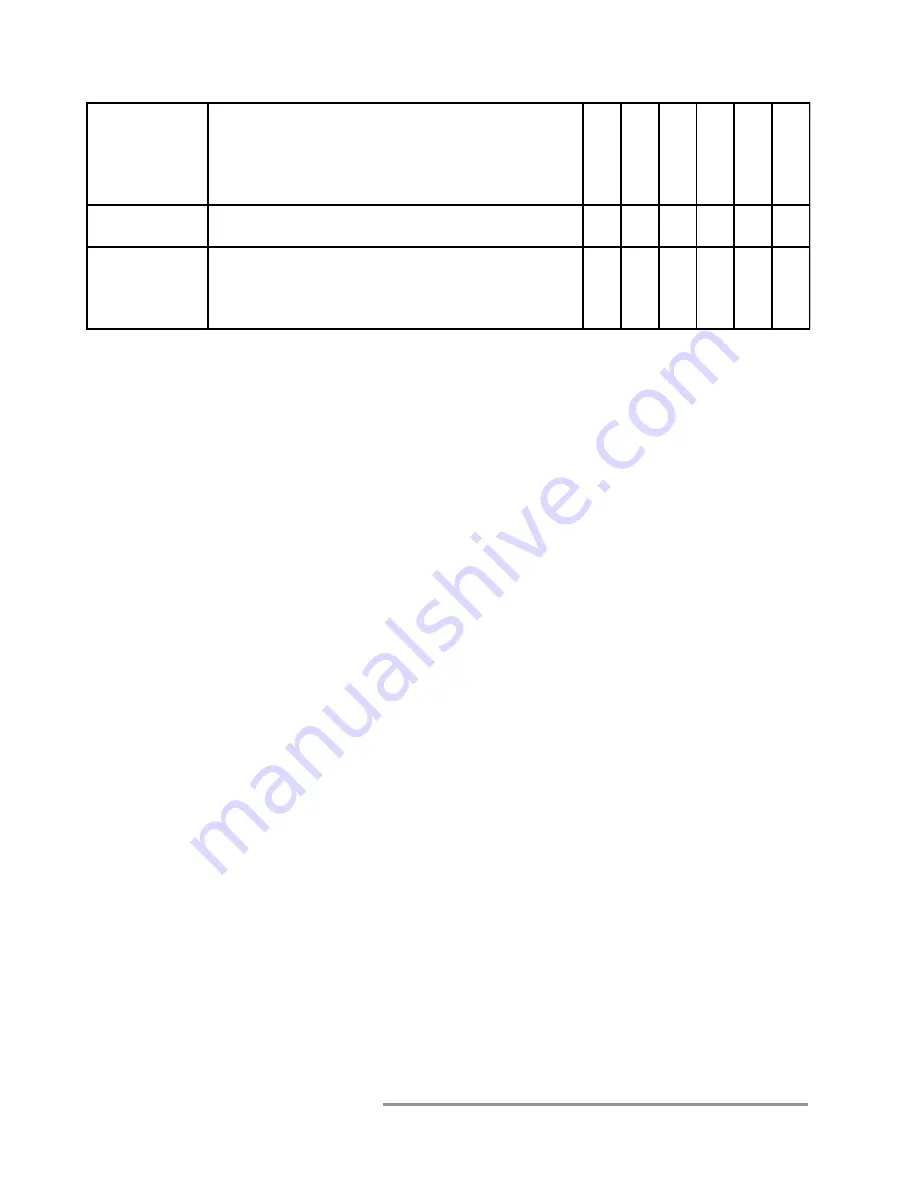
Eclipse Linnox Model CCS-LS, Installation Guide 159, 2/20/04
19
M
AINTENANCE
(C
ONTINUED
)
Flame safety
·
·
Check the interlocks by simulating fault conditions.
Resolve all flame safety problems before re-
starting the burner.
Replace the UV sensor within the time frame as
specified by the supplier.
x
x
Igniter /
flame rod
·
Check and clean or replace the igniter / flame rod
x
Thermal
overlaod
·
Check the direct burner surroundings for signs of
excessive corrosion or deformation due to
thermal overload. Repair or replace insulation or
thermal protection shields if necessary.
x
x