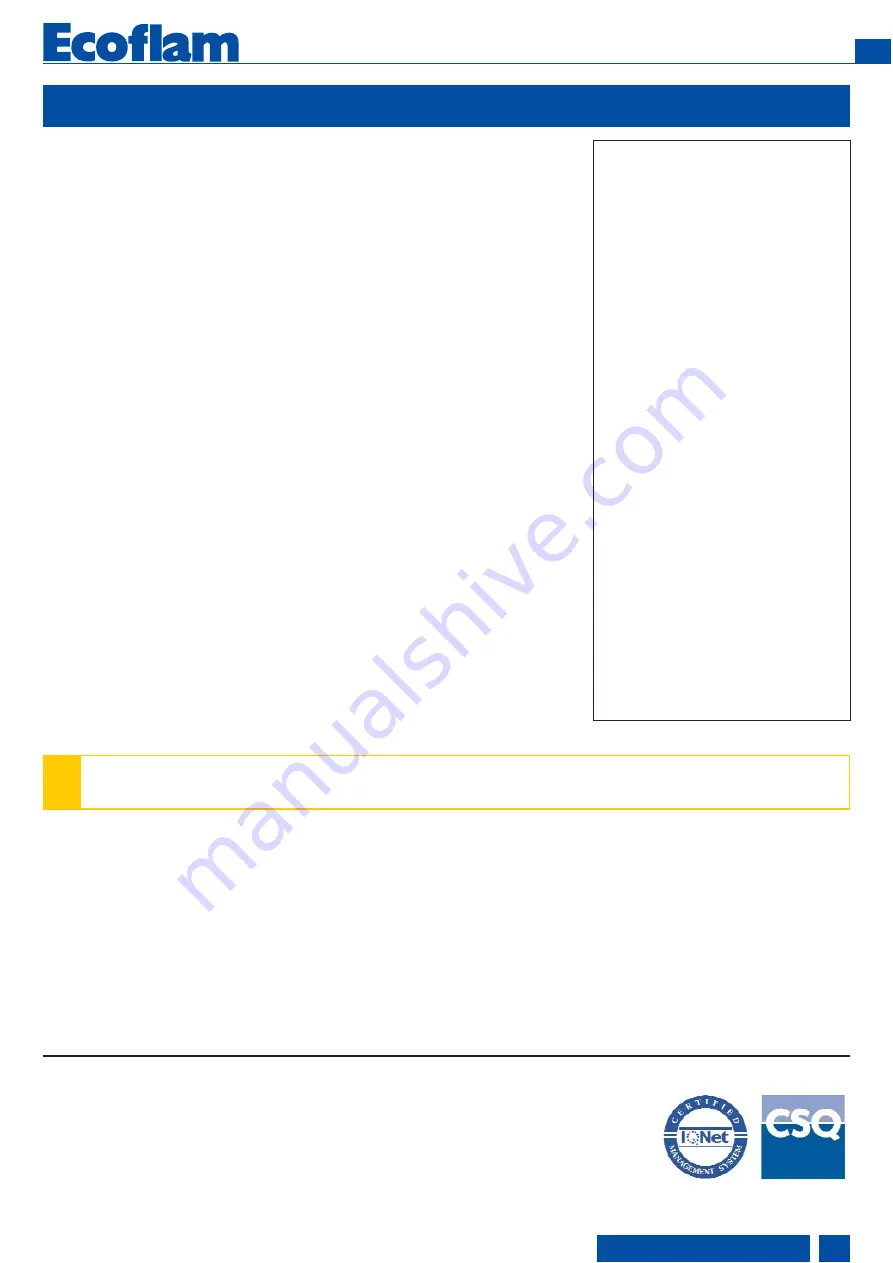
GENERAL WARNINGS - CONFORMITY DECLARATION
MULTIFLAM burners are designed for
the combustion of natural gas and heavy
oil. The design and function of the burners
meet the standard EN267 and standard
EN676. They are suitable for use with all
heat generators complying with standard
within their respective performance range.
Any other type of application requires the
approval of ECOFLAM.
Installation, start-up and maintenance
must only be carried out by authorised
specialists and all applicable guidelines
and regulations must be complied with.
BURNER DESCRIPTION
MULTFLAM burners are progressive
mechanical fully automatic monoblock
devices.
Emissions values may differ, depending on
combustion chamber dimensions,
combustion chamber load and the firing
system (three-pass boilers, boilers with
reverse firing).
PACKAGING
The burner, the gas train and all the
additional components are supplied in a
modular system of packages according to
the configuration ordered that based on
the country of installation shall follow the
applicable standards and the local rules
and code of practise.
The following standards should be
observed in order to ensure safe,
environmentally sound and energy-efficient
operation:
EN 267
Automatic forced draught burners for liquid
fuels.
EN 676
Forced-draught gas burners.
EN 60335-1, -2-102
Specification for safety of household and
similar electrical appliances, particular
requirements for gas burning appliances
GAS LINES
When installing the gas lines and gas train,
the general EN676 directives and
guidelines must be observed.
EN676 compulsory kit and accessories in
order to comply to the safety regulations.
Additional accessories and kits shall be
installed by the installer in accordance to
the local safety regulations and codes of
practise.
INSTALLATION LOCATION
The burner must not be operated in rooms
containing aggressive vapours (e.g. spray,
perchloroethylene, hydrocarbon
tetrachloride, solvent, etc.) or tending to
heavy dust formation or high air humidity.
Adequate ventilation must be provided at
the place of installation of the furnace
system to ensure a reliable supply with
combustion air.
!
BURNER SELECTION:
Type of operation and configuration must be done by professional personnel in order to grant correct working of the
burner. Installation, start-up and maintenance must be carried out by authorised specialists and all applicable guidelines and regulations
(including local safety regulations and codes of practise) must be observed.
We accept no responsibility for
damage arising from:
- inappropriate use;
- incorrect installation and/or repair on
the part of the buyer or any third party,
including the fitting of non-original parts;
- non authorised modifications made
on the burner.
Final delivery and instructions for use
The firing system installer must supply
the operator of the system with operating
and maintenance instructions on or before
final delivery. These instructions should
be displayed in a prominent location at the
point of installation of the heat generator,
They should include the address and
telephone number of the nearest customer
service centre.
Notes for the operator
The system should be inspected by a
specialist at least once a year.
Depending on the type of installation,
shorter maintenance intervals may be
necessary.
It is advisable to take out a maintenance
contract to guarantee regular servicing.
Ecoflam burners have been designed and built in compliance with all current regulations
and directives.
All burners comply to the safety and energy saving operation regulations within the standard
of their respective performance range. The quality is guaranteed by a quality and management
system certified in accordance with ISO 9001:2008.
Declaration of conformity
for dual fuel burners
We,
Ecoflam Bruciatori S.p.A.
declare under our sole responsibility
that the products:
MULTIFLAM 300.1 PR
MULTIFLAM 400.1 PR
conform to the following standards:
EN 676: 2008
EN 267: 2010
EN 60335-1: 2008
EN 60335-2-30: 2006
EN 60335-2-102: 2007
EN 55014-1: 2008 + A1: 2009
EN 55014-2: 1998 + A1: 2001 + A2: 2008
These products are built in accordance
with the following directives
2006/42/EC Machinery directive
2004/108/EC EMC directive
2006/95/EC Low voltage directive
2009/142/EC Gas appliances Directive
CE certification, when required, must be
done at installation site by the end user
Resana, 20th December 2010
M. PANIZZON
420010601100
EN
www.ecoflam-burners.com
3