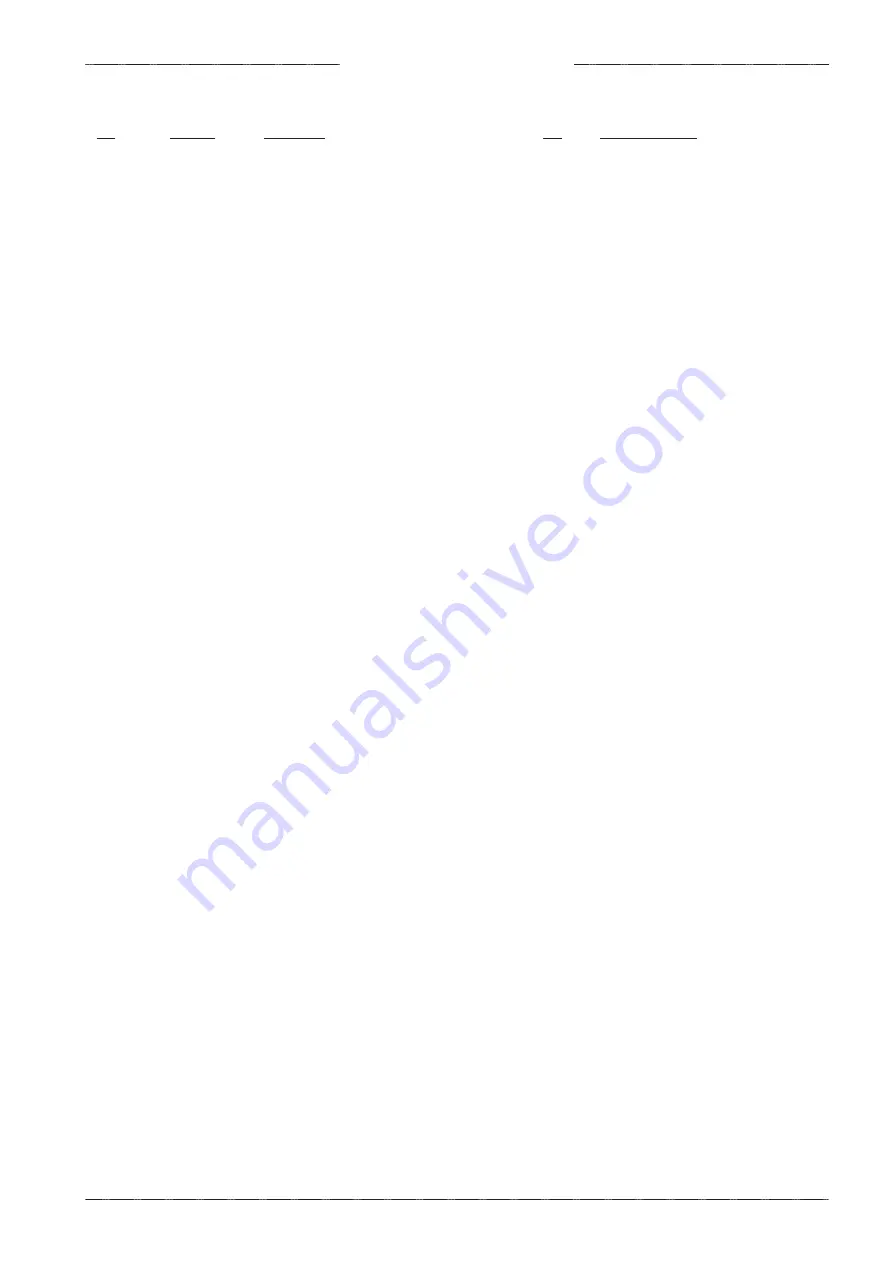
MEL-13
Kraftformer KF 170 PD
2018-05-09 | ECKOLD AG
Machine Spare Parts List (MEL)
Pos
Item No.
Designation
Qty
Type / Dimensions
023.125.0001
Pneumatic cylinder
1
023.910.0273
Bolt
2
2
023.910.0274
Washer
2
3
023.910.0272
Flexible mounting block
1
4
023.910.0271
Flange
1
5
023.125.0025
Piston
1
6
023.910.0163
Cylinder tube
1
7
023.910.0160
Flange
1
8
023.910.0164
Piston rod
1
9
023.910.0162
Guiding pipe
1
10
254.027.0020
Articulatet head
1
Durbal BEF D 14-H7
11
265.021.6051
Guiding ring
1
BS 50702-0200-C-10 D 20 mm
12
021.400.1004
Pressure spring
1
Dm 32 x d 3.5x Lo 230
13
258.340.0037
Safety-ring for shaft
1
DIN 471 d 45
14
252.000.0425
Cap screw
4
DIN 912 M 8x120
15
265.021.5030
O-ring seal
1
0352-8307 D123.19x5.33
16
265.021.6705
Guiding ring
1
BS 50702-1400-A-10 d 140 mm
17
265.022.0122
Turcon glyd ring
1
PPT 0301400-280 / D140.0x5.9x3.45
18
265.021.5060
O-ring seal
1
0160-8307 D133.0x2.62
19
252.000.0319
Cap screw
2
DIN 912 M 6x70
20
277.000.1010
L-type plug connection
1
QSLV-1/4-10
21
277.002.0108
Synthetic hose
1
PUN-10 x 1.5 x 420 lang
22
277.000.2112
Reducing nipple with sealing ring
1
Bosch G1/2 - G1/4
23
277.000.0416
Reducing nipple with sealing ring
1
D - 3/8 i - 1/2 a
24
277.003.1902
Quick air relief cock
1
NG 12-G1/2"
25
277.003.0410
Muffler
1
G 3/8"
26
252.000.0407
Cap screw
1
DIN 912 M 8x25
27
023.910.0317
Clamp
1
28
266.011.0895
Pressure spring
1
Dm 8 x d 0.8 x Lo 68
29
277.000.4118
Sealing ring
1
G 1/2"
Summary of Contents for 021.200.2500
Page 55: ......