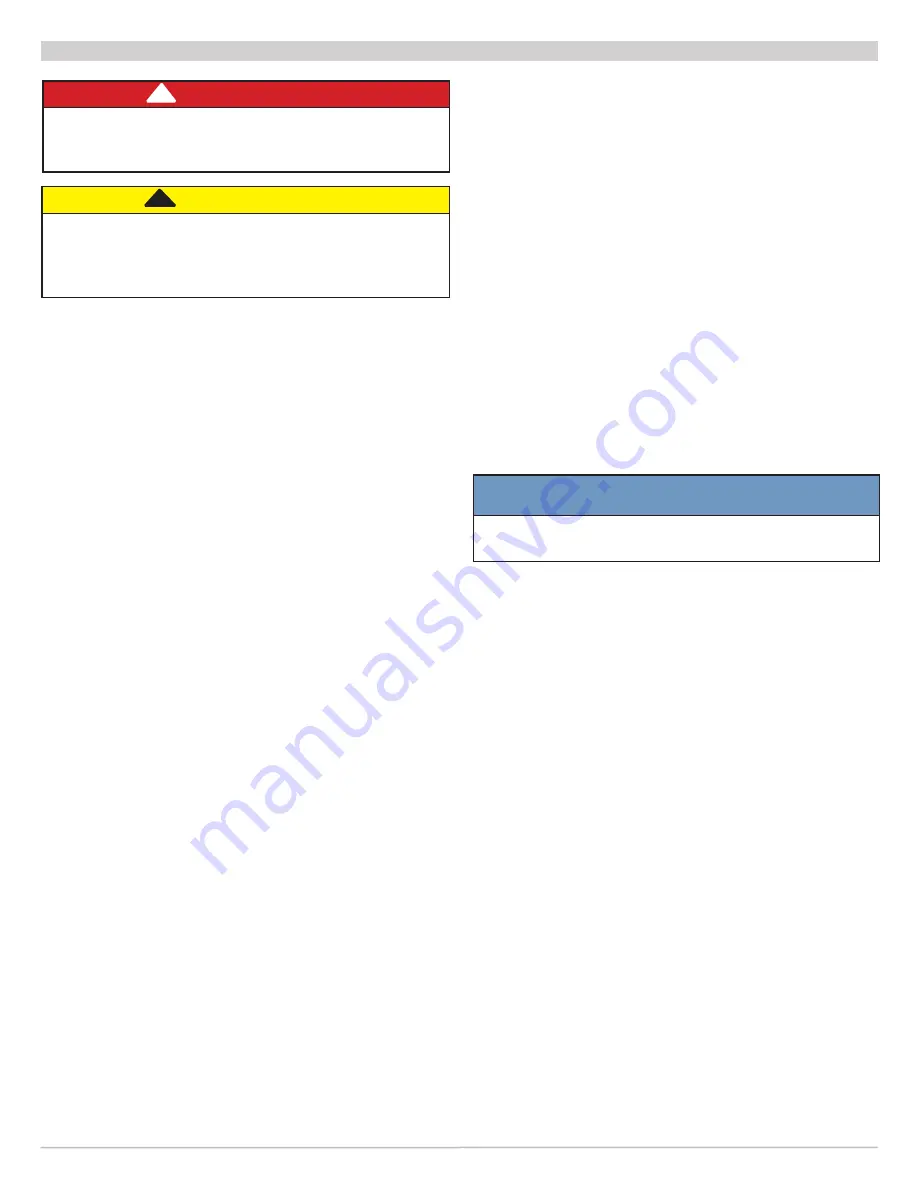
INSTALLATION PREPARATION
Verify existing wall sleeve/enclosure:
1.
RetroAire PTAC/PTHP's are to be used with metal wall
sleeves.
2.
Existing front panels must be secured by screws that
prevent contact with all parts.
3.
Minor dimensions of openings must not exceed ½ inch
(12.5mm).
4.
Indoor air discharge grill must have dimensions not
less than 26” x 4”. Grill must separate top surface of
chassis from top surface of discharge grill by minimum
of 1 in (25.4mm).
5.
For all models, outdoor openings must prevent contact
of all moving parts by means of louvers or grills, with
minor dimension not exceeding 1 in (25.4mm).
DANGER
Electrical shock hazard — Verify power to existing
unit is disconnected before removing. Failure to do
so will result in death or serious injury.
!
CAUTION
Moving parts can cause personal injury. Avoid
contact with moving parts when testing or servicing
the unit. Failure to follow these instructions could
result in minor or moderate injury.
!
Electrical Power Connection
All wiring shall conform to requirements of authority
having jurisdiction or in absence of such requirements:
• United States
National Electrical Code, ANSI/NFPA 70
UL 1995 4th Addition.
• Canada
CSA C22.1 Canadian Electrical Code Part 1.
Installer is responsible for ensuring units are installed in
accordance with all applicable national and local codes.
UNITS RATED 208/230V — RetroAire unit is wired for 230v
primary voltage from manufacture.
Transformer must be rewired by installer if job site voltage
is 208V. Change transformer tap from orange to red. See
wiring diagram for details.
1.
Verify RetroAire unit rating plate for circuit ampacity
and required breaker or fuse size.
2.
Verify existing breaker or fuse is correct size.
A. Replace breaker or fuse if incorrectly sized.
B. Breakers must be type HACR only.
3.
Cord connected units — verify wall outlet is correct
rating. Outlet's blade configuration must match that of
cord supplied with RetroAire unit.
4.
Hard-wired units — verify power wiring is correctly
sized. Inspect existing wiring for deficiencies, such as
cuts or frayed wires. Replace any deficient wiring if
found.
5.
Each unit must have separate branch circuit protected
by fuse or breaker. Refer to unit rating plate for proper
wire and breaker or fuse size. Use of extension cords is
prohibited.
6.
DO NOT connect RetroAire unit to circuit with
incorrectly sized overcurrent protection device.
7.
All cord-connected 265-volt units must be plugged into
receptacles within unit subbase or chassis.
8.
Open power supply disconnect switch. Secure in open
position during installation. Attach sign stating, "DO
NOT TURN ON."
9.
On a plug and receptacle connection, unplug existing
unit at the wall outlet. DO NOT plug in the new unit
until installation is complete and start-up checklist has
been completed.
Remove Old Chassis
1.
Disconnect power or unplug cord before proceeding.
2.
Remove front of the existing room enclosure to expose
old chassis.
3.
Loosen any tie-down bolts or screws. Remove old
chassis.
NOTICE
Dispose of old chassis following existing state and
federal regulations.
4.
Inspect wall sleeve/cabinet for any rust, holes, or
damage.
A. Clean wall sleeve of any dirt.
B. Repair any damage.
C. Ensure proper drainage of condensate or rainwater
to exterior of building.
5.
Remove or repair old weather seals. Note location for
installation of any new seals.
6.
Check wall sleeve/cabinet to ensure all drain holes are
open and:
A. Wall sleeve/enclosure is level left to right
B. Back is pitched to outside by ½ in (12.5mm)
maximum.
7.
Before installing new chassis, inspect outdoor louver
for minimum free area of 70% and remove any
obstructions. Obstructions restrict air flow over
condenser coil and may cause damage to the chassis.
8.
Follow the installation instructions on the following
pages.
9.
DO NOT connect power to the unit or plug in the cord
until instructions in this manual have been completed.
The Right Fit for Comfort
12
P/N 240010598, Rev. A [05/12/2014
]