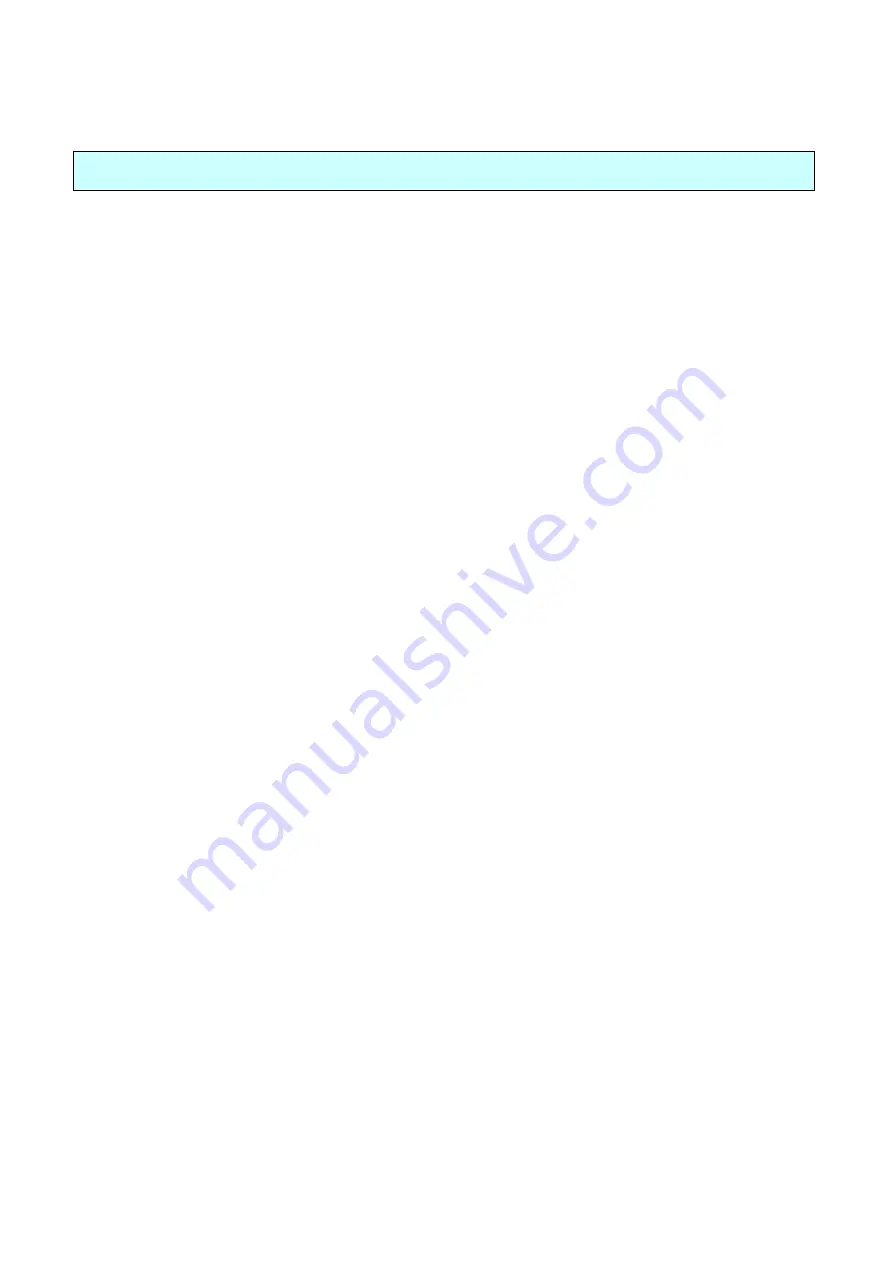
23
This section is supplied for reference only, if your system is a Rental, contact EcoWater technical
service personnel before attempting any complex troubleshooting. This section only includes the
most common types of failures. Some failures may not be listed here and require you to contact
EcoWater’s technical service personnel for aid in troubleshooting.
Gauge Problems-
If the gauge is reading high or low turn off all power to the device the gauge is
connected to and allow the pressure to stabilize. The gauge should return to 0 psi. If it does not, open the
vent at the top of the gauge and allow it to return to 0 psi (this may take several minutes). If the pressure
still remains above or below 0 psi, replace the gauge.
Low Pump (s) Pressures-
Verify that the gauges are operating and return to 0 psi as the pump is stopped.
Verify the strainer basket is clean. You will have to verify the sides of the basket are clean, and not just
the bottom. If the pressure remains low, verify that the isolation valves around the pump as well as the
towers are open. If the pressure remains low, verify that no blockage exists within the tubing to the
gauge. If the pressure remains low, rebuild or replace the pump or motor.
High Pump Pressures-
Verify that the gauges are operating and return to 0 psi as the pump is stopped.
Verify the isolation valves at the unit as well as the towers are open. High pump pressures, if not caused
by a defective gauge, are normally caused by an obstruction to flow. If all the valves are open, the
obstruction will have to be located and removed.
Non-Active Pump-
Verify that the Motor Controller is applying power to the pump. If the Motor
Controller is not applying power, see Motor Controller Failure. If the power is available to the motor,
verify all electrical connections at the motor. If no failures are noted, replace motor.
Motor Controller Failure-
Verify all fuses are intact and pass the continuity test, replace any failed
fuses. If fuses continue to fail, replace the pump motor. If fuses are complete, verify that the Thermal
Overload is set to 1.25 times the maximum motor amperage. The Thermal Overload has a reset button,
once changes are made, make sure to reset the Thermal Overload. If the Controller still will not function,
replace the Controller.
O-Ring Leaks or Failure-
Replace defective O-Ring, and lubricate with appropriate silicone lubricant.
CHC will supply this lubricant if requested.
Plumbing Leaks or Failure-
Contact the appropriate personnel to make corrections to plumbing.
Valve Leaks or Failure
- Contact the appropriate EcoWater personnel to make corrections to plumbing.
Other Electrical Failures-
Contact the appropriate EcoWater personnel to make corrections.
Actuator Failure-
Most actuator failures are caused by the failure of the actuated valve. As the actuator
is removed for servicing, make sure the valve is easily opened and closed. Some valves can become to
difficult to move by the actuator and can cause actuator failure. Verify that the fuse or breaker controlling
the timer circuit is still functional, If the fuse and/or breaker is still good, the failure could be related to the
TROUBLESHOOTING
Summary of Contents for CHC
Page 1: ...INSTALLATION SERVICE MANUAL FOR THE CHC WATER TREATMENT SYSTEM ...
Page 21: ...21 User Screen Structure E coW aterC H C CHC C H C C H C ...
Page 22: ...22 CHC CHC CHC ...
Page 26: ...26 F80 F300 Skid Equipment Views ...
Page 38: ...38 ...
Page 40: ...40 ...
Page 41: ...41 ...
Page 42: ...42 ...