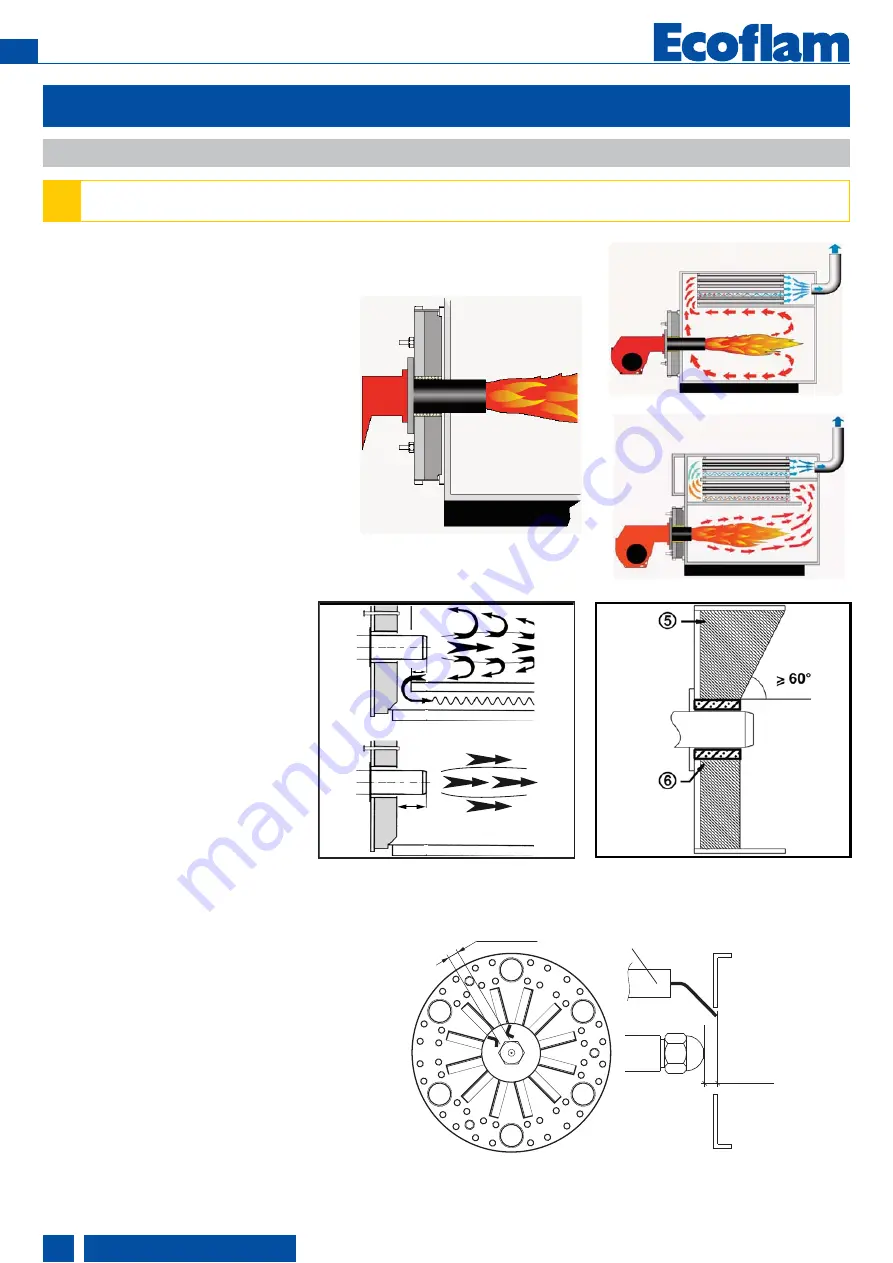
!
WARNING:
handling and moving operations must be carried out by specialised personnel.
Use the eyebolts to lift the burner in order that it will not overturn and fall down.
INSTALLATION
Fitting the burner to the boiler
Position of the electrodes nozzle installation
3 ÷ 4 mm
5 ÷ 6 mm
Ignition Electrode
BURNER LINING
Check before burner installation:
1. Depending on the type of boiler (reverse
flame or three pass) check the burner blast
tube installation depth according to the
data specified by the boiler manufacturer
or consult the burner producer.
2. From the factory the nozzle for
progressive version must be specified from
the customer according to boiler output
and combustion chamber geometry,
otherwise we will select the nozzle for the
80% capacity of the burner.
3. Check the ignition electrodes and the
nozzle on the burner head as per factory
setting (see figures).
The setting of the mixing and ignition unit
according to the boiler output will be
performed during commissioning
procedure.
4. Check that the head is preset at 50%.
420010940500
EN
www.ecoflamburners.com
12
To perform the installation of the burner
into the boiler drill the boiler plate
according to the dimension given on this
manual and place the burner towards it by
lifting and moving the burner by means of
eyebolts.
Place the gasket on the burner flange and
install the burner into the boiler by fixing
nuts into the bolts.
The space between the blast tube and the
boiler lining must be sealed with
appropriate insulating material.
Burner blast tube insertion depth and
brickwork
Unless otherwise specified by the boiler
manufacturer, heat generators without a
cooled front wall require brickwork or
insulation 5 as shown in the illustration.
The brickwork must not protrude beyond
the leading edge of the blast tube, and
should have a minimum conical angle of
60°. Gap 6 must be filled with an elastic,
non-combustible insulation material. For
boilers with reverse firing, the minimum
burner tube insertion depth A as speci fied
in the boiler manufacturer’s instructions
must be observed.
On boilers the blast tube insertion depth
should be observed as per the boiler
manufacturer's instructions.
Reverse flame boiler :
A = 50-100 mm.
Three pass boilers :
A1 = 50-100 mm.
Exhaust system
To avoid unfavourable noise emissions,
right-angled connectors should not be
used on the flue gas side of the boiler.
A
A1
Summary of Contents for MULTIFAM 500.1 PRE
Page 33: ...33 www ecoflam burners com EN 420010940500 APPENDIX Fluidics nozzle chart...
Page 34: ...34 www ecoflam burners com EN 420010940500 APPENDIX Fluidics nozzle chart...
Page 35: ...35 www ecoflam burners com EN 420010940500 APPENDIX Fluidics nozzle chart...
Page 40: ...40 www ecoflam burners com EN 420010940500 APPENDIX Electrical diagrams...
Page 41: ...41 www ecoflam burners com EN 420010940500 APPENDIX Electrical diagrams...
Page 43: ...43 www ecoflam burners com EN 420010940500...