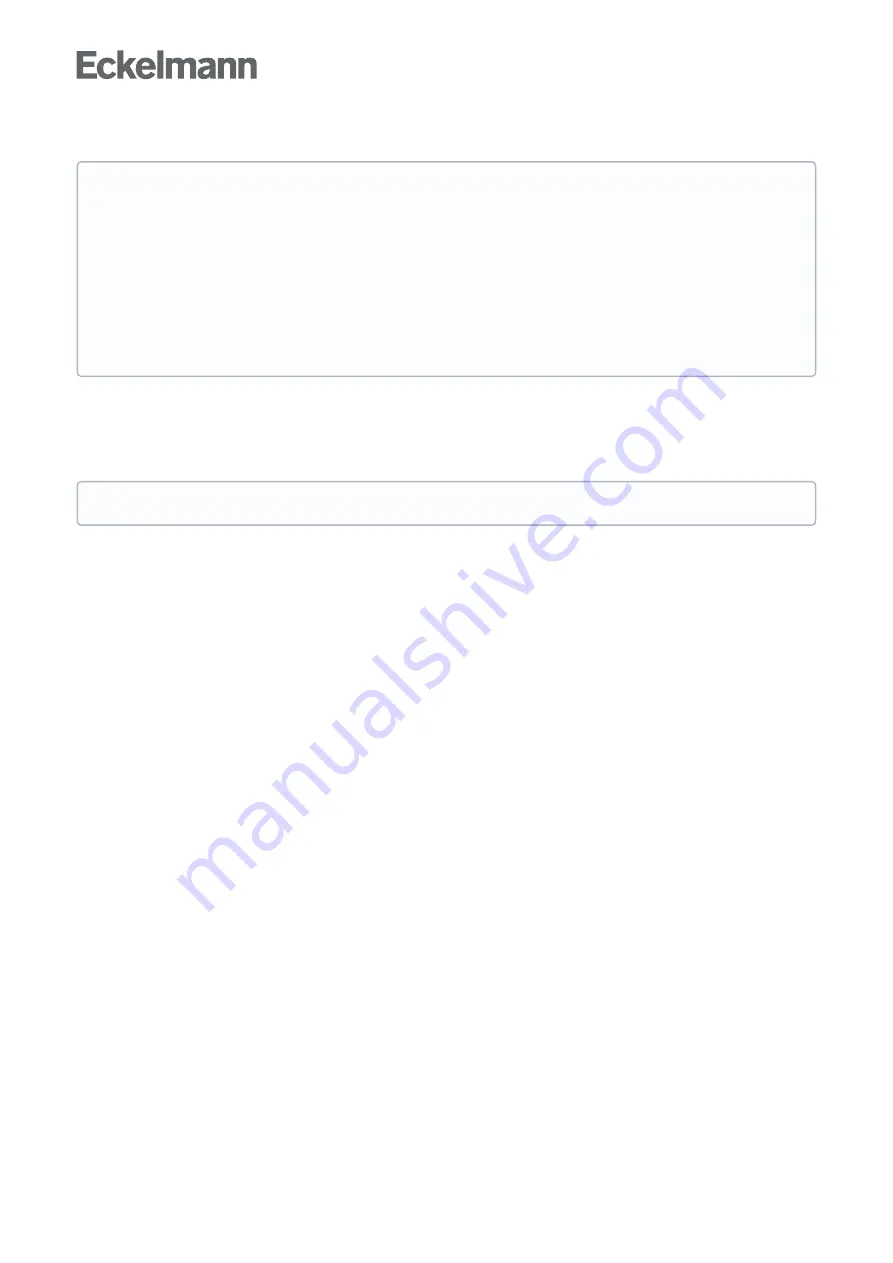
08.11.2022
7/23
2.1 Disclaimer in the event of non-compliance
These operating instructions contain information on the commissioning, function, operation and maintenance
of the controls and of the associated components.
2.2 Personnel requirements, requirements on staff
Special technical knowledge is required for planning, programming, installation, putting into service and
maintenance work. This work may
only
be performed by skilled, specially trained personnel. The installation,
putting into service and maintenance personnel must have training that authorises them to perform
interventions in the system and the automation system. The planning and programming personnel must be
familiar with the safety concepts of automation technology. Working on electrical systems
requires special
technical knowledge
. Work on electrical systems may only be performed
by instructed electrically skilled
persons
or under the guidance or supervision of such persons. The applicable regulations (e.g. DIN EN 60204,
EN 50178, DGUV Regulation 3, DIN-VDE 0100/0113) must be observed. The operating personnel must be
instructed in how to handle the system / machine and the controller and must be familiar with the operating
instructions.
ATTENTION
Warning of damage to goods!
In our experience, the transmission of fault messages is not yet functional during the putting into
service (no internet connection, no telephone line installed, etc.). It is strongly recommended in such
cases to monitor the controller via the CAN bus using a system centre, a store computer or an operator
terminal and to enable the transmission of fault messages, for example using a GSM modem via a
mobile telephone system. In standalone operation, or as an alternative to monitoring via system
centre / store computer / operator terminal, an available alarm contact on the controller must be used
to enable the transmission of fault messages via a telephone network.
For more information, refer to
E*LDS basics, safety instructions, CAN bus & Modbus
Observance
of these operating instructions is a prerequisite for safe and trouble-free operation.