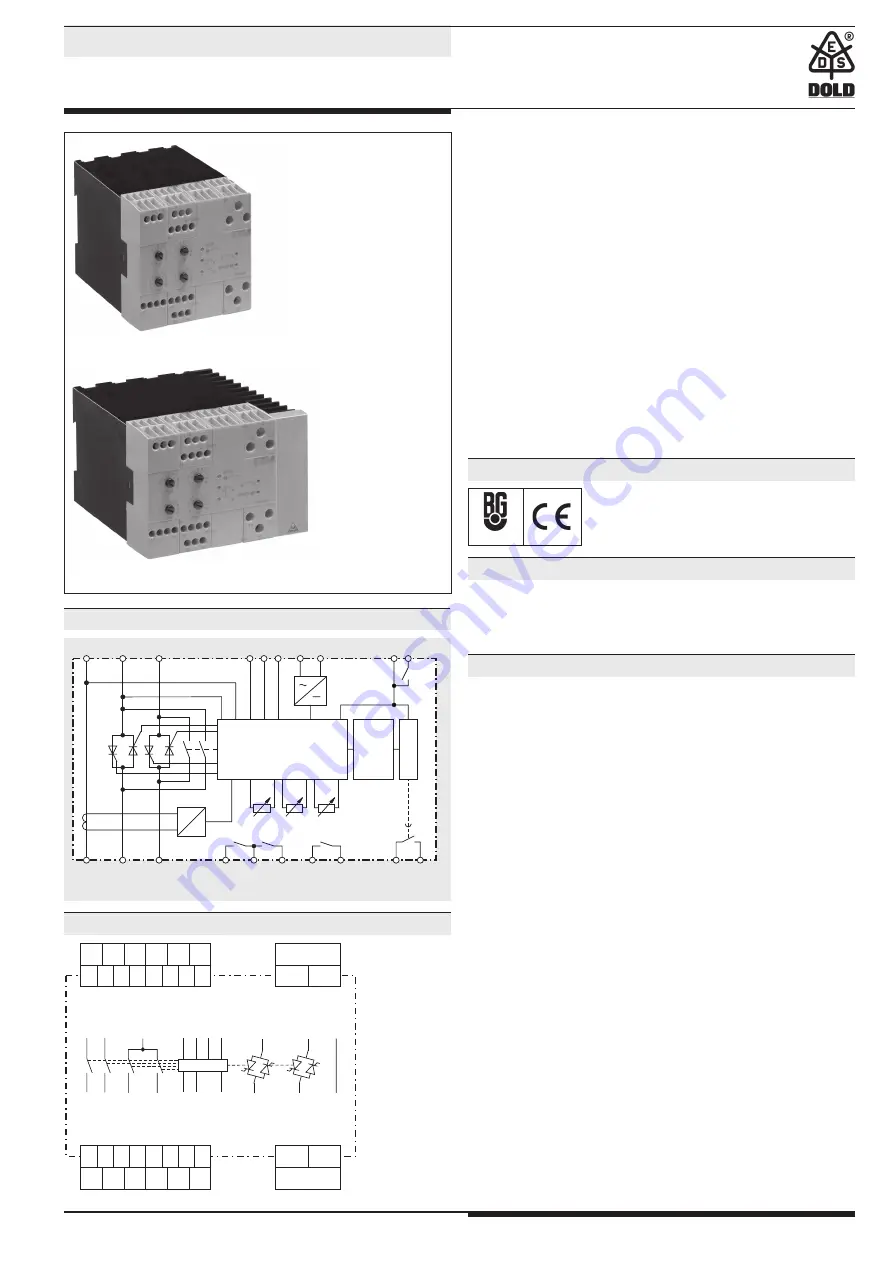
1
BL 9228 / 06.12.07 e
Power Electronics
•
According to IEC/EN 60 947-4-2, prEN 1870-1, GS-HO-01
•
2-phase motor control
•
For motors up to 15 kW bei 3 AC 400 V
•
Separate settings for start and brake time, as well as starting
and braking torque
•
Control input and relay output for emergency stop according to
safety category 1, EN 954-1
•
No braking contactor necessary
•
With automatic standstill detection
•
This brake system fullfills the requirements of category 2
according to EN 954-1 of "Recommandation for Use"
(CNB/M/01.051IR/E), prEN 1870-1, GS-HO-01
•
Safe separation of the motor from the mains after fault or
brakefunction via external contactor, category 1 according to
EN 954-1
•
Maintenance- and wearfree
•
Auxiliary voltages 230 V and 400 V
•
Monitors undervoltage and phase sequence
•
3 relay outputs for indicaiton of status and fault with LED-indication
•
With input to detect motor temperature
•
BL 9228 up to 7.5 kW: 90 mm width
BL 9228 up to 15 kW: 112.5 mm width
Softstarter with DC-Brake BL 9228
ministart
All technical data in this list relate to the state at the moment of edition. We reserve the right
for technical improvements and changes at any time.
A 0249781
Approvals and marking
Applications
•
Motor with gear, belt or chain drive
•
Fans, pumps, conveyor systems, compressors
•
Woodworking machines, centrifuges
•
Packing machines, door-drives
Block diagram
BL 9228 up to 15 kW
BL 9228 up to 7.5 kW
L1
L2
L3
A1
P1 P2 P3
A2
X1 X2
T1
T2
T3
M5667
M on
electronics
supply
t on
I Br
micro control
safety
monitoring
33
34
Tv
14
43
13
44
24
I
U
HBG
Circuit diagram
M8464_c
33
34
P1
P2
P3
13
A1
X1
24
A2
X2
L1
T1
L3
T3
14
43
44
L2
T2
L2
33
43
34
44
A1
T2
L3
L1
T3
T1
X1 X2 P1 P2
A2
P3
13
24
14
Softstarters are electronic devices designed to enable 1-phase or
3-phase induction motors to start smoothly. The devices slowly
ramps up the current on two phases, therefore allowing the motor
torque to build up slowly. This reduces the mechanical stress on the
machine and prevents damage to conveyed material.
These features allow cost saving constructions of mechanical gear.
A special monitoring allows the application in systems of safety
category 2.
Start/Stop switch
When the motor is on full speed after the starting with start switch the
semiconductors are bridged with internal relay contacts to prevent
internal power losses and heat built up.
When stopping the motor via start switch braking is started. The
braking current flows until detection of the stillstand through the motor
windings. If the brake function takes longer than 10 sec, the monitoring
relay 1 provides a signal. After 15 sec the brake function will be finished
and the motor will be separated from the mains via contactor K1.
Monitoring relay 1 (contact 13-14)
Relay 1 is energised if the brake function takes longer than 10 sec. By
restarting of the device this relay is de-energised. However, if the
brake function has been longer than 10 sec for the third time, the device
is set into an error mode. The red LED flashes code 9. This fault can
only be reset by switching on and off the power supply.
Monitoring relay 2 (contact 13-24)
This relay energises as soon as the unit is ready for operation after
connecting it to power. If any error occurs the monitoring relay 2 will
be de-energised immediately. The power output will be switched off.
Monitoring relay 3 (contact 33-34)
The relay is energised after activating the on-button and is de-
energised after indication of the motor standstill at the end of braking.
If standstill is not detected, the relay is de-energised after pushing the
off-button and elapse of a safety time. The relay is operating the motor
contactor. It is immediately de-energised by any fault indication.
Function