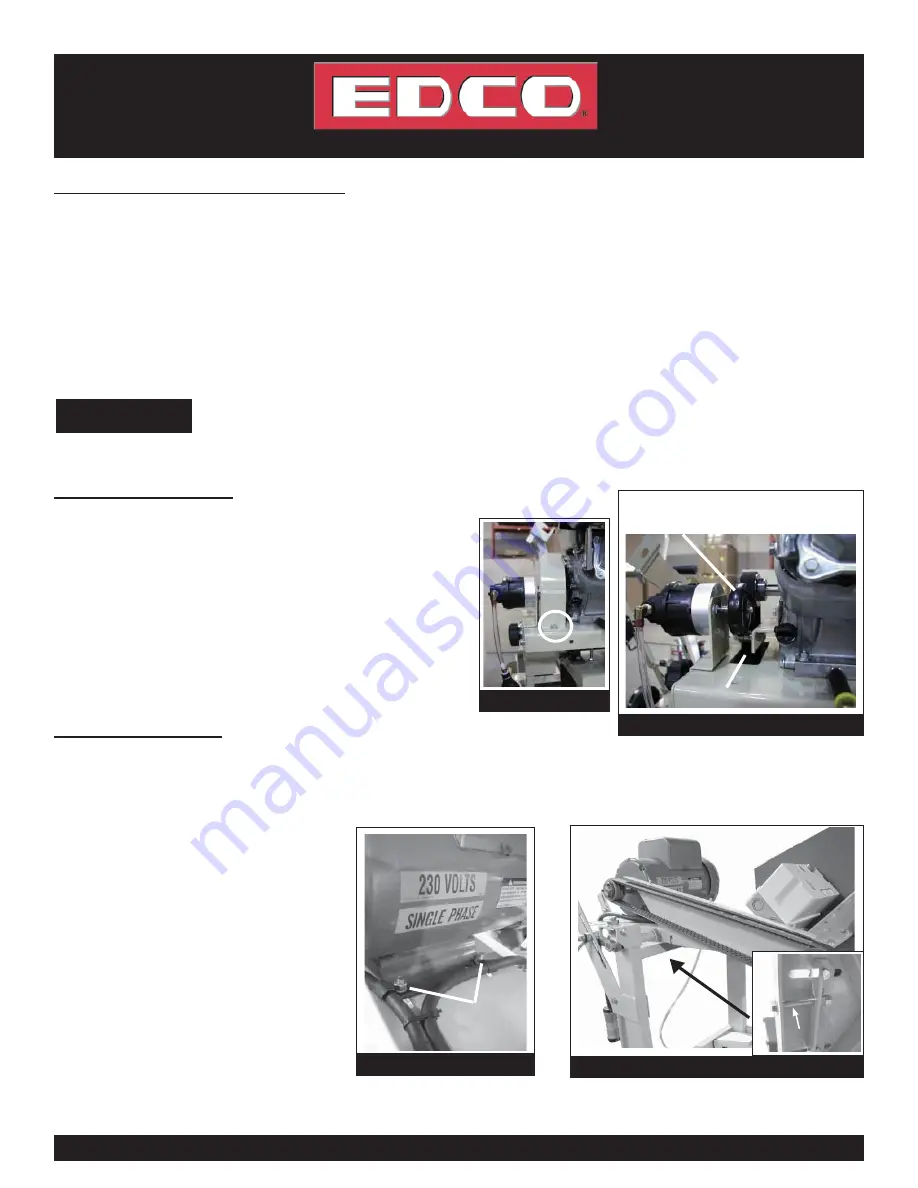
Page 13
E-BB14E&BB14G-I-0416
E-SPTS-I-0809
800-638-3326 • edcoinc.com • [email protected]
EQUIPMENT DEVELOPMENT CO., INC.
Belt Adjustment and Replacement:
•
Periodically check belt(s) for damage, same type and are at the proper tension. Do not mix belts. Slipping belt(s) will
overheat causing the cutting speed to be limited and shorten the life of the belts. Over-tensioned belts will shorten the
life of the belt(s) and bearings.
•
On new equipment and after installing new belt(s) of the same type, be certain to re-tension the belt(s) after the
fi rst 4 hours of use. New belts are stiff and require a break in period. Belts that are loose could slip and/or over-
heat.
•
Damaged, stretched or excessively worn belt(s) should be replaced with a new complete set of belt(s) of the same
type. Do not mix belts.
•
Belt(s) must be replaced with the same type.
•
Blade must be realigned every time the belt(s) are tensioned, gas model only.
Important!
On Electric Models:
NOTE: Due to machine improvements
pictures may not show your particular
machine. The instructions however are the
same.
•
Loosen motor mounts (4)
(
Figure 21
)
•
Loosen jacking bolt until belts
slide off sheave. (
Figure 22
)
•
Replace with a new complete
set of belts of same type. Do
not mix belt types.
•
Adjust jacking bolt to tension belts.
•
Square motor to frame.
•
Retighten motor mount bolts.
On Gasoline Models:
•
Access belt from back of machine.
•
Remove two (2) cap screws from both sides of the
belt guard as circled in photo to right (
Figure 19)
Figure 19)
.
Lift off belt cover, Water pump drive wheel and belt
are now accessible.
•
To change drive belt (
Figure 20
), loosen engine mount bolts
and belt tensioner, tilt engine torward water pump
until belt can be removed.
Figure 19
Water
Pump
Wheel
Drive Belt
Drive Belt
Figure 20
Motor
Mount
Bolts
Figure 21
Jacking
Bolt
Figure 22