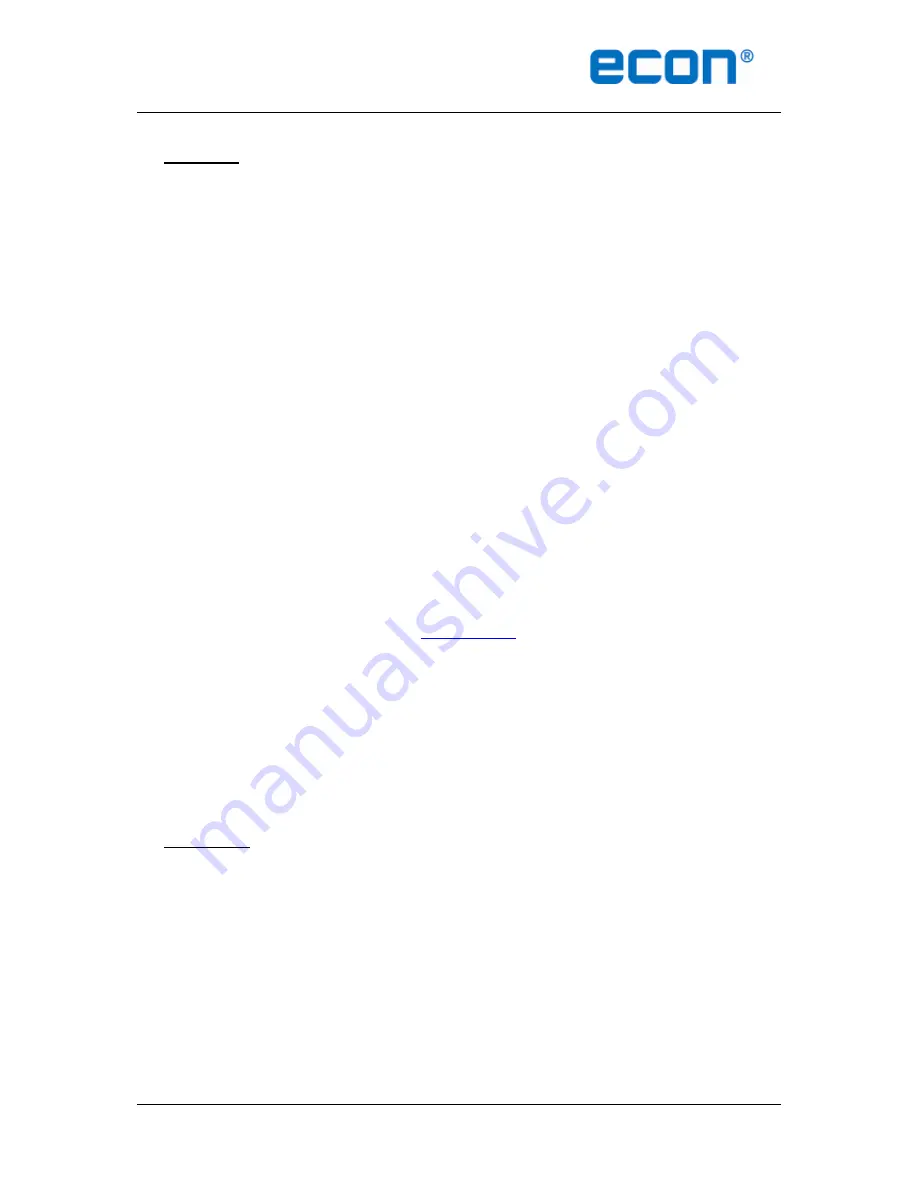
Installation & Operation Manual
Proven Quality since 1892
ECON ball valves Fig. 7422, 7442, 7522, 7542, 7622, 7642, 7722, 7742
www.eriks.com
Rev.4
Page 2
7. Installation
a. Remove the protective plastic cap on 2-threaded, BW and SW ends, and clean or flush the
valves.
b. Prior to mounting, flush and/or clean the pipeline to remove all accumulated extraneous
matters, which may damage the seats and ball surface and check if the valve has a preferred
flow direction and take this direction into account during installation.
c. Installation of threaded ends:
Use conventional sealant (e.g. Teflon) on the threads.
Apply a wrench only on the end cap of the valve for tightening. Applying a wrench on
the valve body or lever can seriously damage the valve.
d. Installation of BW and SW end valves
Tack-weld the valve on the pipe on four points on both caps, with the ball valve in
open position. Extended butt-weld end ball valves allow direct welding. For short butt-
weld or socket-weld end connections process the next steps.
Removed all body bolts except one and after losing the remaining one, the valve body
can be swung out. Secure seats from falling temporary with tape.
Finish welding both end caps on the pipe.
When cooled down, clean both end caps and body surface.
Remove temporary tape, swing the body back to the original position and replace the
bolts (if necessary). Put the valve in the open position. Tighten all nuts slightly. During
this operation it is very important to keep body and end caps perfectly parallel, thus,
preventing distortion of the end caps.
Tighten body bolts evenly. Make sure that maximum tightening torque is observed per
bolting torque data. See table B
e. Check proper operation of the valve.
f. The pipeline shall be free of tension after installation.
g. For any further information please contact the ERIKS company that has supplied the valves.
Contact information can be found on
www.eriks.com
h. Make sure the pipeline will be flushed clean prior to operation.
i. The operation of the valve consist of turning the stem (by manual or automated means) ¼ turn
(90
0
) clockwise to close, and ¼ turn counter-clockwise to open.
j. When the lever (if used) and/or stem flats or groove are in line with the pipeline, the valve is
open.
k. Besides operating by lever, Fig. 7422, 7442, 7522, 7542, 7622, 7642, 7722 and 7742 can also
be operated with an actuator, mounted on the ISO 5211 “Direct Mount” top-flange. (Please
see our catalogue to check top-flanges sizes)
l. Operating torque requirements will vary depending on the length of time between cycle, media
in the system line pressure and type of valve seat.
8. Maintenance
Long life and maintenance-free of valves can be maintained under normal working conditions and
in accordance with pressure/temperature and compatibility data chart.
Warning:
Before starting any service jobs, make sure that the medium supply to the pipeline is cut
off, pressure is decreased to ambient pressure, the pipeline is completely cleaned and
ventilated and the plant is cooled down.
Keep always personal safety precautions in mind and always use appropriate protection
e.g. clothing, masks, gloves etc.
Be alert that ball valves can trap pressurized fluid in ball cavity when closed position.
Be alert that the temperature still can be very high of low and can cause burns.