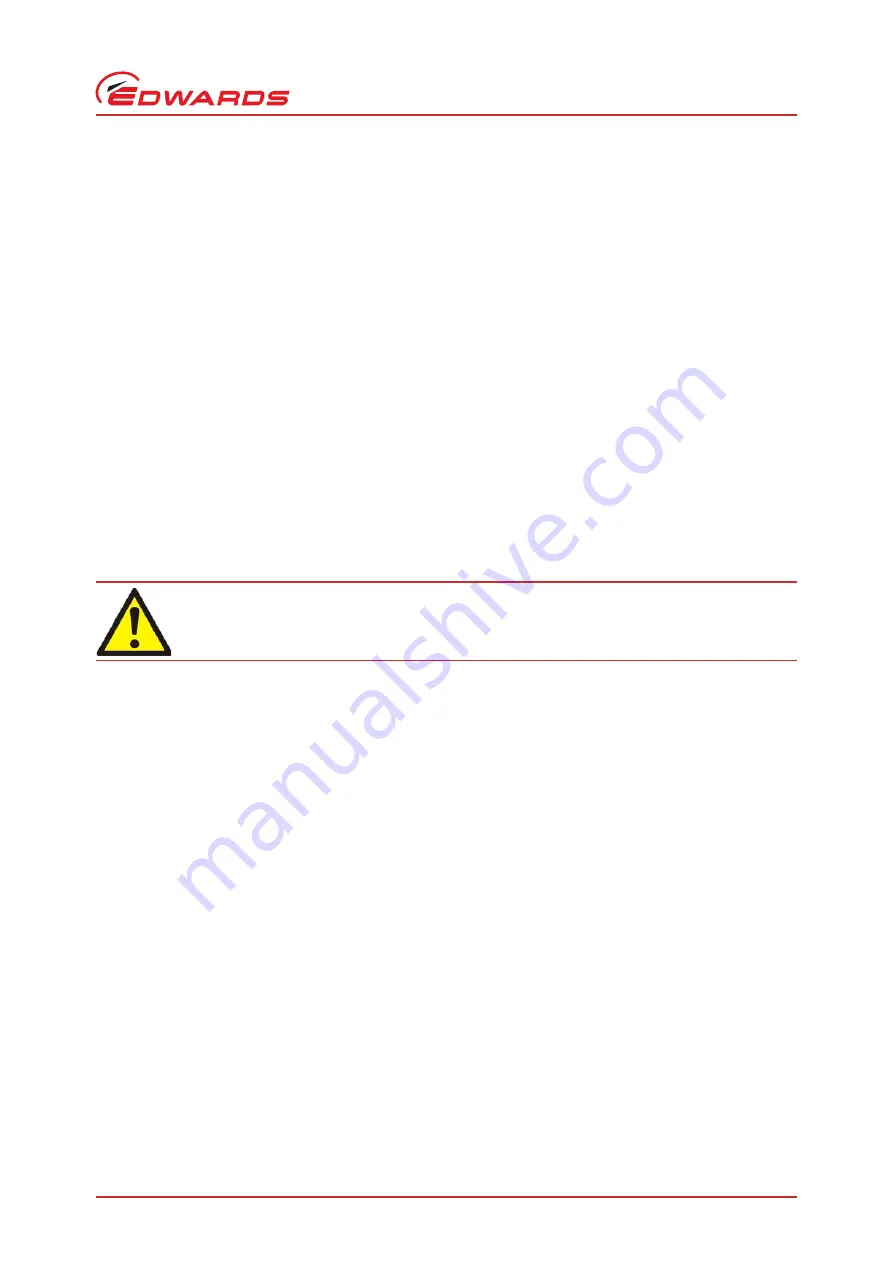
© Edwards Limited 2014. All rights reserved.
Page 17
Edwards and the Edwards logo are trademarks of Edwards Limited.
Operation
A366-04-880 Issue A
4
Operation
4.1
Gas-ballast control
Use the gas-ballast control (
, item 1) to change the amount of air (or inert gas) introduced into the
low-vacuum stage of the pump. Use of the gas-ballast will prevent the condensation of vapours in the pump. The
condensed vapours would contaminate the oil.
Turn the gas-ballast control fully clockwise:
to achieve ultimate vacuum
to pump dry gases.
Turn the gas-ballast control anti-clockwise to open. Use the gas-ballast control fully open:
to pump high concentrations of condensable vapour
to decontaminate the oil.
When you operate the pump with the gas-ballast control open, there is an increased rate of oil loss from the pump.
4.2
Start-up procedure
If the oil is contaminated, or if the pump temperature is below 13°C, or if the supply voltage is more than 10% below
the lowest voltage specified for the motor, the pump may operate at reduced speed for a few minutes.
1. Switch on the cooling water supply to the pump.
2. Switch on the electrical supply to the pump.
3. Check that the oil-level in the sight-glass drops slightly (3 to 5 mm) after start-up. This shows that the pump has
primed with oil.
4. If the pump fails to prime, operate the pump with the inlet open to atmosphere for approximately 30 seconds.
Then isolate the inlet and check that the oil-level drops 3-5 mm.
5. If you want to achieve ultimate vacuum, to pump condensable vapours or to decontaminate the pump oil, refer
to the procedures in
respectively. Otherwise, open the vacuum system isolation-valve.
4.3
To achieve ultimate vacuum
If the pump does not achieve the performance specified in
, make sure that this is not due to your system
design before you contact your supplier or Edwards for advice. In particular, the vapour pressure of all materials used
in your vacuum system, including pump oil, must be much lower than the specified ultimate vacuum of the pump.
Refer to
for a list of possible causes for failure to achieve the specified performance. The most
common causes are:
Your pressure measurement technique or gauge head is unsuitable or the gauge head is faulty
You have used an oil other than the recommended oil, and the vapour pressure of the oil is higher than the
specified ultimate vacuum of the pump.
WARNING
Do not block the pump outlet or allow the outlet pressure to rise above 1.5 bar absolute. If you do,
the oil box may fracture: this may cause injury to people nearby.