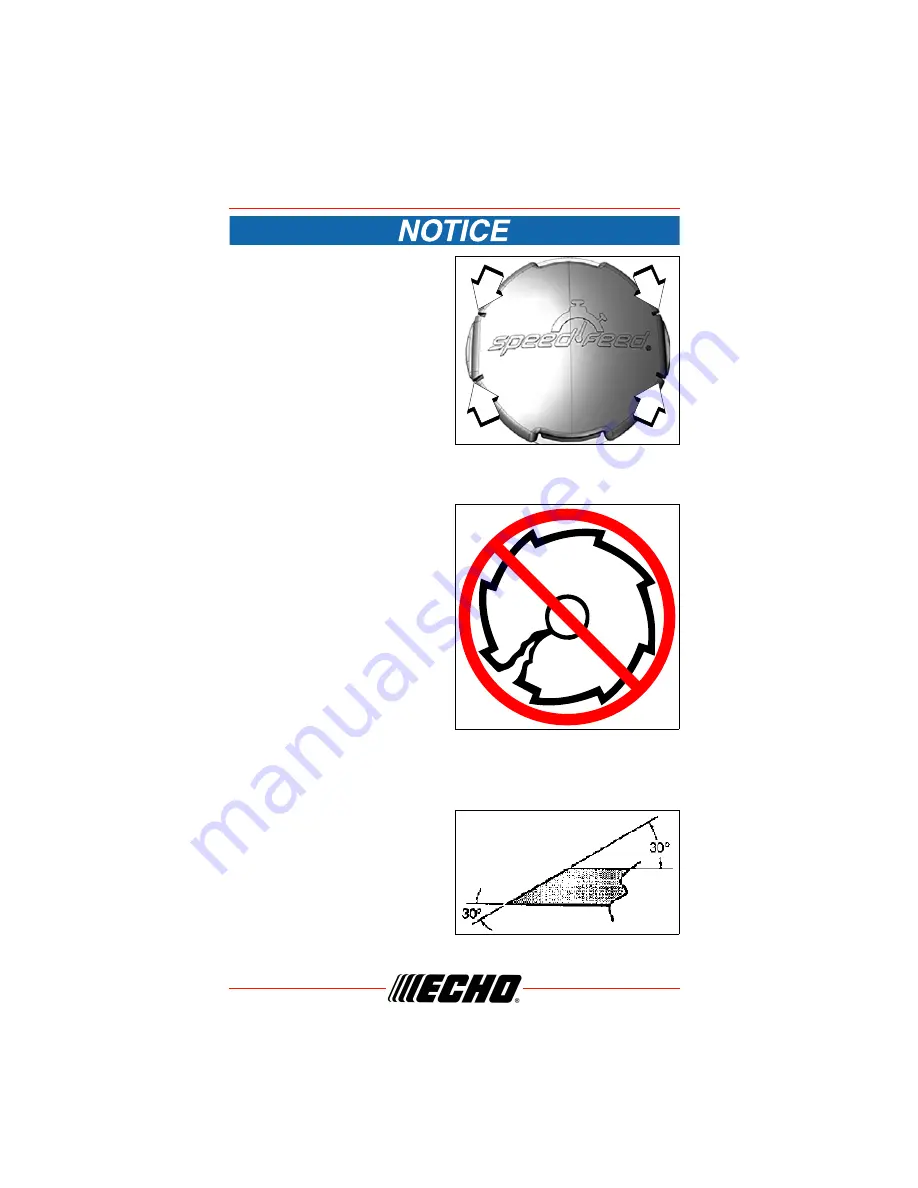
MAINTENANCE
SRM-2320T
42
X7732278300
© 08/2019 ECHO Inc.
When the wear indicators
located at the bottom of the
Speed-Feed
®
head are worn
smooth, or if holes appear,
replacement of the cover or the
entire Speed-Feed
®
head is
required.
Sharpening Metal Blades
Several styles of metal blades are
approved for use on the Brush
Cutter. The 8-tooth blade can be
sharpened during normal
maintenance. The clearing blade
and 80-tooth blade require
professional service.
Before sharpening, CLOSELY
inspect blade for cracks (look at the
bottom of each tooth and the center
mounting hole closely), missing
teeth and bending. If ANY of these
problems are discovered, replace
the blade.
When sharpening a blade, always
remove the same amount of materials from each tooth to maintain balance.
A blade that is not balanced will cause unsafe handling due to vibration and
can result in blade failure.
1.
File each tooth at a 30° angle a
specific number of times, e.g.,
four strokes per tooth. Work
your way around the blade until
all teeth are sharp.
2.
DO NOT file the ‘gullet’ (radius)
of the tooth with the flat file. The
radius must remain. A sharp
corner will lead to a crack and
blade failure.