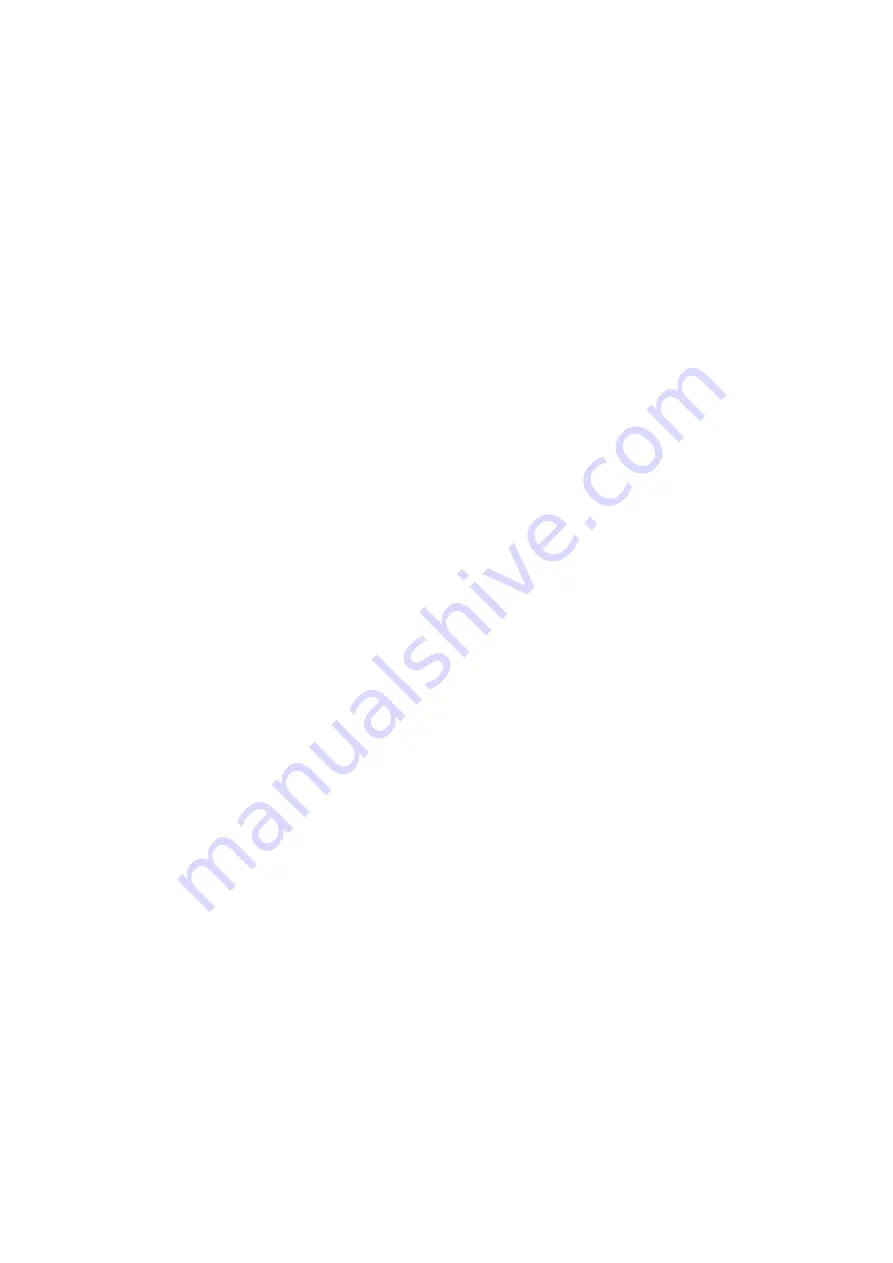
22
the next scan.
5.
Press and hold the blue button to reset the encoder count value of the scan axis position to
zero.
6.
Press the red pause/resume button to resume the next scan then move the scanner forward to
capture data.
7.
Repeat steps 2-5 until grid scan is complete then save the data file.
Bi-direction scanning steps using the R-Scan Array scanner:
1.
Press play and move scanner forward to capture data for the first scan.
2.
When the target distance has been reached. press the blue indexing button to increment the
software to the next scan.
3.
Slide the scanner across perpendicular to next scan path. Do not slide diagonally.
4.
Move the scanner backwards to capture data for the next scan.
5.
Repeat steps 2-4 until grid scan is complete then save the data file.
Automatic mode
To prepare and connect the system together for an automated inspection:
1.
For an automatic mode inspection fit the low friction wheels to the scanner.
2.
Disengage the wheel brake lever.
3.
Attach R-Scan Array scanner to the RMS scanning head using the supplied quick release
bracket.
4.
Follow the setup instructions found in RMS-PA User guide.